ROOF INSULATION REQUIREMENTS |
In the drive toward net-zero energy buildings and ever-greater energy efficiency, expectations for building performance have rapidly progressed over the past several years. With each successive iteration of the generally accepted national energy standards (i.e. American Society of Heating, Refrigeration, and Air-conditioning Engineers [ASHRAE] 90.1, Energy Standard for Buildings Except Low-rise Residential Buildings, and the International Energy Conservation Code [IECC]), requirements for building envelope thermal performance have become increasingly stringent. For this reason, insulation considerations are an essential part of any reroofing project. In 2006, IECC recommended a roof insulation R-value of 15 for commercial buildings in most North American climate zones. Just six years later, in the 2012 edition, that R-value jumped to 20 for southern states and to 25 for most of the rest of the country, with the far northern states having insulation requirements as high as 30 to 35. R-value is a measure of a materials’ resistance to heat transfer and is the reciprocal of U-factor, which describes how well an assembly conducts heat. The higher the R-value of a building element, the better it is at protecting against heat loss. For reroofing projects on existing buildings, meeting increasingly rigorous insulation requirements can be challenging. Even where the project calls for a thin cool roof membrane and not a dense bed of planting media, the depth of insulation necessary to achieve the requisite R-value can impact door thresholds, flashings, walking surface elevations, guardrail heights, edge conditions, and other details. Considering all these implications during the design phase helps minimize problems in the field, when discovering increased insulation height prevents a bulkhead door from opening becomes a costly last-minute modification. |
Reflected solar radiation and glare
Before opting for a cool roof, it is worth preventing future problems by considering not only its impact on the energy use and sustainability of the building on which it will be installed, but also of the surrounding buildings. For roof setbacks or roofs surrounded by taller buildings, the assembly needs to be designed so the reflected sunlight from the roof surface does not create problems with undesirable glare and heat redirected into windows above.
Without appropriate design considerations, reflected heat may negate some of the energy benefits of a cool roof. Some studies have found temperatures above a reflective roof may be higher than those over a traditional darker-colored roof, which may impact rooftop equipment, conduits, wiring, piping, and other materials subjected to the reflected heat. In some regions, widespread use of cool roofs may have even broader climate implications, as the heat redirected back into the atmosphere may adversely impact rainfall, necessitating appropriate tradeoff measures. As such, owners and design professionals should analyze geographically dependent variables when designing and detailing a cool roof.
Controlling glare and reflected heat continues to be a concern for cool roofs, but this should not deter building owners and project teams from considering reflective roof materials for reroofing projects. Where code requirements mandate cool roofs, excessive heat gain is unlikely to be a widespread problem, and glare may be managed through low-emissivity (low-e) window coatings, daylighting controls, baffles, and other architectural elements. Specifying a combination of vegetated and cool roof systems for different roof areas can offer a customized solution balancing comfort with performance.
