
In the authors’ opinion, the roof assembly would perform satisfactorily if the ceiling vapor retarder were perfectly constructed. However, in this type of construction, it was impossible to perfectly construct a vapor retarder at the ceiling level because of the discontinuities. Ventilation of the truss space is an ineffective option to manage moisture. Unlike a steep-slope attic space, there is very little, if any, room to create airflow over relatively long distances.
Perhaps, the motivation to design an assembly as such would be to minimize the insulation costs related to the energy code requirements of recent years. While the amount of insulation installed exceeds the code requirement, the material and labor to install it were less than a code-compliant insulation installed above the roof deck. Filling the truss space with noncombustible insulation also eliminated the need for firestopping and draftstopping as noted in the 2000 edition of the International Building Code (IBC), in force at the time these buildings were constructed.
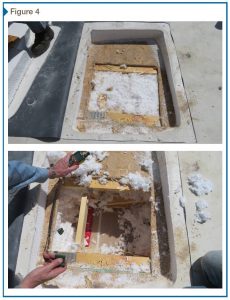
Photos © Dwight Benoy
Installing the vapor retarder at the roof deck level affords a better opportunity to achieve a complete vapor retarder. This would be an easy way to provide continuity across party walls and to seal penetrations. The vapor retarder must also be continuous from the roof to the exterior walls. This might be accomplished by using sprayfoam insulation within the truss space at the exterior walls.
On one building, the Coborn Plaza Apartments in central Minnesota, the problem was discovered approximately five years after the building was constructed when tenants of the top-floor observed mold on the gypsum ceiling and complained of musty odors. A mold remediation project was undertaken and included removal of the gypsum ceiling, vapor/air barrier, and blown-in insulation. It was discovered the exhaust ducts for the bathroom and dryer vents were poorly installed in some of the units. These ducts ran through the structural trusses and exited the exterior walls through the rim area. This duct layout also bypassed the ceiling vapor/air barrier, contributing excessive moisture to the truss space.
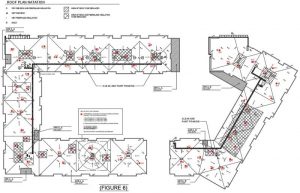
Image courtesy Inspec
The remediation work included the cleaning and sealing of the ducts, which was thought to be the only cause of the problem at that time. The moldy framing and structural roof deck were cleaned and painted with an anti-microbial paint. Some of the rotted deck was reinforced from below with additional OSB sheathing and framing.
Inspection openings from the interior were then made to verify if the remediation was effective. Excessive moisture presence was discovered. It is important to know the moisture buildup had occurred in a matter of months following the remediation. Investigation began for another source of moisture. Hygrothermal modeling was conducted to confirm or deny the inadequacy of the vapor/air barrier. Results indicated a propensity for moisture to accumulate.
Designing the repairs
Due to the damages already experienced and the potential for more to develop, it was determined Coborn Plaza needed a full roof replacement. The primary challenge was to develop a complete vapor/air barrier below the dewpoint temperature that also tied into the wall’s vapor/air barrier in order to envelope the building.
Repair options were developed and hygrothermal modeling was conducted for all the ideas. The owner required all work to be conducted from above the ceiling to minimize disruption to the tenants.