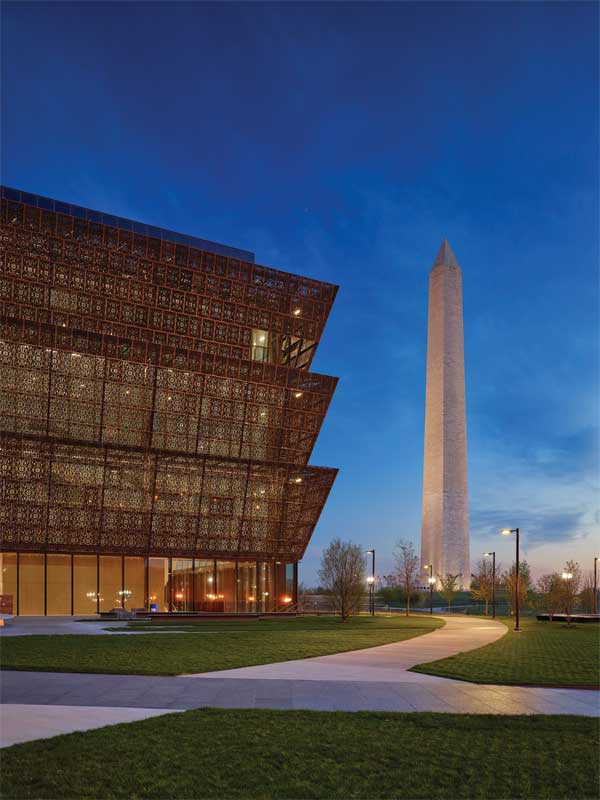
by Jonathan Carreiro, P. Eng., and Patrick M.B. Chan
In the age of high-performance design and construction, thermal bridges at balconies, slab edges, canopies, parapets, and rooftop connections cause these building elements to act like cooling fins, allowing heat to flow unimpeded from the interior through these uninsulated penetrations in the building envelope to the cold exterior environment.
While heating exterior penetrations wastes energy and increases carbon emissions and operating costs, chilling interior structures reduces comfort and allows condensation and mold to form on adjacent surfaces (see “Airtight Vapor Barriers Worsen Thermal Bridging Problems at Structural Penetrations” sidebar). Therefore, one must look for an alternative solution.
Structural thermal breaks (STBs) address these thermal weaknesses in the building envelope by ensuring continuous insulation (ci), thereby improving the overall thermal performance. They are changing the design philosophy to an “envelope-first approach.”
How STBs insulate
An STB is a fabricated longitudinal assembly of the same approximate width as the insulation layer of the building enclosure. It is a pre-engineered assembly containing loadbearing elements and insulation as opposed to thin insulation layers such as pads requiring additional design to make them work. It creates a structural insulated break between an exterior structural penetration (e.g. balcony, slab edge, canopy, parapet, and rooftop support) and the interior structure supporting it, minimizing thermal conductivity between the interior and exterior structures, while providing the specified loadbearing capacity.
Many building types and applications can employ STBs, with the most common being concrete cantilevered balconies. These engineered STBs contain high-strength stainless steel rebar tying in to both the interior and exterior concrete slab reinforcement. Stainless steel is approximately 70 percent less thermally conductive than regular carbon steel rebar. In addition to acting as a thermal separator in the concrete slab, the STB transfers the balcony dead and live loads back into the interior structural concrete slab. Other concrete STB applications include thermally separating concrete parapets on roofs, exposed slab edges, and architectural eyebrows.
STBs are also employed in steel construction to address thermal bridging from steel beams penetrating the building enclosure to support canopies and sunshades, as well as vertical steel applications like roof snow fences and roof anchors.
Lesser-known STB solutions address thermal bridging in concrete-to-steel connections (i.e. bolt-on steel balconies to concrete slab), concrete-to-wood, and steel-to-wood applications.
Compared to non-insulated connections, STBs can reduce thermal conductivity in the connection area by 90 percent for standard loadbearing scenarios, translating into average reductions in energy use and carbon footprint of up to 14 percent for the overall building per year. (For more information, click here.)
The reduction in BTUs required to heat the building also allows corresponding reductions in heating system size/capacity, resulting in savings on capital equipment and ongoing operation and maintenance of mechanical systems.
In the case of cantilevered balconies, STBs typically increase the warmth of adjacent interior floors by up to 15 C (27 F). (For more information, click here.)
