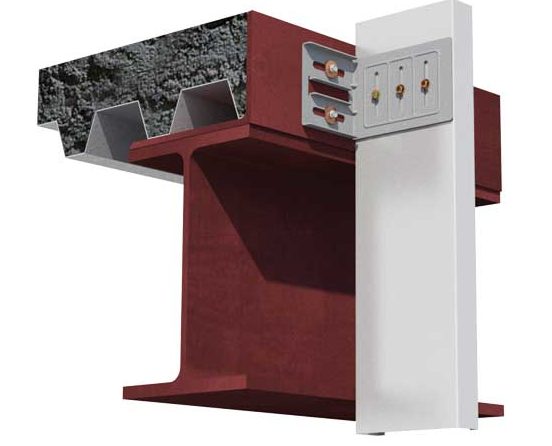
Images courtesy ClarkDietrich
Deflection connectors
Deflection or movement connections are designed to permit movement of the primary structure of the building without imposing any axial loading onto the exterior curtain wall or interior head of wall. Movement of the primary structure may result
from thermal expansion and contraction, seismic disturbances, foundation settling, or normal head-of-wall compression. Deflection connectors are used in an array of framing conditions, including exterior walls, bypass, head of wall or infill, and interior head of wall.
When designing for a deflection connector, the two primary considerations are deflection and standoff distances.
Deflection distances
Deflection distances are the measure of the maximum vertical distance the primary structure is anticipated to move due to the imposition or removal of
‘live loading.’
Standoff distances
Standoff distances are the space between the secondary and primary frames. The former is the curtain wall assembly made of cold-formed steel framing, while the latter is the main building structural support that usually consists of red iron or concrete. The standoff distance allows for the framer to install the cold-formed framing in a ‘true’ line, while the structure of the building may vary either ‘in or out’ or out-of-plumb from floor to floor.
Corrosion protection
As with other cold-formed steel framing products, connectors are protected from corrosion by a coating metallurgically bonded to the steel substrate. There are various coatings available, with the minimum being a G60 zinc coating as found in Table 1 in ASTM C955, Standard Specification for Cold-formed Steel Structural Framing Members. Epoxy-based or semi-metallic coatings that supplement the zinc coating or provide equivalent protection are also available for severe environments. Code-compliant and marketed under a trade name, they can be an economical choice.
Certain environments have high potential for corrosion. These include areas exposed to ocean salt air, fire retardants, fumes, fertilizers, preservative-treated wood, de-icing salts, and dissimilar metals. For these locations, it is possible to augment the level of protection by increasing the coating thickness. In such circumstances, G90 is the most commonly specified next step up; in rare, extremely harsh conditions, a G120 coating could be justified, but the cost implications should also be weighed.
It is common to see corrosion in outdoor applications, but this does not mean the load capacity has been affected or failure is imminent. (White rust is the light film that forms on the surface of a hot-dip galvanized connector as a natural result of the contact of the zinc with oxygen, called oxidation.’ This is harmless. In outdoor applications, it is not unusual to see some corrosion of a connector [i.e. red or brown rust] on the edges of a connector. Despite this, the connector is still being protected against corrosion by the ‘galvanic,’ or sacrificial action of the zinc; the connector is still able to perform as designed. If significant corrosion is suspected, the connector should be inspected by a qualified engineer or inspector. If the area in question takes on a black appearance, then enough zinc has been lost and the steel substrate has begun deteriorating. In normal conditions, this is a process that can take decades.) When significant corrosion is apparent or suspected, the framing members, fasteners, and connectors should be inspected by a qualified engineer or inspector. Replacement of affected components may be appropriate.
Some wood-preservative and fire-retardant chemicals and retentions also pose increased corrosion potential, and are more corrosive to steel connectors and fasteners than others. Connector manufacturers can provide specific guidance on the interactions of their products with the wide variety of wood treatments.