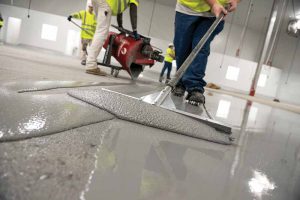
Inspecting the concrete
Before beginning a resinous floor coating project, installers should conduct a visual inspection of the concrete substrate to identify all contaminants, such as oil, grease, grime, silicone, and/or existing sealers. Misting the surface with water can help identify bond inhibitors. If the water beads up and does not wet out the concrete or change its color, it indicates something within the concrete—perhaps a contaminant oil or silicone—is creating a barrier.
While a visual inspection is important, installers should also check for surface soundness. Dragging a chain or tapping the surface with a hammer, metal pipe, or other hard object will reveal different sounds over hollow areas. Tapping the surface is a popular and accurate technique, especially if concrete is lifted or not lying flat on the substrate. Installers should also look for excessive cracking and determine if the concrete is structurally adequate to support a topping. They should also identify spalls or pop-outs and determine if they occurred due to an impact or as a result of previously bolted-down equipment being removed from the floor. If installers cannot establish what caused the damage, they should try to attain more information before proceeding.
Developing a concrete surface profile (CSP)
If concrete is deficient during initial inspections, it needs to be repaired or replaced. In rare cases, this might mean tearing out complete sections and pouring new concrete. In other cases, smaller repairs can sometimes be made using standard concrete. However, most often, repairs can be made using materials designed for concrete restoration such as acrylic cement, urethane concrete, or epoxy mortar. The type of restorative material depends on the condition of the concrete. Is it contaminated? Was there a freeze-thaw which removed the top surface? Again, installers should identify the cause for the deficient concrete before proceeding.
Although concrete is the least expensive method for repairing small areas, it extends repair timelines, as installers may have to wait over a week to apply a coating on top. For a faster repair turnaround, an epoxy or urethane concrete material will be best.
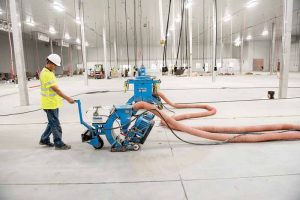
To initiate surface preparation, installers must remove any bond-inhibiting substances by degreasing, grinding off, or in severe cases, shotblasting the concrete (Figure 5), depending on the depth of the contamination. For example, they will degrease a floor using a floor machine or buffer with an aggressive brush, perhaps adding hot water and/or steam. If contamination is from silicone, mechanical grinding might be necessary, followed by a water test. If the contamination is oil-based, which is common, it can be emulsified and removed.