by James Hodgson
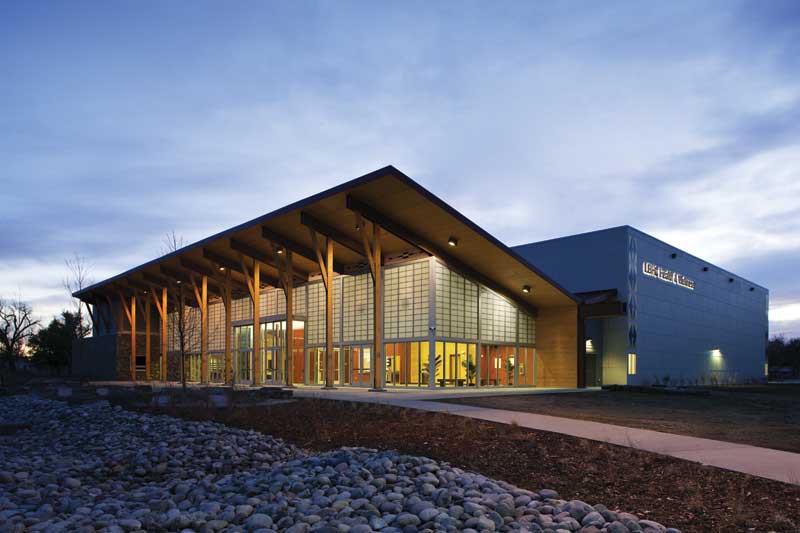
What does it take for gymnasiums or buildings with wide-open interior spaces to achieve a platinum certification under the Leadership in Energy and Environmental Design (LEED) rating program? With a floor area of 700 m2 (7500 sf) and a ceiling height of 7.3 m (24 ft), a typical high school or junior college gym has a vast interior space to heat or cool—approximately 5100 m3 (180,000 cf) of volume—so an ultra-energy-efficient envelope is crucial.1
For gyms and other buildings with large interior volumes, such as worship facilities, community centers, barns, cold storage, and light manufacturing, building teams increasingly are specifying structural insulated panels (SIPs) in conjunction with steel frames.
SIPs are engineered wall and roof systems combining structure, insulation, and air barrier in one unit. The panels are made of a rigid insulating foam core to which structural wood panels have been laminated. Architects and contractors have employed SIPs for decades in a wide range of commercial and institutional buildings, as well as for multi-unit residential structures and single-family homes, in all climate zones.
In what situations does it most make sense to integrate SIPs with metal-framed buildings? What design factors do project teams need to be aware of? And, what pitfalls must be avoided?
SIPs can help the design team achieve high-performance building envelopes in structures with wide-open interior spaces. They have many benefits, including:
- providing continuous insulation (ci);
- reducing gaps to be sealed against air leaks;
- decreasing thermal bridges;
- offering advanced framing methods; and
- saving time and labor on the jobsite.
The following two project examples serve as a starting point to frame the discussion of integrating SIPs with steel structural frames at the design stage.
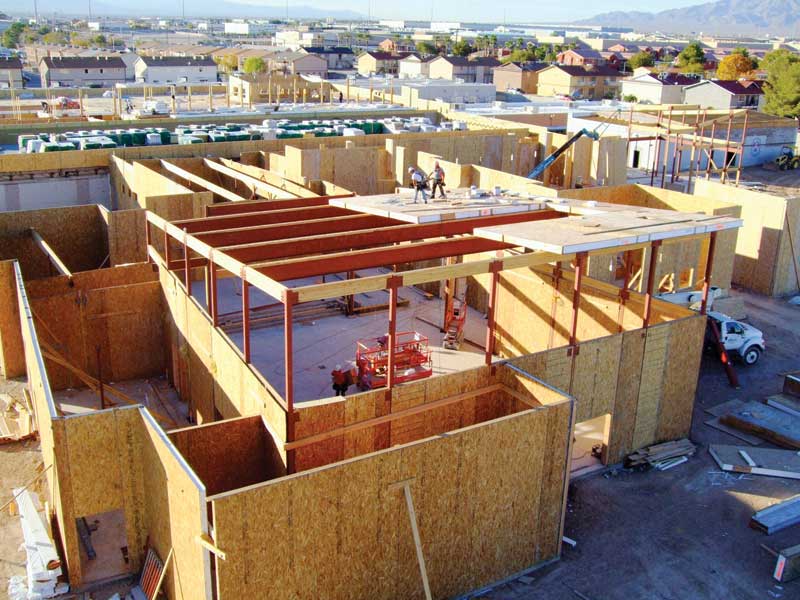
Photo courtesy Premier SIPs
Finn Hill Junior High
The Lake Washington School District in suburban Seattle built its Finn Hill Junior High to be 47 percent more energy efficient than targets set under the U.S. Department of Energy’s (DOE’s) Energy Star program.
