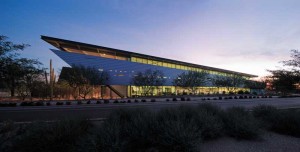
Photo © Timmerman Photography
Solvents
Solvents are carriers that make coatings easy to apply. They do so by solvating resin to a desired consistency and dispersing pigments evenly throughout the coating. Solvents have no effect on coating performance.
Ultimately, a coating is only as good as the sum of its parts. If a coating is formulated from strong, durable resins, but weak pigments—or weak resins and strong pigments—it has the potential to prematurely chalk or fade. Conversely, durable resins combined with strong pigment systems will deliver long-lasting durability and performance.
In short, a coatings formulation cannot be strong if any of its individual components are weak. High-quality raw materials are essential to a coating’s long-term performanceres.
However, they cannot match the long-term performance of 70 percent PVDF coatings for two reasons:
- SMP and super-polyester coatings do not have the chemical structure needed to sustain the long-term performance of 70 percent PVDF coatings.
- SMP and super-polyester coatings do not have long-term weather exposure data equal to 70 percent PVDF coatings, which have a 45-year history of proven durability on buildings around the world.
Since 70 percent PVDF coil coatings debuted in the 1960s, they have been continuously subject to South Florida exposure testing. In this testing, coatings are applied to metal panels and exposed at a 45-degree angle to South Florida’s notoriously harsh humidity and UV light, then measured at five-year intervals for chalk, fade, and other signs of environmental degradation.
Since then, numerous SMP and super-polyester coatings were introduced to the market. While experience shows older, high-quality polyester resins can perform well for up to two decades before they experience a dramatic fall-off in color retention and fade, newer polyester-based coatings formulations have not been available long enough to provide the five- to 10- and 20-year exposure testing needed to assess their long-term performance. Despite the lack of requisite performance data, many newer SMP and super-polyester coatings are warranted at terms comparable to 70 percent PVDF coatings.
Some coatings manufacturers seek to dismiss this concern by insisting performance data for new SMP and super-polyester coatings supersedes that of older products. However, new polyester technologies may in fact be superior to the earlier polyester formulations, but they cannot achieve the long-term performance of 70 percent PVDF coatings because ultimately, the molecular structure of the base polyester resins cause them to fail.
Coatings specifiers should also examine if and how their warranty distinguishes between vertical and non-vertical surfaces. Many warranties cover vertical and non-vertical surfaces differently because the latter (e.g. roofs) is more susceptible to failure. Seventy percent PVDF coatings purchased from proven, reputable coil coatings manufacturers should provide equal chalk and fade coverage for both vertical and non-vertical surfaces.
Chalk and fade
As explained earlier, chalking or fading directly results from the chemical breakdown of a coating’s base resins and pigments, which ultimately appear as a visible loss of color and/or gloss.
Chalk is the appearance of a powdery substance on a coating’s surface. In accordance with ASTM D4214-07, Standard Test Methods for Evaluating the Degree of Chalking of Exterior Paint Films, it is measured by rubbing the coated surface with a soft fabric and calculating the amount of powder picked up on a scale from one (extremely poor) to 10 (perfect), as depicted in Figure 1.
Fade is the loss of color calculated in Hunter ΔE units in accordance with ASTM D2244-11, Standard Practice for Calculation of Color Tolerances and Color Differences from Instrumentally Measured Color Coordinates. (Hunter ΔE units are an internationally recognized system for measuring fade or color loss on siding and building panels.) One ΔE Hunter unit denotes the smallest degree of color change visible to the naked eye (Figure 2).
While it may not appear so on paper, a difference of one or two points in a chalk rating—or more than five ΔE Hunter units in a fade measurement—can mean the difference between a coating that maintains its original appearance for 50 years from one that looks old much sooner.