FAILURES
Deborah Slaton, David S. Patterson, AIA, and Michael Nagle
Moisture-related problems are common at critical interface conditions in the building enclosure due to discontinuities in the air/moisture control layers. One such instance is where a parapet at a lower roof meets an exterior rising wall of an upper floor or another enclosure assembly (Figure 1). Failures at this parapet-to-wall condition often occur when control layers are not fully integrated between the parapet and rising wall. The integration can be challenging when different cladding assemblies make up the exterior building enclosure. This building condition is particularly vulnerable, as rainwater that sheets down the outer surface of the rising wall exposes this interface to an increased volume of water, and, consequently, to the risk of water infiltration if integration of the control layers is not properly addressed. Lack of integration of the parapet with internal drainage mechanisms in rising walls can also result in water leakage to the building interior. Water infiltration can lead to deterioration of the wood blocking, exterior sheathing, insulation, and framing—which may not be immediately visible—as well as to interior finishes.

Photos courtesy Wiss, Janney, Elstner Associates, Inc.
At locations where water leakage to the building interior is occurring in the vicinity of such interface conditions, the detail membrane for the air/moisture control layers of the parapet, roof membrane, and/or metal coping at the top of the parapet is often terminated at the exterior face (outboard of the drainage plane) of the rising wall, rather than being integrated with the air/moisture control layers of the rising wall. Such conditions are often due to a lack of understanding by the designer and/or installer of the importance of integrating the control layers of the wall assemblies, poor trade coordination, or sequencing of the work that does not allow for proper integration of assemblies. Drawings and specifications should define fully the intended integration of the air/moisture control layers of intersecting walls. The level of detail required is largely dependent on the complexity of the condition and enclosure assemblies. Use of three-dimensional, step-by-step details can also be beneficial to illustrate complex conditions. Incorporation of pre-construction and field mockups is also essential to proper implementation of the details (Figure 2).
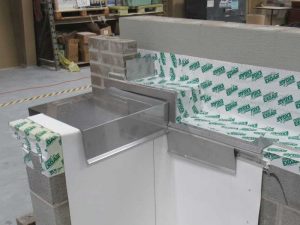
A common method of integrating parapets with the intersecting walls is by using three-dimensional fully soldered or sealed sheet metal or molded saddle flashings in combination with detail membranes that straddle the top of the parapet, with integral flanges that are in-plane with the parapet and rising walls. At the parapet and rising wall interfaces, the saddle flashings are integrated with the air/moisture control layers or accessories, to shed water to the drainage plane of the wall assembly or to the exterior. Examples of saddle flashing details are provided by the EIFS Industry Members Association (EIMA) and the Sheet Metal & Air Conditioning Contractors’ National Association (SMACNA).
Parapet-to-rising wall conditions that are aligned with fenestration and other cladding assemblies may require further consideration and specialized detailing.
The opinions expressed in Failures are based on the authors’ experiences and do not necessarily reflect those of The Construction Specifier or CSI.
Deborah Slaton is an architectural conservator and principal with Wiss, Janney, Elstner Associates (WJE) in Northbrook, Illinois, specializing in historic preservation and materials conservation. She can be reached at dslaton@wje.com.
David S. Patterson, AIA, is an architect and senior principal with WJE’s office in Princeton, New Jersey. He specializes in investigation and repair of the building envelope. He can be reached at dpatterson@wje.com.
Michael Nagle is an architect and associate principal with WJE’s office in Cleveland, Ohio. Nagle specializes in investigation and repair of the building enclosure. He can be reached at mnagle@wje.com.