by Michael Russo
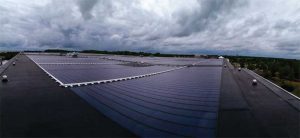
As the wind picks up speed, the loose-laid, single-ply roof membrane reacts almost instantly, a subtle ripple coursing through the tough 60-mil sheet. As air is forced through the perimeter roof vents, the negative pressure kicks in, forcing the membrane tight against the insulation below. At the same time, the wet polyisocyanurate (ISO) left in the existing roof system begins to dry out.
It is the negative pressure roofing system in action on a retrofit. Also referred to as a ‘wind-vented’ roof, the design is protected by more than 25 patents and is proven in thousands of roof installations encompassing approximately 9 million m2 (94 million sf) in the United States, Canada, andthe Virgin Islands.
The science behind the system is simple—no smoke and mirrors. When an air seal is formed using a newly installed single-ply membrane, a low-pressure condition is created on the underside of the roof. Any moisture in the existing wet roof insulation is pulled up through perimeter roof vents. It is the same phenomenon as seen in a low-pressure weather system forcing water vapor out of the ground. The U.S. Department of Energy (DOE) has documented the system’s ability to dry out wet roof insulation.
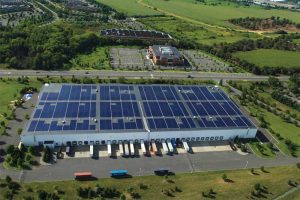
Further, a ‘dry-out’ rider is an optional part of the guarantee. The rider says the manufacturer will come back in two years and cut a core sample from the roof to ensure at least 90 percent of the existing insulation is dry. Based on previous experience, the dry-out period may be shorter depending on the saturation level of the insulation.
How wet is wet? One independent manufacturer’s representative recalls a recover over a cold storage facility in Kansas City, Missouri, that probed the limits of what the design can do. “When I pulled the core on the original roof, the core machine filled up with water,” says the representative. “A fish might have lived in that roof, it was so wet, but the recover installation was approved.”
On a routine leak call on the same building four years later, the roofing professional re-cored the roof in the same spot.
“I pulled out the fiberglass (insulation) and wrung it out in my hands—no evidence of liquid water—the insulation just felt cold, so probably some residual moisture in the fiberglass.”
According to Timothy Fogue, who spent two decades serving as project designer at Iowa State University (ISU) in Ames, the wind-vented system’s ability to dry-out wet roofs has proven itself on numerous projects at the school over the past 15 years. ISU has almost 139,355 m2 (1.5 million sf) of roofing in service on its main campus and two branches in Vinton and Council Bluffs.
Fogue had documented one such success story on the Scheman Building at the Iowa State Center. The structure’s metal deck was inspected from below before installation of the wind-vented roof. The existing built-up roof (BUR) included a vapor retarder mopped to the steel deck. At some point, this system had been recovered with a single-ply membrane and insulation. An infrared scan of the roof showed areas of wet insulation. A cored area revealed the insulation in both the existing roof systems was saturated, but the deck was in good condition. The roof was then recovered with a single-ply membrane using the negative pressure roof design. The cored area with the saturated insulation was re-cored about 18 months after installation, and the roof system was completely dry, according to Fogue.
Standing up to Sandy’s fury
Hines & Associates has more than 30 years of experience in commercial roofing and has been directly involved in the repair, maintenance, and application of more than 2 million m2 (20 million sf) of roof membrane in the New Jersey/New York/Pennsylvania area alone.