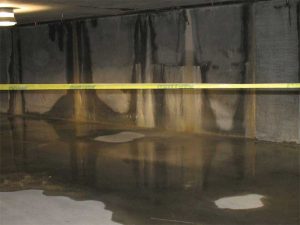
Timber lagging shoring walls should not have wide gaps between members. Wide gaps create a spot for the high-velocity shotcrete to blow open the overlap seam (even taped ones) of a waterproofing membrane. If the timber lagging is installed with wide gaps, the shoring wall can be brought to a sound and planar condition by applying a thin, fiber-reinforced layer of smoothing shotcrete, or by installing a course of cementitious boards over the face of the lagging. It is best to avoid using low compressive strength expanded polystyrene (EPS) foam insulation or any other soft material to prepare the substrate surface because it can compress or vibrate during shotcrete application.
Contiguous concrete caisson and cut rock face SOE can be brought to a planar surface to install the waterproofing by applying a smoothing course of shotcrete. With corrugated metal sheet piling, a course of plywood can be constructed on the surface of the metal spanning the concave recesses of the sheet piling. The plywood should be of sufficient thickness and braced to provide the required stiffness to place the shotcrete without vibrating. Also, the void space behind the plywood should be filled with compacted backfill or slurry grout. Without a plywood course it is difficult for the crew to place and properly consolidate the shotcrete and remove any rebound in the angled, concave void space through the reinforcement steel. Further, erecting a planar plywood substrate over the corrugated metal sheet piling can decrease the total quantity of waterproofing membrane by approximately 30 percent and facilitate an easier installation because it eliminates fixing the membrane in the deep, angled recesses of the metal sheet piling.
Tie-backs are another element to properly detail. Waterproofing permanent versus temporary tie-backs use different methods and detailing because the latter must be ‘blocked out’ and completed after the wall is constructed. Stay-in-place forming should not be used to keep the block-out open during shotcreting. It is very difficult to seal off against water ingress, especially with shotcrete. Instead, it is advisable to construct the box out with removable concrete forming tubes or wood. The top side of the box out can be slanted slightly upward to allow entrapped air to escape during final concreting of the tie-back.
Any seeping or running groundwater from the retained earth should be controlled and channeled off before and during shotcrete placement. The buildup of water pressure needs to be prevented by using drainage mats, weep pipes, or similar measures. Puddling, ponding, and freestanding water should be avoided.
A difficult condition to address is when a below-grade, raised slab is placed prior to the shotcreting of the shoring wall (e.g. a slab between different parking levels). With this construction, sequencing the top corner just under the slab is a trap for rebound pockets and overspray. Thus, this area is poorly consolidated and prone to leaks.
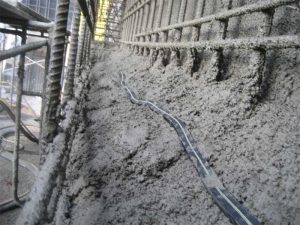
Waterproofing systems
It is generally known in the waterproofing industry the majority of leaks in western United States over the past few years have been on projects with structural shotcrete placement on below-grade, blind-side foundation walls.
Historically, waterproofing manufacturers developed systems for use with conventional CIP formed concrete—they were designed for both backfilled wall and blind-side applications. Many of them are now being used with shotcrete, and this may be one of the reasons for more water ingress on shotcrete projects than conventional CIP concrete ones.
Since it is problematic to make shotcrete watertight, manufacturers have either modified existing systems or developed new materials. On some projects, waterproofing consultants have unilaterally added detailing and ancillary products to existing systems within their specifications as a means to adapt traditional CIP waterproofing assemblies to fair better with shotcrete. In some cases, this unilateral means has resulted in conflicts with warranties because either the detailing was not the standard guidance by the manufacturer or the ancillary product was not supplied by them.
Waterproofing membrane sheets are mechanically hung from the shoring wall. Like any sheet in a vertical application with minimal fasteners, the membrane billows away from the solid backing of the shoring in many areas. With CIP, formwork is installed inward of the lagging to place the foundation wall, and normal weight concrete is poured into the formwork. The weight of the concrete pushes the membrane tight against the shoring, and vibrating consolidates it. The pneumatic placement of shotcrete often results in the mix simply bouncing off the billowed membrane, leaving voids between the membrane and shoring, and preventing uniform confinement. These voids can also compromise the stability of fully adhered membranes because hydrostatic pressure buildup can force the membrane to span a void, causing seam failure.
The maximum spacing of the anchor points must be designed properly and should be tested in a mockup. Too much sagging or spanning of the membrane between the fastener points must be avoided. The substrate should be inspected (including but not limited to pillowing and spanning) before the installation of the waterproofing membrane and shotcrete. Also, shotcrete application has the potential to force open membrane lap seams as the high-velocity shotcrete is blasted against the waterproofing and discharged at varying angles in an attempt to fully encapsulate the steel reinforcement.
While admixture-type waterproofing products have performed well in CIP concrete, there are doubts about whether they can be relied on to perform in a watertight manner in shotcrete applications. Voids and large cracks must be limited for the admixture waterproofing to perform in a watertight manner in shotcrete applications.
Ancillary material – waterstop
Due to the likely development of porous sections in shotcrete, it is good practice to specify and install both swelling strip and injectable hose waterstops in all planned concrete cold joints. The swelling strip waterstop would be either bentonite or hydrophilic rubber, and be positioned outward of the injectable hose line. Although the shotcrete industry does not consider a lift joint to be a concrete cold joint, a swelling strip waterstop can also be placed in the top of a working lift by partially pressing it into the plastic concrete. Polyvinyl chloride (PVC)-P dumbbell waterstops are not used with shotcrete construction because its wide flange obstructs the application of shotcrete, and can result with poor consolidation behind it.
Conclusion
The use of structural shotcrete to construct below-grade, blind-side foundation walls is advancing throughout the country. However, inherent quality issues with shotcrete have resulted in the industry experiencing a high rate of water ingress. Today, shotcrete is considered a primary contributing factor to the failure of below-grade waterproofing systems. Manufacturers are starting to address the issues with shotcrete by developing new systems or by adding ancillary products and detailing.
With regards to waterproofing performance, conventional CIP formed concrete has proven to be more reliable than shotcrete. If conventional CIP formed concrete is value engineered out to shotcrete, it is advisable to review the waterproofing system to confirm it is suitable for the unique application conditions associated with shotcrete. It is important to also verify if the manufacturer has specific installation guidance and details for shotcrete.