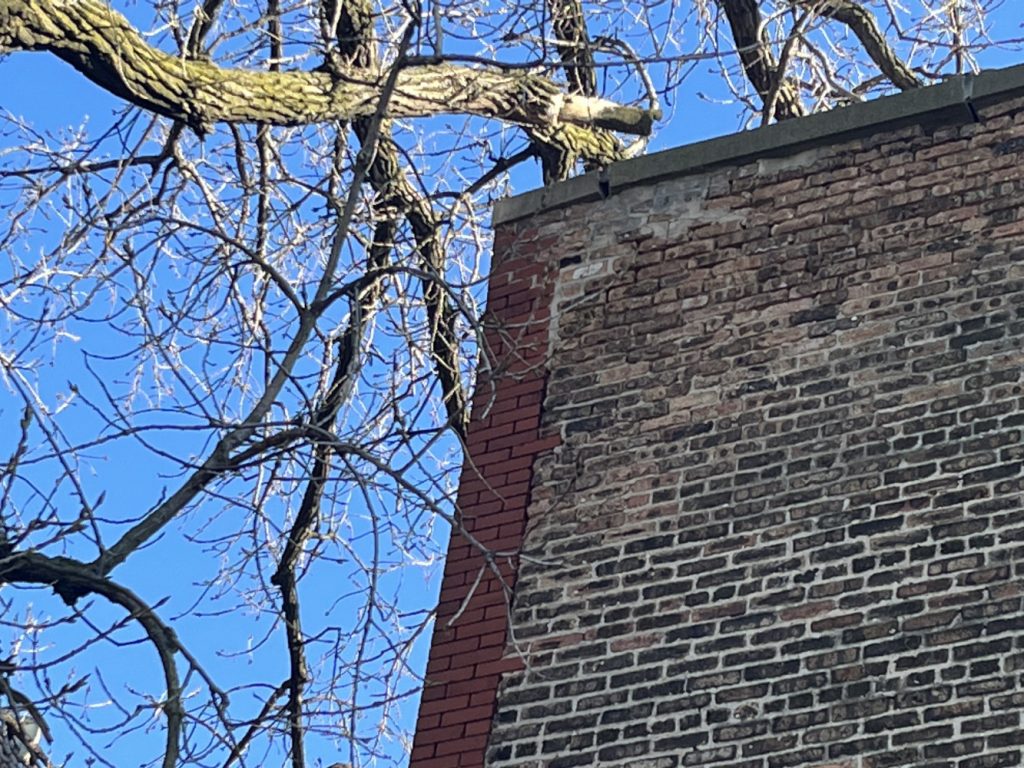
Historic masonry buildings often have unreinforced parapet walls, which lack vertical reinforcing in walls made of continuous multi-wythe masonry and capped with coping. Commonly used masonry materials include clay brick, stone, cast stone, terra cotta, clay tile, and concrete masonry units (CMUs), with lateral ties or reinforcing (if present) possibly extending between wythes, particularly in walls of multiple materials. In some historic buildings with projecting cornices below the parapet, the parapet wall’s mass may help counterbalance the cornice.
As these wall assemblies age and weather, routine assessments should be made for potential distress signs, including wall leaning or bowing, extensive masonry or mortar joint cracking, and displacement or deflection near corners and at structural framing. If observed, investigations are needed to identify the distress causes and develop appropriate repairs. Parapet wall distress may stem from unaddressed expansive or cyclical thermal stresses, material deterioration, or severe weather or seismic events.
Masonry materials can expand and contract at significantly varying rates depending on the material, and differential expansion can accumulate over time. Differential movement between dissimilar materials may lead to mortar joint cracking and wall leaning. For instance, in a brick masonry parapet wall with stone cladding, the brick masonry backup’s expansion might surpass that of the more stable stone cladding, causing the parapet wall to crack and lean outward. Material expansion might also cause displacement at building corners if not restrained by control joints. A recent project showed that insufficient corner restraint led to parapet leaning (Figure 1). Conditions linked to horizontal expansion can include vertical cracking, buckling, or parapet wall leaning.