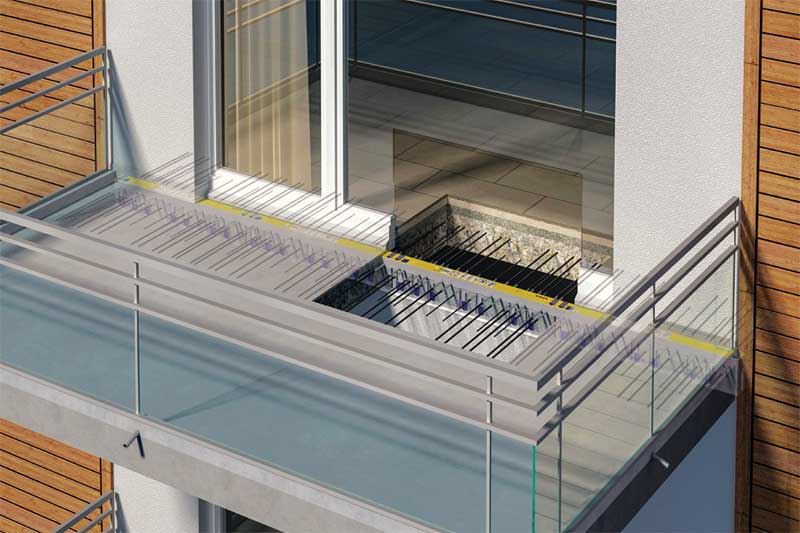
Photo courtesy Schöck North America
By allowing the interior side of structural penetrations to remain warm, STBs also prevent condensation, mold, and rust problems associated with today’s airtight vapor barriers and elevated interior humidity.
Since STBs are still a relatively new concept in North America, it is important suppliers provide local technical expertise, onsite support, and signed and sealed drawings by a professional engineer who is registered in the project’s state or city. Suppliers should also be able to furnish a comparative energy performance benefit of using STBs through 3D thermal modeling.
In Europe, gaping thermal penetrations through the building envelope are rare in high-rise construction because STBs are installed to simultaneously insulate and carry the loads of structural penetrations. The opposite has been true throughout North America where the adoption of STBs lags by decades. The reason for this is building codes.
Unlike European codes requiring continuous envelope insulation, North American “performance” codes contain loopholes of sorts allowing thermal deficiencies in one area to be offset by efficiencies in another.
Since thermal insulation of structural penetrations in North America remains discretionary, the adoption of STBs has been led primarily by:
- developers who intend to retain and operate the building for mid- to long-term profit;
- developers seeking Passive House, Leadership in Energy and Environmental Design (LEED), and other sustainability certifications;
- environmentally conscious developers and architectural firms; and
- projects such as museums with critical needs for preservation and protection of their buildings’ contents.
However, change is on the horizon as building codes regulating ci and energy efficiency tighten in the United States and Canada at the national, regional, and local levels.
As building codes evolve to mandate higher energy efficiency, thermal penetrations through the building envelope may soon go the way of single-pane windows and incandescent fixtures. Thus, design and construction professionals will benefit by keeping pace with current codes and understanding where new ones are headed.
Standards raised
Evolving building codes are narrowing the gap between decisions based on economic constraints and the ones reflecting broader, greener priorities.
The American National Standards Institute/American Society of Heating, Refrigerating and Air-conditioning Engineers/Illuminating Engineering Society (ANSI/ASHRAE/IES) 90.1, Energy Standard for Buildings Except Low-rise Residential Buildings, was updated in 2016 to require specific energy efficiency modeling for uninsulated assemblies in building envelopes, including balconies, perimeter edges of floor slabs, and parapets. This goes beyond past versions of ASHRAE 90.1, which did not effectively address, or allowed design/construction teams, under common interpretations, to ignore, these types of assemblies.
However, model building codes—established by organizations like ASHRAE, ANSI, IES, the International Code Council (ICC), the American Concrete Institute (ACI), along with Canada’s National Building Code (NBC) and National Energy Code for Buildings (NECB)—do not have the force of law until local authorities having jurisdiction (AHJ) adopt them. Therefore, the schedules and details of code adoption vary, and depend on regional climatic, economic, cultural, and political variables.
According to the July 2017 U.S. Department of Energy (DOE) code maps, no state has advanced to ASHRAE 90.1-2016. (For more information, click here.) Most state commercial building standards are based on pre-2007 codes. However, California, Massachusetts, and Washington employ regulations that are more efficient than ASHRAE 90.1-2013. The 2018 version of ICC’s International Energy Conservation Code (IECC) is expected to correspond to ASHRAE 90.1-2016 in many respects. States like New York and Illinois usually incorporate IECC revisions into their codes within the year the standards appear.
Good afternoon,
We have a high rise that needs insulation.The building has metal panels between the ceiling and walls, the metal panels were insulated 45 years ago and the insulation is almost non existent, therefore in winter the units are very cold and in summer very hot. Those metal panels are getting lose and making noise.
The building is located at 500 Laurie ave West, Ottawa, Ontario
If you need any more information our superintendent Derek Barkley can be reached at 613-261-9600
Please let us know if you can help.
Thank you very much
Marina Caron
Treasurer of the Board of Directors of Tower “A”
613-236-6767