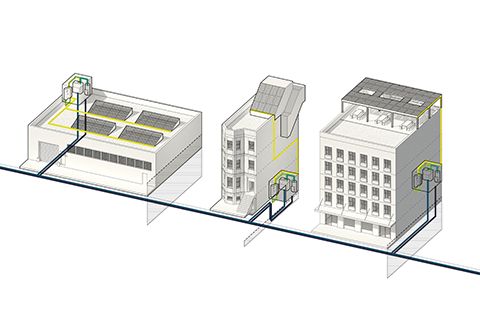
Superior windows
Window selection is critical in any building envelope, but Passive House brings a higher factor of importance due to their typically lower relative energy performance and their often large overall surface area. Passive House-certified windows have been developed over the past decade to help eliminate this envelope Achilles’ heel.
The Passive House recommended standard is </ 0.8 W/m2/K (</ 0.14 Btu/hr-sf-F) equivalent to an R-7. To achieve this performance, windows are constructed with nonconductive frame materials such as wood or fiberglass and with triple-pane, gas-filled lites. The U.S. marketplace is limited in such offerings (though a recent check shows a few domestic companies with offerings), but items like Passive House windows may be specified through European manufacturers.
The Passive House window standard is not a requirement, and if lower R-values are specified the energy efficiency levels must be compensated for in the envelope insulation. The typical U.S. window meeting building code varies per climate from less than 1 R-value (U-value of 1.2) in Climate Zone 1 to 2.8 R-value (U-value of 0.35) in Climate Zone 8, according to the 2009 version of the International Energy Conservation Code (IECC). Passive House standards range from 2.5 to 7.0 times more stringent.
Insulation
Deep insulated wall assemblies make up the core of the envelope. For Passive House, most buildings require envelope performance levels in the range of R-40 to R-60 for walls, R-50 to R-90 for roof systems, and typically about R-30 to R-50 for sub-slab assemblies. Such insulation levels may be about four times the levels required by local building code, and may yield a much deeper, thicker wall design. Rather than using stud-wall cavity-based insulation systems, alternatives such as insulated concrete forms (ICFs), exterior insulation and finish systems (EIFS), and various other continuous insulation (CI) wall details allow for a thinner wall section while achieving necessarily high insulation values.
Airtight construction
The standard’s airtightness requirements are among the most challenging requirements for U.S. design teams trying to achieve Passive House criteria. Success relies heavily on the general contractor’s expertise and attention to detail, ensuring all openings and penetrations large and small are flashed and sealed before the envelope’s closing. There are several effective materials in the marketplace for these details, including a variety of window tapes, caulks for joints and seams, and airtight electrical outlet boxes. This process visually differentiates Passive House projects during the construction phase, when observers can see the wrapping and taping of substrates, windows, and penetrations.
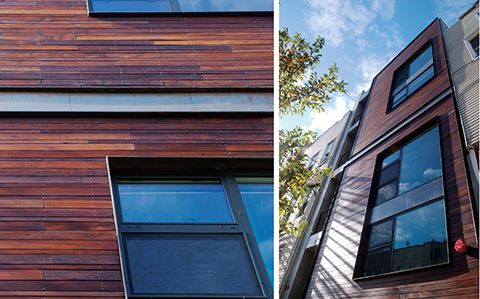
The airtightness measure of 0.6 ACH50 required for achieving certification is verified onsite by means of a blower door test. (PHI has created an energy retrofit standard, EnerPHit, which requires a more achievable 1.0 ACH50 for certification.) For Passive House, a European standard—EN 13829, Thermal Performance of Buildings: Determination of Air Permeability of Buildings−Fan Pressurization Method—is often referenced. While it is similar to ASTM E779, Standard Test Method for Determining Air Leakage Rate by Fan Pressurization, there are slight differences in the timing of the tests, how volume is calculated, and methods for final reporting. Conducting a blower door test early in the construction phase helps indicate any remedial steps needed, envelope areas requiring added air sealing, and what should be next in the path to Passive House certification. A final test is conducted when the envelope and mechanical systems are completed.
Ventilation
‘Passive’ House is perhaps a misnomer—ventilation in this case is not a passive design feature (see “At a Standard’s Core, Passive Design Precepts,” below), but instead requires an active mechanical system to move stale indoor air out. No longer is incidental infiltration an acceptable alternative for ensuring the fresh outdoor air supply. Careful design of the ventilation system by the engineering team is important to ensure fresh air is introduced in all occupied rooms. Typical ventilation systems specified are energy recovery ventilation (ERV) or heat recovery ventilation (HRV) units; depending on the size of the building and the spatial configuration, a project may require multiple units.
HRV systems allow heat from the warmer air stream—stale air in winter, fresh air in summer—to be transferred to the cooler air stream. In the winter season, the HRV ‘recovers’ a portion of the heat that would have otherwise been exhausted and lost to the exterior. This heat transfer occurs without any mixing of the two air streams.
An ERV does everything an HRV does and allows some of the moisture in the more humid air stream—usually the stale air in winter and the fresh air in summer—to be transferred to the drier air stream. Ventilation is typically exhausted from bathrooms and kitchens, whereas it is supplied to the living room and bedrooms. These ventilation systems should run at about 90 percent efficiency, and help heat and cool the building in the shoulder months. This eliminates the need for other individual ventilation systems and, in this way, minimizes any additional penetrations through the envelope that could cause heat loss. If ducts are associated with the ventilation installation, the runs should be minimized, kept as straight as possible, and built without flexible ductwork, which can kink.
The Passive House seems like a great step towards greener, more environmentally friendly living. I can’t wait to see some advancement on this! Thanks for sharing this.