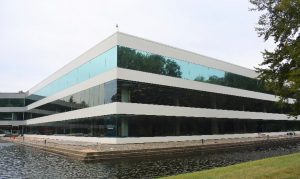
Photo courtesy Stuart Dean Company
Home to several high-profile tenants since its construction in the early 1970s, the 1 Rockwood office building in Sleepy Hollow, New York, underwent a complete façade restoration using a polyvinylidene fluoride (PVDF) exterior restoration coatings. The restoration project will help the building resist exterior fading and degradation for at least 20 years.
Preparing the surface
Building restorations provider Stuart Dean Company conducted the five-month restoration of the 3716 m2 (40,000 sf) of exterior aluminum panels. According to Chris Incorvaia, national manager of façade restoration for the Stuart Dean Company, the 20-technician crew started by preparing the surface for coating application.
“The aluminum panels had been previously field-painted with acrylic polyurethane,” he said. “That previous coating had degraded significantly due to ultraviolet [UV] exposure and weathering.”
PVDV coatings were an ideal choice for the project, Incorvaia said, because they can be used on previously painted surfaces. The coatings contain a water-based PVDF resin that does not need to be baked, making it ideal for air-dry, field-applied coatings.
The PVDF coating is weather-resistant and can be applied to a variety of substrates, Incorvaia added, noting that the coating system meets the same requirements of factory coatings using American Architectural Manufacturers Association (AAMA) 2605-13, Voluntary Specification, Performance Requirements, and Test Procedures for Superior-performing Organic Coatings on Aluminum Extrusions and Panels.
Proper surface conditions are crucial to achieving good coating adhesion and long life, so the Stuart Dean team was careful to fully prepare the surface. They started by removing sealants from all joints: metal to metal, metal to glass, and along window perimeters. These sealants were replaced 72 hours after the final topcoat. Next, they washed all surfaces to remove environmental contaminants such as chlorides and nitrates. Finally, they prepared the surface for the new coating by scuffing and sanding it to achieve a 1.0-1.5-mil anchor profile in accordance with NACE surface preparation guidelines.
Smooth application
Before applying the coating system, the Stuart Dean crew masked windows and adjacent surfaces to protect them. Then, they began the coating application, starting with one coat and 1.00-1.25 mils dry mil thickness (DFT) of bonding primer, which was roll-applied.
The bonding primer is a unique chemistry designed to adhere directly to metal and to tough coated surfaces, such as PVDF coating, siliconized polyester, and powder coatings.
The primer was followed by two coats and 2.00 mils DFT of metal restoration topcoat, also applied by roller. The PVDF coating provides a superior factory-like finish in a field-applied coating. Its advanced formulation is engineered for extreme UV protection, as well as resistance to algae, fungal growth, abrasion, dirt pickup, and stains.
The coating was custom matched with the topcoat in a color selected by the building owner—in this case colonial white.
A high-performance coating was critical for white exterior surfaces, especially in damp environments like this building,” a representative from the coatings provider said. “When traditional latexes and urethanes break down under harsh UV rays, the paint film degrades, turning chalky, and eventually erodes away.”
Throughout the entire coating process, the Stuart Dean crew paid special attention to ambient environmental conditions.
“The building is located on wetlands and is subjected to a high concentration of moisture and precipitation,” Incorvaia said. “To maintain quality control and ensure the long-term performance of the coating system, we diligently measured air temperature, surface temperature, relative humidity, and dewpoint.”