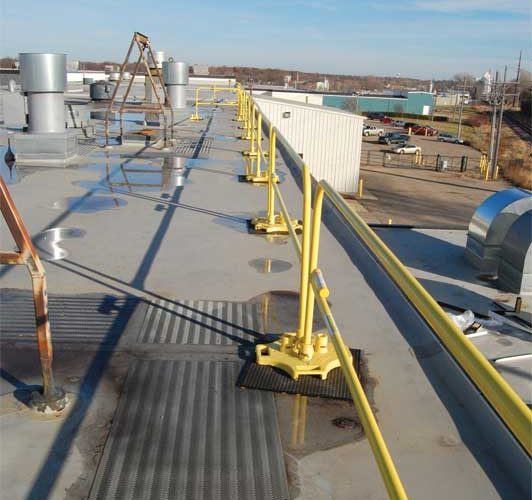
Active fall protection systems
Active systems depend on the user to be effective. They typically involve tie-off anchors or harnesses—as in the case of personal fall arrest systems—and feature a variety of requirements. For example, tie-off anchors must be able to hold a 2268-kg (500-lb) load at minimum and be certified by a structural engineer. They should also be inspected and recertified on an annual basis, per the regulations covering the area where the project takes place.
Additionally, fall retrieval plans must be implemented so when an accident occurs, the victim can be attended to within a certain timeframe (usually 15 minutes). The earlier the victim is given medical attention, the more likely it is the treatment can take effect and prevent a fatality.
All personnel must also receive adequate training for use of active fall protection systems according to 1926.503, Training Program. This training should cover the types of fall hazards most likely to be encountered by workers, along with the procedures for using, maintaining, and inspecting fall protection systems, the role of every employee in the use of these systems, and the limitations of each type of fall protection equipment.
Employers must verify compliance with this provision by submitting a written certification record for every trained employee. Training documents should also be regularly reviewed and updated. Further, any review of tie-off systems should be done in the presence of the building owner’s environment, health, and safety (EHS) representative.
In OSHA 1926.502(d), Personal Fall Arrest Systems, OSHA sets out standards for such arrest systems. There are two primary points to be aware of:
- body belts are not considered an acceptable form of a personal fall arrest system, but they can be used in compliance with 1926.502(e), Positioning Device Systems; and
- connectors shall be drop-forged or made of formed steel, pressed steel, or other materials with similar qualities, while connector finishes need to be corrosion-resistant, with edges smoothened to avoid damage to interfacing parts.
Even with training, there is still risk inherent in using active fall protection systems. Since individual workers can use these systems as they please, it is possible they will fail to install them correctly and become more susceptible to fall-related injuries or fatalities.
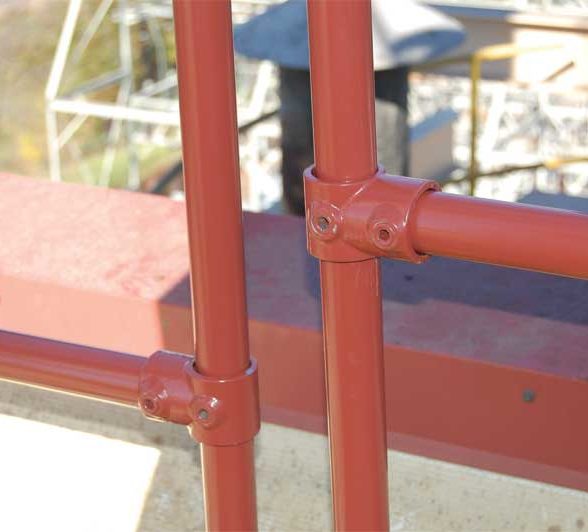
This is not to suggest active fall protection systems should not be used at all. If these systems are the best solution for the project and circumstances at hand, then they should be utilized, with their specifications made as clear and accurate as possible. In fact, it is better if active fall protection systems are used in conjunction with their passive counterparts.
Passive fall protection systems
Passive systems can function without any action from users. Once installed, they protect construction workers for as long as they are up. Passive fall protection systems need little to no maintenance, and even workers with minimal training can install and benefit from them. Non-penetrating guardrails fall under this category, providing numerous advantages.
Minimal damage
If penetrative fall protection systems are installed on roofs, employers run the risk of damaging the structure’s integrity and incurring additional, unnecessary costs. Non-penetrating guardrail systems minimize this risk. Given these systems’ ballasts are heavy enough to keep rails in place, but light enough to refrain from penetrating the roof—while meeting OSHA load requirements—non-penetrating guardrails protect both the workers and the structure.