By Thomas J. Taylor, PhD
When it comes to roofing material, it is helpful to know the length of its lifespan—after all, no one can afford to put on a new membrane and simply wait to see how long it lasts. Building owners need assurance of roof lifespan so they can determine when a replacement might be needed, and manufacturers need to determine membrane warranty. Like building owners, manufacturers cannot wait and build a test roof to determine its longevity. If a test roof were built, where would it be located? In a hot, sunny environment like Arizona or a wet, damp environment like Washington?
This is why an accelerated weathering test is needed. Weathering is when a material shows the effects of sunlight, ultraviolet (UV), heat, and rain on its exposed surface. Accelerated weathering is the simulation of these conditions using special environmental chambers and instruments to speed up the process and measure its effects. Many industries use accelerated weathering, such as paint producers, automobile suppliers, and construction product manufacturers. For example, paint manufacturers employ accelerated weathering to see if a color fades during aging, if the paint peels and cracks, or if any gloss is retained. These are all important characteristics for consumers to know before they make a purchase.
Thermoplastic polyolefin (TPO) is known to be very resistant to standing water. It is even used as a pond and pool liner because it is not affected by repeated freeze and thaw cycles. However, TPO weathers from the effects of UV and heat. Simulating this kind of heat is simple, and an oven is used. There are many options available to simulate UV testing, including indoor and outdoor techniques.
Weathering affects the field of the membrane. In TPO assemblies, the top layer cracks, eventually down to the scrim. The second potential issue with TPO roofs is erosion of the top layer, which can lead to exposure of large areas of reinforcing fabric. During accelerated weathering testing, inspectors look for surface cracking and weight loss. Any significant weight loss signifies the membrane is eroding away.
Natural sunlight testing
Since building a roof sample and leaving it in the natural sunlight for 20 to 30 years is not an efficient or practical means of testing, a new testing method using mirrors and natural sunlight was developed. For example, if 10 mirrors are used, only two years of exposure may be needed to simulate 20 years of sun.
The Q-Lab Corporation’s Q-Trac sunlight concentrator located in Buckeye, Arizona, uses 10 mirrors that track the sun, exposing samples to almost year-round concentrated sunlight. The samples are sprayed with water once per day. This is known as the EMMAQUA test (equatorial mount with mirrors for acceleration with water). However, this method of testing can still take too long for some manufacturers.
Photo courtesy Q-LAB CORPORATION
The Ultra-accelerated Weathering System (UAWS) was developed by National Renewable Energy Laboratory (NREL) and collaborators from the Institute of Laser Optic Technology and Atlas Material Testing Technology. It uses 29 reflective facets, which initially caused samples to melt during early development work. Each facet has a 96-layer vacuum-deposited coating on the surface, concentrating the UV portion of natural sunlight, but filtering out some of the infrared rays.
UAWS is capable of collecting approximately 17,000 MJ/m2 total ultraviolet radiation (TUV) annually in Arizona. This is about the same amount of UV deposited over 60 years of Florida exposure (i.e.16,800 MJ/m2).
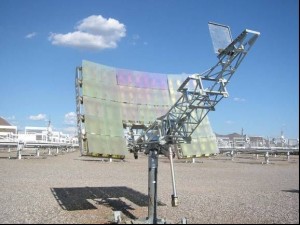