The 10,757-m2 (115,900-sf) building was designed to serve 600 middle school students, and an additional 150 students in an “environmental adventure school” located within the building. In collaboration with the design team, Mahlum Architects designed the school to an energy consumption target of 283,913 kJ/m2/year (25 kBTU/sf/year), compared to an Energy Star Target Finder average energy use of 537,164 kJ/m2/year (47.3 kBTU/sf/year), a 47 percent improvement. By comparison, older schools within the Seattle area consume upwards of 999,374 kJ/m2/year (88 kBTU/sf/year), making the Finn Hill Junior High approximately 70 percent more energy efficient than older buildings.
To meet these aggressive energy targets and enable the school to be “net zero-energy ready” (i.e. having the potential for roof-mounted solar panels to meet all the school’s energy needs) the design team specified 152-mm (6-in.) thick SIP walls and 254-mm (10-in.) thick SIP roof panels over a steel structural frame. The SIPs provided high R-values (R-25 at 4 C [40 F] for the walls and R-40 for the roof) and reduced air leakage compared to other envelope solutions.
“Every aspect of the design and construction must be considered in an integrated way when energy conservation goals are so ambitious,” said Anjali Grant, AIA, LEED AP, project architect with Mahlum.
“Utilizing SIP panels not only supported the strategies for energy savings, but also allowed for a smooth and rapid assembly process, shaving weeks off a tight construction schedule,” added Mitch Kent, AIA, project manager with Mahlum.
Little Big Horn College Health & Wellness Center
The Little Big Horn College Health & Wellness Center (Crow Agency, Montana) includes:
- a National Collegiate Athletic Association (NCAA) gymnasium seating approximately 1300 people;
- spaces for aerobics/community gathering, weightlifting, and cardiovascular fitness;
- locker rooms; and
- support facilities.
The college (of the Apsàalooke Nation – Crow Tribe of Montana) built the facility to serve its students as well as the surrounding community.
The college wanted a sustainable, energy-efficient building targeted to LEED Platinum standards, to reinforce the center’s role in supporting healthy living and to respect the tribe’s historic, cultural, and artistic way of life.
Operating under an integrated project delivery (IPD) approach, the project team specified SIPs for the exterior walls and roof.
“SIPs meet a number of needs with just one system,” said Doug Morley, principal architect with Springer Group Architects. “They install fast, insulate well, and are strong. Other than in the large gymnasium, this reduced the need for a secondary support structure in the building and saved a bunch of time and money.”
The SIPs played a key role in the building’s high energy efficiency design. The large-sized panels have fewer gaps requiring sealing than other construction methods and provide ci throughout the walls and roof.
“Energy savings is a big part of getting to the LEED Platinum goal,” said Ben Mitchell, project manager with Fisher Construction, the project’s general contractor (GC).
Using SIPs with metal structural frames
The 1300-seat gymnasium portion of the Little Big Horn College Health & Wellness Center illustrates how buildings with large, open interior spaces requiring an energy-efficient envelope are suited for SIPs and metal structural frames.
Two of the players involved in this project summarize the role SIPs have in such spaces.
“They work well in long spans and have high shear and diaphragm values. This was especially crucial to help create the wide-open space in the project’s gymnasium,” said Matt Anderson, owner of Compass Consulting Engineers.
