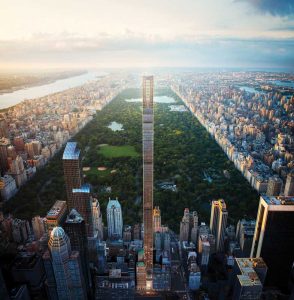
At the end of the powder gun, there are electrodes. Upon firing the powder gun, the powder is discharged and picks up the electrostatic charge from the electrodes at the end of the gun. As the substrate is grounded, the powder is attracted toward the parts. A film of powder is built up to the required thickness on the part, and the coated parts go into the oven.
Each powder comes with its own cure schedule that informs the coater how hot the oven should be and for how long it should cure. Once the substrate heats up and reaches the designated temperature, the powder melts, flows, gels, and cures, leaving a beautiful, durable, scratch resistant film.
Sustainable design
Powder coatings deliver an impressive array of sustainability advantages. As the Powder Coating Institute (PCI) states, “Powder coatings contain no solvents and therefore emit negligible, if any, polluting VOCs into the atmosphere.”2 This includes all architectural grade powders. There is no need to worry about VOC limits or for the need for a thermal oxidizer to remove solvent/VOCs because they are simply not there in the first place.
Powder coatings can also be reclaimed and reused or recycled. Similar to liquid paints, not all the powder product makes it onto the substrate. The coating that does not make it onto the part is often referred to as “overspray.” However, unlike liquid paints, overspray can be reclaimed and mixed in with “virgin” powder and reused or recycled.
Most powder applications on aluminum only require a single coat to look great and deliver the technical performance expected from architectural performance coatings. This significantly reduces the amount of product used, alongside the amount of energy and time to apply multiple coats.
DSM, a global science-based company specializing in health and nutrition, did a study on carbon which concluded that powder coatings have a lower carbon footprint than equivalent solvent borne liquid paints.1 In addition, there are comparisons that highlight powder outperforming both liquid and anodizing paints in the testing required for Environmental Product Declarations (EPDs), including global warming potential (GWP)—which is now being used to measure embodied carbon.
There are several powder coating manufacturers with EPDs for their architectural grade performance powders—delivering third-party verification and enabling the design community to meet sustainability goals, whether they are internal objectives in practicing sustainable design, or an accreditation such as Leadership in Energy and Environmental Design (LEED) or Declare. Health Product Declarations (HPDs) may also be available for interior grade powder products.