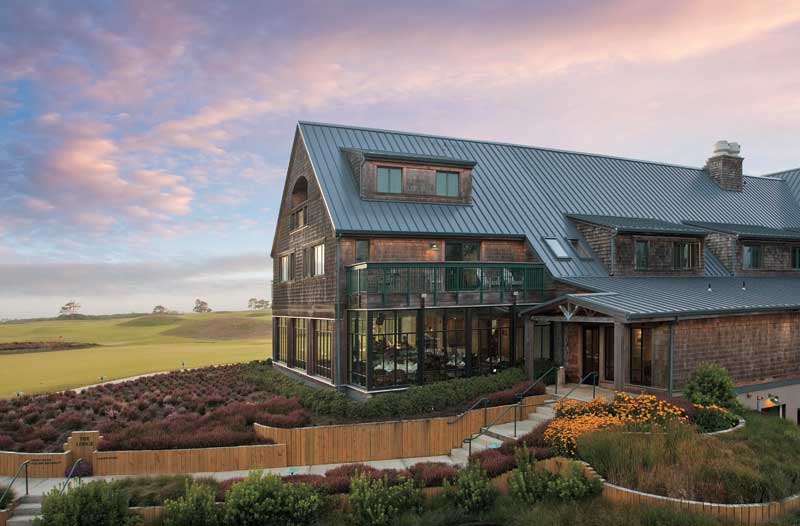
by Scott W. Moffatt
Although silicone-modified polyester (SMP) and super-polyester coatings are well-suited for specific applications, they cannot provide the same proven long-term performance as 70 percent polyvinylidene fluoride (PVDF) products.
While many SMP and super-polyester coatings are excellent products well-suited to various architectural and building product applications, the practice of marketing them as comparable alternatives to 70 percent PVDF coatings may cause architects and specifiers to select the wrong product for their applications.
This article examines differences between 70 percent PVDF, SMP, and super-polyester coatings, and explains why the first type generally retain its color and gloss longer than coatings based on the other chemistry.
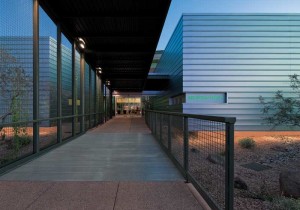
Photo © Timmerman Photography
The basics
Coil coatings are made from three basic ingredients: resins, pigments, and solvents.
Resins
Resins give coil coatings basic performance attributes such as resistance to abrasion, scratching, moisture, and ultraviolet (UV) light, as well as mechanical characteristics like adhesion, hardness, and flexibility during fabrication.
Coil coatings are formulated with several resin types, including acrylic, epoxy, polyester, and PVDF polymers. For applications demanding a highly durable coating surface (e.g. metal roofing, composite panels, building panels, and curtain walls), 70 percent PVDF coatings are regarded as superior because of their strong UV resistance. Due to their lower cost and harder finishes, SMP and super-polyester coatings are traditionally favored for applications such as warehouses, industrial, storage, and agricultural structures, and other non-monumental commercial buildings.
In recent years, some manufacturers have sought to position SMP and super-polyester coatings as viable, low-cost alternatives to 70 percent PVDF coatings. While it is true polyester coatings are more resistant to UV damage than early-generation coatings, they do not offer the same weatherability, color retention, and gloss retention as 70 percent PVDF coatings.
To understand why, it helps to know the chemical structure of various resins. PVDF resin molecules are composed of alternating carbon-fluorine and carbon-hydrogen bonds; the former are among the strongest in the chemical world. Consequently, they render PVDF resins chemically and photo-chemically inert, and, therefore, virtually immune to degradation from sunlight, moisture, acids, pollutants, and chemicals. That is the reason for their superior durability.
In contrast, molecules in SMP and super-polyester resins are based on carbon-hydrogen, carbon-oxygen, and carbon-silicone bonds. Since their molecular bonds are weaker, long-term exposure to UV light and environmental hazards eventually defeats the polyester coating’s structural chemical integrity, causing it to chalk or fade.
Pigments
Pigments are colorants made from fine powders. There are three types: organic, inorganic, and ceramic—their chemical structure determines their stability (i.e. ability to resist fading). Since ceramic pigments are made from metal oxides fused under high temperatures—instead of carbon-based pigments derived from chlorophyll or coal that break down more easily under environmental stresses such as UV light—they are the most chemically stable and fade-resistant. Consequently, they are the default choice for coatings warranted to satisfy the most demanding performance expectations, such as high-end architectural applications.