“It is hard to get a gym to meet any energy code, let alone LEED Platinum, but the SIPs provide a super energy-efficient envelope, much better than we could get from other products for the same labor and material costs,” added Ben Mitchell, the project manager at Fisher Construction.
SIP advantages |
Projects teams for many types of commercial and institutional buildings specify SIPs. Below are several considerations for SIPs.
Energy efficiency Testing by the U.S. Department of Energy’s Oak Ridge National Laboratory (ORNL) showed SIP structures are up to 15 times more airtight than stick-framed walls insulated with fiberglass batts. A SIP structure had an air leakage rate of only 0.2 m3/min (8 cf/min) at 50 pascals of pressure compared to stick framing, which leaked air at 3.4 m3/min (121 cf/min). This dramatic difference is a result of SIP-built walls and roofs having far fewer gaps to be sealed, as the spaces were otherwise comparable, including interior gypsum board with taped joints. The lab also found for similar wall thicknesses, SIPs were 47 percent better at resisting heat flow than stick framing.* Streamlined construction “With the prebuilt panels, you just have to piece the building together like a puzzle,” said contractor Glen Kamerman, partner with Kamerman Construction. “Compared to stick framing, SIP walls go up much faster since they can be installed in large sections and eliminate the need for separate onsite framing and insulation work,” said Sharon Bullock, project manager for Community Development Programs Center of Nevada (CDPCN). “The finished walls are also beautifully straight, which saves time on drywall installation, painting, and other finishing work.” As an example of the potential time savings, the building team for the 900-student Jacob E. Manch Elementary School in Las Vegas, Nevada, completed the building’s framing in only seven weeks using SIPs. The school district had originally allotted 17 weeks for the structural work using concrete masonry units (CMUs), so the SIPs resulted in a 60 percent time savings. Gary Radzat, former president of Shell Building Systems, noted: “Not only did the SIPs install faster, saving on structural building time, but [they] also reduced labor time for the electrical work. The panels have electrical chases built inside them so electricians do not have to drill or modify faming. Instead, they can easily pull wires through the chases. Labor savings
* Read “Heating and Blower Door Tests of the Rooms for the SIPA/Reiker Project” here. |
Design factors
When using SIPs in steel-framed buildings, it is important to take into account a number of factors, such as:
- shear and transverse loads;
- wall height;
- available staging area;
- SIP attachment method
- air and moisture management; and
- fire performance.
Shear and transverse loads
Although designers often use SIPs as the primary structural elements in light commercial and institutional buildings, in steel-framed structures, the SIPs usually are a supplemental element. In a steel-framed building, SIPs can take on additional shear loads, similar to the way sheathing helps enhance shear load capacity in stud walls. SIPs also can take on additional transverse loads for a stronger overall structure. As the specifics of these loading details depend on the building, one can contact the manufacturer for design assistance.
Wall height
SIPs come in large panel sizes, up to 2.4 x 7.3 m (8 x 24 ft), which helps reduce the number of gaps in a wall to be sealed, and can speed up wall construction. In light of these size limits, the maximum unsupported wall height for a SIP attached to a steel-framed building is 7.3 m (24 ft). Walls taller than that require an intermediary structural support for a second SIP panel placed above a lower panel.
Available staging area
Since SIPs are large, heavy, monolithic units, and require equipment to move and place them, it is important for project teams to take into account adequate staging areas for trucks, unloading equipment, and, potentially, for panel storage and staging, depending on the job’s size. This is especially an issue in dense urban areas and on projects with zero lot lines.
SIP attachment method
SIPs typically are attached to steel structural frames in one of two ways:
- directly to the steel using steel fasteners; or
- by screwing the SIPs to wood nailers attached to the steel.
The SIP manufacturer can assist with attachment details for their specific panels, and in accordance with the project’s loading and other design concerns.
