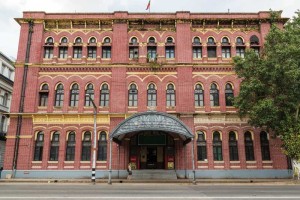
by Andre Desjarlais, Amy Wylie, and Mugdha Mokashi
Sixty percent of U.S. commercial buildings were constructed before 1980. (This comes from Energy Information Administration’s (EIA’s) “2012 Commercial Buildings Energy Consumption Survey,” which can be accessed at www.eia.gov/consumption/commercial/reports/2012/buildstock). Retrofitting them for energy efficiency is essential to achieve the Department of Energy (DOE) Building Technologies Office’s (BTO) goal of halving building energy use by 2030. (For more, see DOE’s Office of Energy Efficiency and Renewable Energy (EERE) 2014 paper, “Windows and Building Envelope Research and Development: Roadmap for Emerging Technologies”). Most existing buildings have masonry construction with uninsulated wall assemblies, which offer good potential for wall improvement strategies. Effective analysis of these retrofits is essential to ensure improved durability when insulating masonry walls on the interior. Now, best practice retrofit recommendations have been evaluated based on the results of hygrothermal analysis, laboratory tests, and field performance evaluations.
Standard component retrofits, such as HVAC or lighting upgrades, present a limited scope for retrofit. They prevent the building from realizing greater energy savings that can be achievable when considering an envelope retrofit along with a standard component retrofit. (See the American Institute of Architects (AIA) and Rocky Mountain Institute’s 2013 publication, “Deep Energy Retrofits: An Emerging Opportunity.” Visit www.aia.org/practicing/AIAB09924).This integrated retrofit approach is essential in order to achieve more than 50 percent reduction in energy consumption.
Older masonry buildings often require a retrofit on the interior due to factors such as historic preservation, zoning issues, space restrictions, or aesthetics. However, without effective analysis, adding insulation to the interior of a masonry wall can result in potential performance and durability issues such as condensation, particularly in cold climates. (See John Straube et al’s 2012 paper for Building Science Corporation, “Measure Guideline: Internal Insulation of Masonry Walls”). This is a concern because most of the pre-1980s buildings with masonry construction are located in the Northeast. (For more informaton, see K. Otto’s “CoStar Statistics on GPIC Mid-sized Class A Office Buildings” [Robust Systems and Strategy LLC, 2011] and E. Fratto’s “Identification of Unreinforced Masonry Buildings (URMs) in the United States” [Northeast States Emergency Consortium, 2012]).
The objective of this project was to identify best practices for energy-efficient and cost-effective retrofits for commercial buildings with masonry construction. The metrics used to evaluate the best practice recommendations were intended to exceed performance of American Society of Heating, Refrigeration, and Air-conditioning Engineers (ASHRAE) 90.1-2010, Energy Standard for Buildings Except Low-rise Residential Buildings, and achieve a payback in less than 15 years. The target market for the project was ASHRAE Climate Zones 4 and 5, representing a majority of the northeastern United States. While the field data collection for the project is currently ongoing, this article explains the process of evaluation for the recommended retrofit scenarios.
Market engagement for the project
The Consortium for Building Energy Innovation (CBEI), headquartered in Philadelphia’s Navy Yard, is a group of 14 member organizations funded through the DOE and led by Pennsylvania State University. It works to develop and deploy market-tested pathways to achieve 50 percent reduction in overall building energy use by 2030 for existing small and medium-sized commercial buildings (SMSCB). The research project profiled in this article supports the CBEI goal by providing envelope solutions for an integrated retrofit strategy.
The project team included collaborators representing diverse areas of the retrofit value chain. A manufacturer of raw materials for building insulation led the project, while Oak Ridge National Laboratory (ORNL) provided third-party verification for simulation and laboratory test evaluations. The Air Barrier Association of America (ABAA) and another manufacturer served as market partners, offering industry expertise for the project and guiding the commercialization of the project results.
A Technical Advisory Group (TAG) of industry experts in the area of building envelope was also engaged for this project. Their role was to provide technical advice, ensure the project outcomes were relevant to the market, and confirm set deliverables were met. The TAG members for this project were Fiona Aldous from Wiss, Janney, and Elstner (WJE) Associates, Brian Stroik from a sealant/waterproofing company, and Pat Conway from the International Masonry Institute (IMI).
In 2012, CBEI identified a potential demonstration project in the Navy Yard to show energy savings using integrated retrofit strategies. The identified building was a two-story masonry building built in the early 1940s, which required a retrofit on the interior of the masonry wall. Numerous integrated retrofit solutions were analyzed to identify an optimal solution providing energy and cost benefits. This analysis of an integrated retrofit required a longer time than a conventional retrofit analysis, which typically considers only the most cost-effective single-component retrofit. Although the building owner appreciated this analysis, a change in the business strategy resulted in the owner not pursuing the proposed retrofit.
Nevertheless, the analysis and interactions with the building owner were instrumental in identifying market barriers for envelope retrofits such as initial upfront costs and lack of information regarding options and benefits. This not only requires extensive evaluation at the initial stage to identify solutions and ascertain potential savings, but also indicates a need for making more information available on interior insulated masonry buildings through validated case studies. Those case studies could then reduce the need for extensive evaluations and help accelerate adoption of wall retrofits in the market.
It is great to know that you can restore these amazing buildings. Some areas just look great with restored buildings and others look great with industrial buildings. Thanks for sharing!