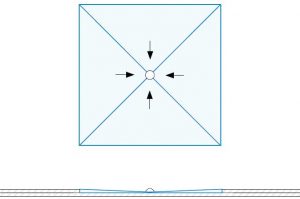
Components of tapered insulation systems
Tapered insulation systems commonly incorporate flat polyiso board stock (referred to as “fill panels” or “tapered fill panels”) to support the tapered panels. The tapered panels can be a single panel (or “one panel repeat”) system meaning the taper is provided by a single repeating panel in conjunction with fill panels (Figure 3). A four-panel (or “four panel repeat”) tapered insulation system in which the slope is developed using four repeating panels. This system utilizes 50.8 mm (2 in.) and 102 mm (4 in.) fill panels.
Non-typical designs can feature up to an eight-panel (or “eight panel repeat”) system with eight tapered panels making up the sloped section prior to incorporating the first fill panels. An example of an eight panel repeat system with a 25.4-mm (1-in.) and 50.8-mm (2-in.) fill panels and 1.59 mm (0.06 in.) per ft slope is provided below (Figure 4).
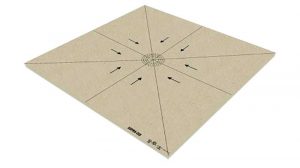
Flexibility in configurations, slopes, and fill panel thicknesses in polyiso tapered insulation systems demonstrate its versatility to accommodate a range of roof designs and rooftop complexities.
Crickets are an integral part of a tapered insulation system and are commonly find use in two-way systems. Crickets can divert water toward drains and away from curbs, perimeter walls, and roof valleys. The two factors that must be considered in the design and installation of crickets are slope and configuration. The general rule of thumb is that for a full diamond cricket, the total width should be between one third or one half of the total length (Figure 5). The wider the design of the cricket the more slope is utilized in the field of the roof. This improves drainage efficiency. With limitations, narrower crickets can be used within greater fields of slope.
Crickets typically have diamond or half-diamond shapes (Figure 6). However, kite-shaped and snub nose crickets can also be configured to accommodate specific roof designs. To keep water from remaining on the cricket surface, the design needs to have sufficient slope (generally twice the slope of the adjacent field of the roof). NRCA provides guidance regarding cricket geometry.
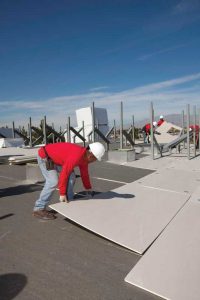
More often than not, the drains will not be located at the lowest structural points due to physical limitations (e.g. beams and columns). A properly sloped roof should have sumps at the drains to increase drainage efficiency. Sumps can be used with both structural slope roofs and with fully tapered systems to promote positive slope to the most critical locations on a roof. This helps ensure the drains are the actual low points of the roof (Figure 7).
Designing for long-term performance
Tapered systems can add first costs to a project and may come under scrutiny during a value engineering analysis. However, eliminating a tapered system can compromise the drainage intent of the design professional, architect or roof consultant and even changing the specified slope or redesigning the configuration of the tapered panels can have unintended consequences. In scenarios where tapered insulation systems are eliminated or significantly altered, the building owner risks trading savings on the installation for increased long-term costs resulting from poor roof drainage, including additional roof maintenance and even premature roof system failure.
Conclusion
Whether for new construction or a replacement on an existing building, installing a low-slope roof is a project that requires careful planning and design to ensure that the new system will meet the rigorous demands during its service life. Employing tapered insulation is a cost-effective way to increase a roof’s thermal efficiency while also implementing an adequate rainwater management strategy that includes both proper drainage and elimination of ponding water. A tapered roof system can reduce costs in terms of energy usage, roof maintenance, and forms a critical element for long-term performance and durability of the overall roof system.
Author
Marcin Pazera, PhD, is the technical director for Polyisocyanurate Insulation Manufacturers Association (PIMA). Dr. Pazera coordinates all technical-related activities at PIMA and serves as the primary technical liaison to organizations involved in the development of building standards. Dr. Pazera holds a doctoral degree in mechanical engineering from Syracuse University and, over the course of his career, has worked in building science with a focus on evaluating energy and moisture performance of building materials and building enclosure systems. He has expertise in building enclosure and product manufacturing encompassed-research, testing, product conception and development, and computer modeling/analysis.