Air and moisture management
To maximize energy savings, occupant comfort, and building longevity, it is essential to manage air flow and moisture in SIP structures. This includes appropriately sized mechanical ventilation, sealing all joints with SIP tape or mastics, and a building design incorporating methods to control water vapor transmission and bulk water infiltration.2
Fire performance
Although SIPs are made of combustible materials—oriented strand board (OSB) and expanded polystyrene (EPS) insulation—many manufacturers have tested their SIPs in fire-rated wall and roof assemblies.
It is important to confirm with the SIP manufacturer which fire tests their panels have passed in wall and roof assemblies, such as the one-hour, fire-resistance requirements of ASTM E119, Standard Test Methods for Fire Tests of Building Construction and Materials. Meeting the one-hour fire test typically requires attaching two layers of gypsum (depending on the thickness of the gypsum) to the SIP. The gypsum protects the EPS foam core from melting in the heat of a fire, for the duration of the fire-rating period.
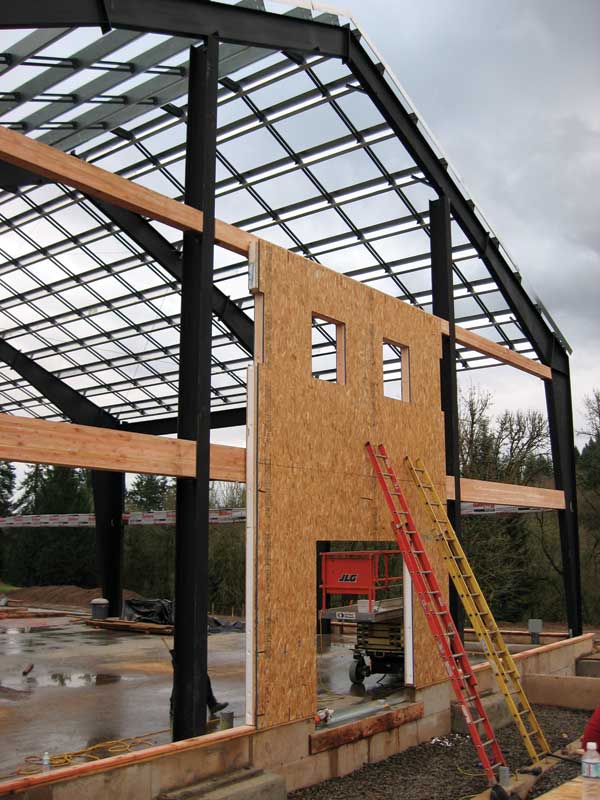
Photo courtesy Premier SIPs
Cost factors
The installed costs of SIPs are comparable to other framing methods, and in many cases, may be lower due to reduced construction times and jobsite waste. SIPs can also decrease costs for other building systems, as their insulating properties and the reduced air leakage through the exterior building envelope allow designers to specify smaller-capacity heating and cooling equipment. These cost savings are especially notable for a building’s HVAC system, potentially reducing requirements by up to 40 percent. Over the long-term, SIPs dramatically reduce energy consumption and related costs.
For some complex building designs, the cost of structural elements may be somewhat higher with SIPs than other methods because of additional engineering and production requirements for the panels. Details can be confirmed with the SIP manufacturer.
Conclusion
From energy efficiency to faster construction, SIPs offer many benefits, but they are no panacea. Although any light commercial/institutional building or single-family residence can be adapted to use SIPs, when designing a steel structure, it is important to consider SIPs early in the design process. By bringing in the SIP manufacturer early, project teams can help ensure the SIPs and steel frame are optimized for one another. This helps avoid problems like having steel structure elements placed such that the SIP panels must be excessively trimmed in the factory, which wastes material and drives costs higher than they would be with a well-planned, integrated design.
As the project team for the Little Big Horn College Health and Wellness Center discovered, SIPs can provide the ultra-energy efficient building envelope needed to help gyms and other large open spaces meet LEED rating standards.
James Hodgson is the general manager for Premier Building Systems, a manufacturer of structural insulated panels (SIPs). Hodgson also serves on the board of directors of the Structural Insulated Panel Association (SIPA). Hodgson can be reached via e-mail at james.hodgson@premiersips.com.