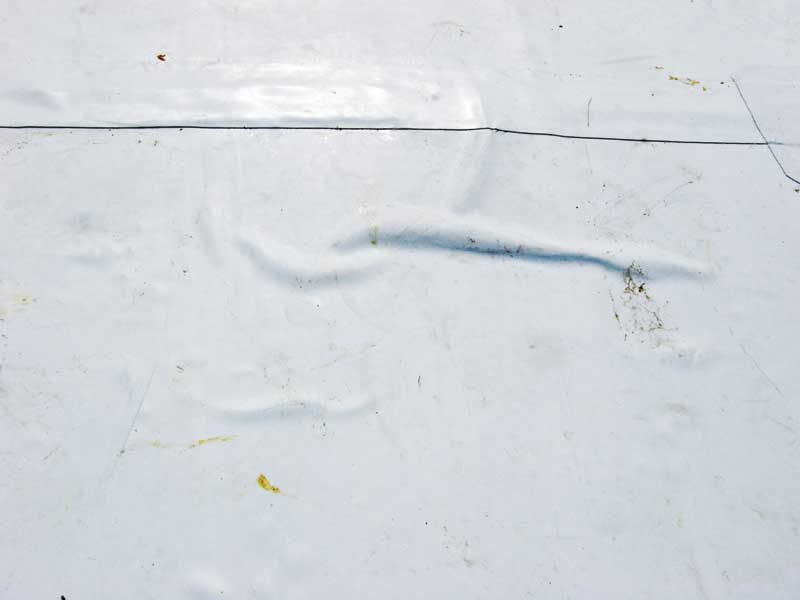
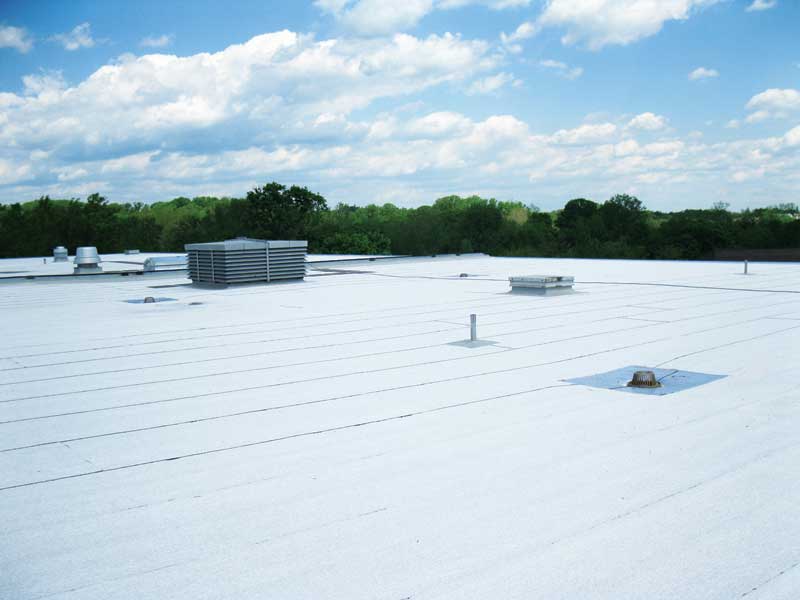
A step ahead
Even where building codes do not mandate increased insulation, vegetated or cool roofs, or other energy-saving assemblies, it is still good practice to opt for assemblies meeting national standards for energy performance. The list of states and municipalities that have newly adopted codes based on ASHRAE or IECC standards is constantly growing, with some cities, such as New York, enacting energy and building codes even more stringent than those at the state level. Rather than chase after evolving requirements, design/construction professionals should stay at the forefront of energy efficiency policy by choosing assemblies meeting or, better, exceeding national standards.
In general, building codes for energy performance are the lowest end of what is acceptable, with plenty of room for improved efficiency beyond what is mandated by law. Increasing insulation levels from 2006 IECC-required values to those mandated in the 2012 edition of the code, for example, has been shown to have a significant impact on electricity consumption; installing a cool roof covering over this increased insulation further cuts electric bills by reducing peak demand.
As building performance standards change, so too do the product offerings from manufacturers, which may mean a straightforward replacement of an existing roof with the same or similar assembly is no longer an option. Rather than an item to check off the to-do list, reroofing presents the opportunity to consider possibilities for increased efficiency, better indoor comfort, improved building user experience, and enhanced aesthetics. Although some new technologies, particularly vegetated roof systems, present a greater up-front investment, they can return benefits of long-term durability and create a sustainable building amenity.
Russell M. Sanders, AIA, is executive vice president and senior director of technical services at Hoffmann Architects, an architecture/engineering firm specializing in the rehabilitation of building exteriors. As one of Hoffmann Architects’ first employees, he has been with the firm for 38 years and has expertise in the technical details and design considerations for roof replacement. He can be reached via e-mail at r.sanders@hoffarch.com.
What a nice overview of these issues. Vegetative/green roofs are a great amenity for inhabitants and building owners and EPDM membrane is commonly used as the roof cover. A small correction … prior to the 2010 edition of ASHRAE 90.1, there was no requirement for roof reflectivity. That provision was added for the 2010 edition in Climate Zones 1-3. Your statement of “…in previous editions, reflective roof assemblies were the standard, irrespective of geographic region” is incorrect.
Green roofs have become incredibly popular and are being designed and installed at an incredibly rapid pace. As an addition to the “Waterproof design” in this article, I would strongly recommend installing a conductive mesh beneath the waterproof membrane. This will now, always allow for an Electronic Leak Detection to be performed after completion of such elaborate vegetated roofs and/or any other amenity space idea. My company specializes in both high and low voltage testing (leak/integrity), Gaussen’s “Real Time Leak Detection and Alert Systems” (24/7 live monitoring) as well as installing the conductive mesh.
The recommendation to perform a leak detection prior to installing the green roof components is spot on and will only save time, money and frustration. You can find our specification for Electronic Leak Detection at http://atlanticleak.com/eld-specification/.
Great article!!