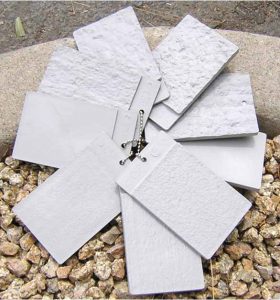
Once all concerns have been identified, it is important to develop a proper CSP in the substrate before coating it (Figure 6). A CSP increases the amount of surface area in the same square meter (square foot) of area by creating divots and peaks in the concrete’s substrate. This additional surface area provides more contact points for coating materials to bond with, providing greater adhesion and durability potential in the flooring. The CSP should be appropriate for the specified coating system. All holes, spalls, pop-outs, and other surface flaws should be pre-filled, so they do not appear through the finish coat. This step is more important for thinner coating applications.
In general, the thicker the coating system used for applications, the more daily abuse the floor can be expected to support. Such floors must be able to withstand the impact of dropped pots and pans, tools falling from above, or the pressure of forklifts transporting loads across them (Figure 7). In such cases, a greater CSP is required to give the flooring material more bonding area, thereby increasing its bonding strength.
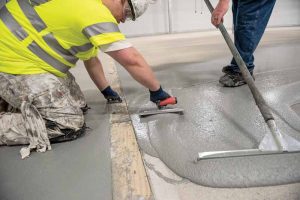
By contrast, an aircraft hangar might feature a thin-mil, chemical-resistant coating because the floor is not expected to withstand as much stress (Figure 8). A tow motor might pull an airplane across the floor, but it is all on wheels. The area may be designated for only light-duty work, so heavy impact would be unlikely, and the aviation fuel-and fluid-resistant finish would allow spills to be easily wiped up. This type of floor will not require as great a CSP for those reasons. In addition, a 10- to 30-mil coating will not hide surface imperfections and a greater CSP would show through in the finished floor. Such telegraphing of concrete surface imperfections through the final coating finish is undesirable. Therefore, the thinner the coating system, the more important it is to fill in any imperfections to ensure an aesthetically pleasing finish.
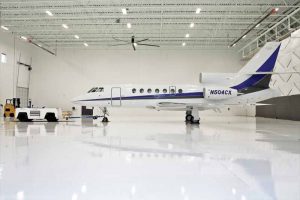
The misunderstood role of moisture
Moisture is probably the most misunderstood reason for coating failures. Too much moisture in a concrete substrate may cause the resinous flooring system to bubble and blister, weakening it and making it susceptible to disbonding. However, moisture alone is not the culprit of those failures because it does not generate enough pressure to break a well-bonded coating from a concrete substrate.
Moisture in concrete, when condensed into a liquid, will emulsify the hygroscopic elements within the concrete itself. These emulsified elements or sulfate salts are carried to the surface, and as the water dissipates, crystals form and expand, which may eventually fracture the bond between the coating and concrete. The formation of salt crystals right at the bond line are what fracture the bond, not the moisture. Once the bond is fractured, liquid continues to accumulate, and the hydraulic movement will lead to failure. The liquid contains water, salts, and a hint of uncured resinous components leached out of the coating. Such sulfate salts create bonding problems for many floor finishes beyond resinous systems, including carpet and vinyl composition tile (VCT).