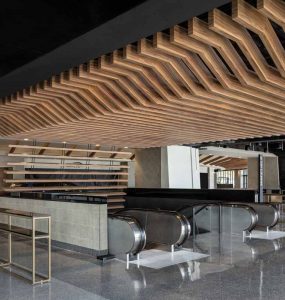
From concept to reality
With so many variables involved in the ceiling’s design, it was essential for components to be fabricated with precision, schematics to be drawn with detail, and installation to be carried out with accuracy.
Pope and his team worked hand-in-hand with Gensler’s designers to develop detailed computer-aided design (CAD) models and to test specific beams and suspension assemblies for fit and coordination to achieve the seamless effect the design firm visualized before moving on to the installation. Once one rafter was tested and working in place in the model, the team was able to repeat the same basic calculations and process for the rest. While the rafters’ sizes and angles varied widely, the same basic process could be applied to cut and align each one.
“Our focus is on the installers and helping them meet the architect’s design intent as easily as possible,” said Pope. “That is true of any installation, but especially one of this size and level of detail.”
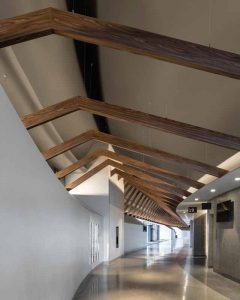
The testing process also helped streamline the original architectural design. Throughout manufacturing, the team found it could reduce the number of cuts required without negatively impacting the integrity of the design or its durability over the long run. The original design for the ceiling called for 40 angles per coliseum quadrant. Through tweaks in the calculations and plans, that number was reduced to 15 angles per quadrant, ultimately reducing the difficulty for the installers.
“We tweaked the design by consolidating the angles, and found we could maintain the visual effect of the changing peak height, but reduce the complexity of both production and installation,” explained Pope. “Repeating beam angles per quadrant created the opportunity to reuse engineering calculations and use the same beam-hanging process for the installers.”
This approach also reduced the amount of custom parts the manufacturer had to provide, which aided in controlling lead times and ensured installers could work to a tighter schedule.
Once test fitting was complete, manufacturers and subcontractors collaborated throughout extensive layout and engineering stages, as well as on precision fabrication of the components.
Richard Meyer, a subcontractor who worked on the installation, said the team excelled at providing drawings that offered “a nice guide to putting it all together. I do not think anyone’s really done that type of system before… there was definitely a lot of designing involved in this custom work. The installation went very fast.”
By reducing the number of angles and beams, making precision cuts, giving diagrams on how to seam the beams together properly with the brackets, and identifying placement of hanger points, the engineering team supplied the installers with everything they needed to simplify an otherwise complicated installation job.
Due to the in-depth planning, efficient engineering, and detailed guidelines, the installation phase went quickly and smoothly. Pope recalls only two phone calls back and forth between his office and the subcontractors once installation began.
“When the beams came together, it was pristine,” he said. “From a product development mockup stage, we were able to do a lot on the front end in order to make sure the beams came together and looked sharp.”