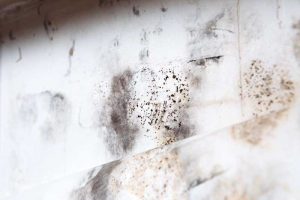
The basic challenge for insulation installation is to meet the required or desired R-value. However, this simple challenge is complicated by the presence of moisture. It makes a big difference where the insulation is installed on the basement wall.
During the cold season, insulation on the interior side of the basement wall will be colder on the side facing the exterior of the building, and the interior side of the insulation will be facing the warmer moist air of the basement’s interior. This is a perfect recipe for moisture condensation on the interior side of the basement wall, and moisture condensation within the insulation. Moisture condensation typically leads to mold and mildew (Figure 6).
Conversely, insulation on the exterior side will be exposed to exterior moisture, as well as the compressive forces of soil around the building. It may also be exposed to ultraviolet (UV) radiation if the insulation is left exposed above grade.
The advantage of locating insulation on the exterior side of basement walls usually outweighs any advantage of locating insulation on the interior side for thermal control. The basement wall will stay much warmer during the winter when the insulation is on the exterior side. Since the basement wall is warmer, moisture condensation is far less likely within the basement, and mold and mildew can be prevented from forming—provided the interior relative humidity (RH) is controlled.
Getting practical
If the goal is to (1) facilitate drainage, (2) keep temperature extremes outside, and (3) prevent condensation, then what practical measures must be implemented during basement design?
Start with the polystyrene foam insulation thickness. Table 1 includes R-values for polystyrene foam insulations, including XPS and EPS foam insulations. Based on recognized R-values for these, special considerations for insulation thickness adjustments for habitable basement designs are as indicated in Table 2.
In general, the thickness of EPS insulation should be increased by 24 percent to achieve the desired thermal performance and to prevent condensation when EPS is placed outside below grade walls. Further, EPS thickness must be increased by 50 percent in below grade horizontal applications (i.e. under the floor slab). Remarkably, the thickness of XPS insulation needs to be increased by only 11 percent to achieve a desired thermal performance and to prevent condensation when XPS is outside below grade walls. XPS thickness needs to be increased by only 25 percent in below grade horizontal applications.
More specifically, the following design examples apply to insulation beneath a basement floor slab that requires an insulation design R-value of R10, and on the exterior side of a basement wall which requires an insulation design R-value of R20.