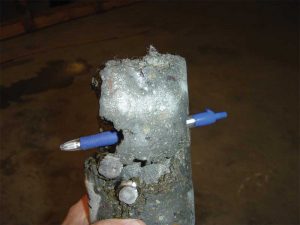
Consolidation of shotcrete is achieved by placing it at a high velocity. Until one has personally seen concrete shot out of a hose at 129 km/h (80 mph), one cannot fathom the forces involved. These forces can compromise the laps of waterproofing membranes.
Shotcrete overspray on the waterproofing membrane above a working lift can form a thin layer of cured concrete that does not bond well with the shotcrete in the subsequent working lift. In this condition, the membrane may only bond with the overspray.
Quality assurance of shotcrete
Anyone who has worked with shotcrete has heard of mixtures being shot “too stiff,” or sloughing because it was shot “too wet.” The quality of structural shotcrete is dependent on the properties and consistency of the mix, the workmanship of the crew applying the material, and a sound substrate with appropriate access for its placement.
Proper mixing of shotcrete materials is important when it comes to reinforcement encapsulation. Poorly mixed shotcrete can develop sand lenses, rebound pockets, and other defects, thereby creating pathways for water to flow within the shotcrete.
A primary key to a successful shotcrete project is a knowledgeable contractor with an experienced shotcrete crew, not just an expert nozzleman. The basic shotcrete crew may consist of a foreman, nozzleman, assist nozzleman, finisher or rodman, wireman, pump and mixer operator, and laborers. Though the nozzleman has the greatest influence on the shotcrete placement, the quality of shotcrete application depends on the entire crew.In 2000, ACI, in cooperation with the American Shotcrete Association (ASA), established a formal training program for certifying shotcrete nozzlemen. However, certification does not mean the nozzler is qualified for every project. He or she may not have sufficient experience with heavily reinforced areas or complex structural geometry. Therefore, preconstruction mockup testing should be specified and conducted.
It is recommended to include in the specification a statement that only ACI-certified shotcrete nozzlers will be allowed to apply shotcrete on the job, and that the trained nozzlemen will need to qualify in accordance with the site-specific mockup testing. Also, for large projects, it is advisable to have more than one qualified nozzler.
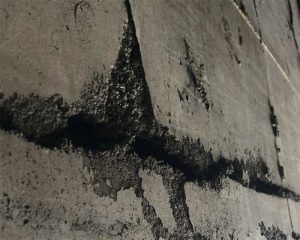
Independent field inspection should document any nonconformance of shotcrete placement and notify the contractor and engineer. A follow-up inspection should be conducted to confirm the corrective action properly resolved the nonconformance.
If water leaks are reported, injection materials are employed to fill voids and cracks within the shotcrete. With the numerous amounts of voids that can be typical with shotcrete, it can be difficult to precisely locate the initial point of water penetration. In the event of a warranty claim, manufacturers will often core the foundation walls to verify the shotcrete is well consolidated. Voids can nullify the waterproofing warranty.
Mockup
Following ACI 506, Guide to Shotcrete, preconstruction testing by means of a full-scale mockup is strongly recommended. The mockup should reflect the project-specific wall substrate, waterproofing and reinforcement conditions, and mimic the onsite logistical conditions. It is not unusual to have several mockup trials to optimize the system and prove the design works. Additionally, the mockup allows the nozzler to train and qualify under project-specific conditions.
Further, proper shooting procedures and application sequence should be laid out in writing in the work plan and tested at the preconstruction mockup stage.
One blind-side wall element that is good to have in the mockup is a box out of a tie-back because it is notorious for water ingress. A separate mockup may be required to facilitate this detail, as this element is large.
Since the mockup is not part of the work and the backside can be accessible, it is recommended to inspect the back of the shotcrete mockup panel for rebound or overspray entrapment or other visible imperfections not necessarily found by reviewing the cores.
In addition to the routine material quality tests, such as compressive strength required by project specification, visual examination of shotcrete cores is an important tool for quality evaluation. This type of examination can reveal imperfections, including voids, sand lenses, and delaminations, and the degree of reinforcing steel encapsulation.
ACI also publishes 506.2-13 (18), Specification for Shotcrete. However, in the opinion of the authors, one important quality assurance item no longer included in the ACI specification is the shotcrete core grades, as published in ACI 506.2-95.
In ACI 506.2-95, there were five specific shotcrete core grades. Grade 1 was defined as a solid specimen with no laminations, sandy areas, or voids behind the reinforcement steel. A Grade 2 specimen had no more than two laminations or sandy areas with dimensions exceeding 3 x 25 mm (1/8 x 1 in.). The height, width, and depth of voids shall not exceed 9 mm (3/8 in.). Porous areas behind reinforcing steel will not be more than 13 mm (1/2 in.) in any direction except along the length of the reinforcing steel. A Grade 3 specimen shall have no more than two laminations or sandy areas with dimensions exceeding 8 x 32 mm (3/16 x 1 1/4 in.) long, or one major void, sand pocket, or lamination containing loosely bonded sand not exceeding 16 x 32 mm (5/8 x 1 1/4 in.) in width. Core grades 4 and 5 have numerous large voids and sandy areas greater than that of Grade 3. It was generally practiced for applications, especially in hydrostatic ground water conditions, that a mean core grade of 2.5 or less was suitable. No single core is allowed to score greater than three, and passing requires an average score of 2.5, unless otherwise specified.