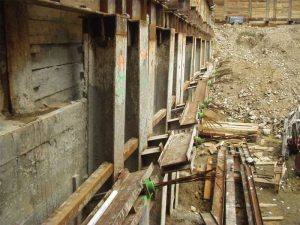
The project should not start the work until the contractor has proven its means and methods can provide the specified quality of shotcrete.
Three major issues
There are three primary installation issues with shotcrete that can have a negative impact on the performance of the waterproofing system. They are:
- voids around reinforcement;
- shotcrete overspray; and
- porous rebound pockets.
Stabilizing the reinforcement to prevent voids
Stabilizing the steel reinforcement in the wall with anchors is critical to keep it from moving or vibrating during the application of shotcrete. Vibrations in the reinforcing steel can create voids around the rebar, which reduces in-place strengths.
Sufficient anchors must be provided to rigidly hold reinforcement in place. Anchors or spacers should be located to offer sufficient clearance around the reinforcement, permit proper cover, and complete encasement with sound shotcrete. The intersecting reinforcing bars should be tied rigidly to one another and to the anchors to prevent vibration during shotcrete placement.
ACI 506.2-13 (18) only says, “Secure reinforcement to prevent movement.” This vague guidance has resulted in contractors initially installing a limited quantity of anchors only to have to add more during the shotcrete application. Of primary concern with this work sequence is the waterproofing contractor is unable to properly detail the new anchor points, which could be the source of future water leaks.
Some or all of the rebar attachment rods and fasteners may vibrate during the installation of rebar and subsequent shotcreting. With this in mind, all rebar attachment hardware should be detailed in accordance with the waterproofing manufacturer’s installation guidelines prior to shotcreting.
Although sufficient impact velocity ensures shotcrete flows around reinforcement, the rebar density of columns and pilasters create a potential for poor consolidation and the creation of voids in the structural wall, thus increasing the risk of water ingress. Due to these issues, designers may want to consider specifying CIP formed concrete for heavily reinforced columns and pilasters. They would be blocked out and cast-in-place before shotcreting the wall sections.
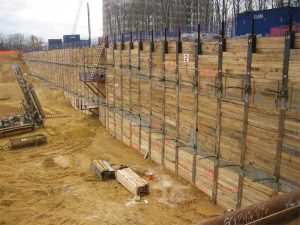
Insufficient shotcrete impact velocity assists with buildup of mix material on the reinforcement steel, resulting in a larger shadow void or porous area cast behind the rebar.
Poor reinforcement encapsulation reduces the quality of the shotcrete and increases the likelihood of water ingress.
Overspray and porous rebound
ACI defines overspray as “waste shotcrete material deposited away from intended receiving surface” and rebound as “shotcrete material that ricochets off the receiving surface,” both of which are, for all practical purposes, considered defects. When the nozzle is directed at an angle to the receiving surface, the shotcrete material can separate, creating additional rebounding and overspraying. When the nozzle is held at too great an angle to perpendicular, the shotcrete can trap greater amounts of rebound, overspray, and have poor surface bond.
With regards to waterproofing, overspray can have negative performance consequences. For example, when constructing a working lift, the exposed waterproofing membrane directly above the planned lift height generally gets covered with a thin layer of overspray. As mentioned earlier, this thin overspray bonds to the membrane and forms its initial set with the working lift. Then during the application of the next working lift the subsequent shotcrete covers the overspray (it is important to note the second-lift shotcrete does not always bond to the initial layerof overspray). Thus, just above the lift joint, the waterproofing membrane may only be bonded to the overspray and not the shotcrete wall.
This overspray issue is not supposed to happen, but it does on many projects because protection from shotcrete overspray is rarely implemented in the field.
Temporary protection from shotcrete overspray and rebound should be installed directly above and around the shotcrete lift joint. This overspray protection can be plastic sheeting, cardboard, plywood, or other appropriate means to minimize the shotcrete splatter from attaching to exposed waterproofing. If temporary protection is infeasible, overspray should be removed before it hardens.
Also, when the shotcrete mixture is applied to a surface, the aggregate tends to ricochet off the receiving surface until sufficient cementitious paste builds up to absorb it. A nozzler’s helper should remove rebound that does not fall clear of the work, especially anything entrapped behind rebar, by using a blowpipe. Unremoved rebound can be porous, and yet another pathway for water migration.
Support excavation preparation
Before the application of the waterproofing membrane and shotcrete, the support of excavation (SOE) shoring wall should be properly constructed in planar condition. Installation of shotcrete on waterproofing membranes installed on shoring walls presents placement and consolidation challenges. Additionally, if the project was valued engineered from CIP to shotcrete, and the shoring retention wall was built with the understanding CIP would be used, there can be even more challenges to shotcrete placement.
With soldier pile and timber lagging SOE, it is critical the latter is positioned on the inward-most H-pile flange to provide the most planar substrate surface possible. Placement of the timber lagging on the outward H-pile flange or mid-depth between the two H-pile flanges should be avoided because it is nearly impossible to properly place and also consolidate shotcrete behind the metal flange of the H-pile.