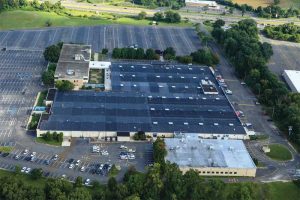
These perimeter vents are flashed like an ordinary pipe penetration, with the option to buy pre-flashed products. Each one-way vent stands about 406 mm (16 in.) high, with a small bladder and cap to prevent moisture from entering the pipe opening.
Roof penetrations, drains, curbs, and perimeter edge details are sealed with a rope-like, 19-mm (3/4-in.) thick, square-shaped butyl caulking. When specifying thermoplastic polyolefin (TPO) or polyvinyl chloride (PVC) single-ply membranes, only a standard termination bar detail is required. This detail functions as an air seal and can be used at deck level, or the base of a wall on non-nailable decks.
Non-reinforced EPDM membrane can also be used with the wind-vented roof. Oriented strand board (OSB) is mechanically attached with the butyl air seal rope sandwiched between the OSB and the existing roof. The EPDM membrane is then loose laid and adhered to the OSB with bonding adhesive about 0.6 m (2 ft) from the perimeter of the roof. This prevents air from the outside edge of the building from entering beneath the roof system. On existing gravel surfaces, a 13-mm (1/2-in.) gypsum cover board is used in the field of the roof and then fully adhered to OSB with bonding adhesive 0.6 m from the perimeter.
“Even with EPDM’s tendency to shrink, we have never seen the bond between the fully adhered EPDM membrane and the OSB broken,” says Chuck Beyer of Beyer Roof Sales, a roofing contractor in Clear Lake, Iowa. “Also, the system is continually being dried out, with any moisture pulled up through the perimeter roof vents to prevent degradation of the OSB.”
However, depending on the roof design, special precautions may be required when using OSB horizontally on the exterior of the building envelope due to the material’s vulnerability to moisture.
“The installation of the roof system is very easy,” says Hanson. “Our crews know exactly where to place the roof vents, and the entire process of air-sealing the roof is not problematic at all.”
The wind uplift resistance of the system can be another advantage due to the increasingly stringent requirements adopted by the International Building Code (IBC). However, local codes can vary widely on wind-resistance requirements, and the wind-vented roof will not be appropriate for all jurisdictions. One example is the Miami-Dade County in Florida, where the building code requires a wind resistance of up to 282 km/h (175 mph). It is advisable to consult with the manufacturer about local wind resistance requirements before specifying the wind-vented design.
Another area of concern, as mentioned earlier, is on older, non-air permeable decks, such as poured-in-place concrete, where missing penetrations such as pipes or curbs can ruin the air seal required by the wind-vented system.
“You cannot see any of this from the roofing side of the deck,” says Beyer, “and if you cannot inspect the deck from the underside, you might be losing the air seal. Where access to the deck is possible, penetrations can be filled in with foam packs, but if I cannot examine the structural deck from the bottom side, I am not going to use the wind-vented system because I have no idea about the condition of the deck.”
As long as an air seal can be assured, roofing professionals like Beyer and Hanson have used the negative pressure roof system with EPDM (45 to 90 mils), TPO (45 to 80 mils) and 60-mil PVC membranes. In Iowa alone, Beyer has specified the system on 371,612-m2 (4 million sf) of school roofing since 2001.
“The system can also be incorporated into certain modified bitumen and built-up roofing designs, although we have had less experience with these membrane types,” says Beyer, who retired this year.
Though the negative pressure roof system was introduced in 1986, it remains a niche design option in the single-ply roofing industry.