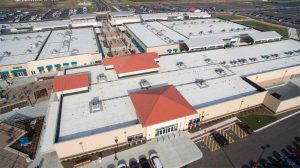
Photo courtesy St. Charles Parish & School
TPO and PVC membranes are known to resist the hydrostatic pressure resulting from standing or ‘ponding’ water.
Additionally, they are not affected by any freeze and thaw cycles. However, similar to other roof membranes, TPO and PVC weather from the effects of ultraviolet (UV) light and heat. For this reason, accelerated aging is conducted to expose TPO and PVC membranes to conditions often far in excess of what is experienced during rooftop use but in shorter (accelerated) time periods.
Thermoplastic membranes are not a ‘cure-all’
While the popularity and performance characteristics of these membranes are clear, every thermoplastic membrane exhibits strengths and weaknesses. While thermoplastic membranes represented more than 50 percent of the low-slope membrane roofing market in 2018, there are installations where their traditional use is not recommended.
All thermoplastic membranes rely on one layer of roofing material to waterproof the building. More traditional roofing options, such as built-up roofing (BUR) and modified bitumen, offer redundancy in the form of multiple layers of roof membrane protection. Some asphalt-based product specifications also offer greater puncture resistance and are more forgiving of rooftop abuse than standard thickness thermoplastic membranes.
Another installation where care should be taken is one with high heat loading combined with concentrated exposure to sunlight, although this is less of a concern in northern climates. Most roofing materials degrade over time when exposed to heat and UV and their long-term performance depends on formulation and in-situ conditions, so exposure to high temperatures and high UV, such as south- and west-facing walls in extremely hot climates, may warrant either a thicker membrane or a membrane that is formulated for such severe conditions.
As mentioned previously, thermoplastic membranes are often specified with ISO insulation. As one of North America’s most widely used, readily available, and cost-effective insulation products, ISO has been cited by the U.S. Environmental Protection Agency (EPA) for its responsible impact on the environment. However, according to some sources, the insulating performance of ISO insulation is degraded at colder temperatures. Questions about the cold-weather performance of polyiso should initially be directed to pima.org.
Regarding the environmental impact of using thermoplastic membranes, manufacturers can publish environmental product declarations (EPDs) in accordance with the International Organization for Standardization (ISO) 14025, Environmental labels and declarations – Type III environmental declarations – Principles and procedures. EPDs rely on life-cycle assessment (LCA) to provide information on a number of environmental impacts of products over their life cycle.
Thermoplastic membranes are also suitable for roofing upgrades on existing low-energy buildings, although this is highly dependent on building location, construction, and interior conditions. In colder climates, cooling load is less of a concern. In fact, building scientist John Straube does not recommend using light-colored roofing materials in colder climates, as they reduce the potential for drying of condensation that may build up within the roof assembly.
Regarding condensation, a hydrothermal analysis should be conducted using a program such as WUFI to determine the condensation potential of the specific roofing design using the expected interior and exterior conditions for the building and location.
WUFI allows realistic calculation of the transient coupled one-dimensional heat and moisture transport in multilayer building components exposed to natural weather. It is based on the newest findings regarding vapour diffusion and liquid transport in building materials and has been validated by detailed comparison with measurements obtained in the laboratory and on outdoor testing fields. In general, the building design should not show increasing levels of condensation versus time. If it does it should be revised to prevent this situation.
Conclusion
Thermoplastic membranes can meet a variety of different building requirements by offering a range of options in new construction, retrofit, and tear-off/reroofing situations. Single-ply membranes, including thermoplastics, are particularly suited to ‘big box’ applications due in part to the availability of large 3 x 30 m (10 x 100 ft) sheets using some of the labor-saving techniques mentioned earlier. Thermoplastic membranes also offer excellent resistance to UV degradation and ozone and chemical exposure.
It is also important to note these high-performance thermoplastic roofing membranes are compatible with the latest rooftop technologies, including solar arrays and vegetative roofing. Given the wide variety of installation options available, it is easy to understand why these membranes have continued to gain in use and provide long-term performance for building owners.