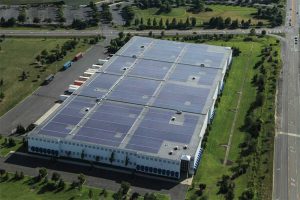
On October 9, 2012, Hurricane Sandy struck southern New Jersey, packing 129-km/h (80-mph) winds. Three negative pressure single-ply roofs that took direct hits from the storm remained intact and are still in service today. The Shore Casino in Atlantic Highlands, New Jersey, was one of the first establishments in the area to reopen for business in February 2013. A two-tenant office building currently owned by Adler Development in Cranberry, New Jersey, featuring an 18,581-m2 (200,000-sf) roof and solar installation survived the storm undamaged. A 46,452-m2 (500,000-sf) ethylene propylene diene monomer (EPDM) roof with polycrystalline solar panels that was completed in 2012 in Vineland, New Jersey, using the negative pressure roof system also survived the hurricane. The roof designer chose EPDM for its long-term weatherability and the wind-vented roof for its solar-ready wind resistance on buildings in coastal areas. The negative pressure roof system held the EPDM membrane flat to the roof substrate, and the ballast weight of the solar racking system held the solar panels in place through the storm.
“Unlike other roof attachment methods, the stronger the wind blows, the more the roof assembly is pulled to the substrate,” says Jim Hines, president of Hines & Associates, Oceanport, New Jersey. “The system has proven itself twice on the same roof at Miami International Airport [Florida] during Hurricanes Gloria and Andrew in 1985 and 1992, respectively.”
Other benefits of the wind-vented system documented by Fogue include:
- reuse of existing insulation instead of removal and disposal, resulting in significant cost savings;
- restoration of insulation value to the roof, with the option to increase R-values;
- promotion of airflow through the roof system to eliminate potential mold growth;
- less noise and disruption for building occupants during application; and
- easier maintenance compared to ballasted roof systems.
“No roof system is perfect for every situation,” says Mark Hanson, president of Central States Roofing in Ames, Iowa. “However, when attempting to win over a property owner, we often find the wind-vented roof is the best solution. Two of the primary reasons for this are cost savings and ease of installation.”
All of these benefits add up to a recover system that is less expensive than adhered roofs where insulation has to be removed.
“The roof system is also beneficial if you are working within a tight deadline,” adds Hanson. “This is often the case with schools and universities looking to reroof during a winter, fall, or spring break. We have successfully committed to coming in on a Monday and finishing the roofing work by the end of the week.”
While most recover systems require a cover board, the wind-vented design allows contractors to install directly over existing adhered single-ply membranes if the insulation below is secure.
Another big advantage of the system comes into play over a non-nailable deck or when roof fasteners might protrude through the ceiling and be visible to occupants inside. Roof fasteners are not required with the wind-vented system, while traditional roofing options require a tear-off down to the non-nailable deck. Hot mopping, cold adhesives, or low-rise foam are then necessary to adhere the insulation or new membrane.
However, caution is recommended when recovering over non-air permeable roof decks like poured-in-place concrete because the integrity of the deck’s air seal must be ensured before reroofing. Particularly on older buildings, pipes or penetrations may have been disturbed or removed from non-permeable decks, compromising the air seal of the substrate. If the deck is visible from the top or underside, penetrations can be easily sealed with foam packs as needed. If the roof deck is inaccessible to visual inspection, a number of options can be used to ensure an air seal over
the existing system.
Simple concept, easy installation
When specifying the wind-vented roof system, the design burden on the roofing professional is light. The number and layout of the roof vents is determined by building height, parapet walls, and a variety of other factors determined by the system manufacturer. On average, about 12 vents are needed for a 1394-m2 (15,000-sf) roof.