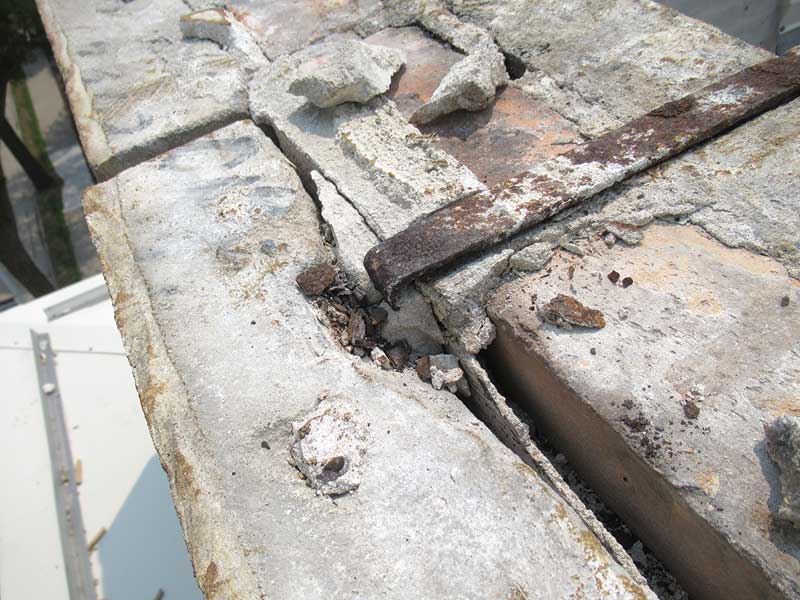
Weathering can deteriorate parapet walls over time, making them particularly vulnerable due to multi-directional weather exposure. Water penetration can corrode embedded steel in elements such as lateral ties, lintels, shelf angles, or anchors. A recent project showed how corrosion of lateral anchors led to spalling and displacement of stone cladding unit (Figure 2). Corroding steel expands, potentially pushing or lifting adjacent masonry, causing cracks, bowing, or leaning where corrosion occurs. Masonry saturation can cause freeze-thaw damage, such as spalling and cracking of masonry units, weakening the wall system’s structural integrity over time (Figure 3).
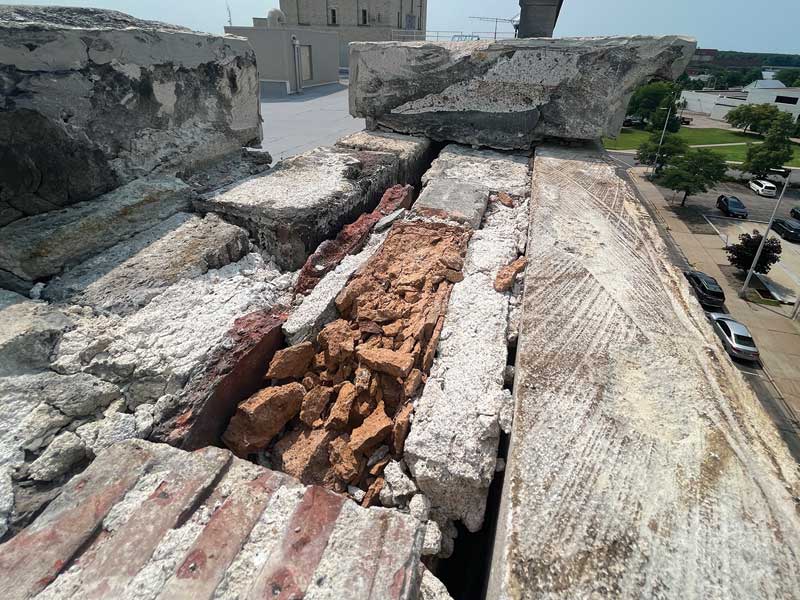
Besides issues tied to materials and construction, unreinforced parapet walls are more prone to failure from natural events like earthquakes, high winds, excessive rainfall, and flying debris during severe weather.
To determine an appropriate approach for repair, investigations must identify distress mechanisms and document the existing wall and roof structure, including concealed conditions. Repair options might include removal and rebuilding or in-place bracing, stabilizing, and repairing. Depending on the distress’s cause and extent, other methods, such as installing pins for missing or deteriorated lateral anchorage, may be considered. Any selected repair design should be performed in accordance with applicable standards to meet the anticipated wind, seismic, and other loads.
Authors
Kenneth Itle, AIA, is an architect and associate principal with Wiss, Janney, Elstner Associates (WJE) in Northbrook, Illinois, specializing in historic preservation. He can be reached at kitle@wje.com.
Mike Ford is an architect and senior associate with Wiss, Janney, Elstner Associates (WJE) in Northbrook, Illinois. He specializes in facade assessment and cleaning. He can be reached at mford@wje.com.
The opinions expressed in Failures are based on the authors’ experiences and do not necessarily reflect that of The Construction Specifier or CSI.