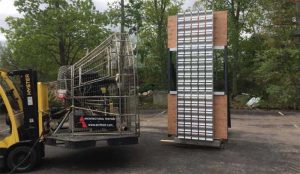
Like any reachable structural element of a building, a façade is vulnerable to vandalism. The accessibility of the façade and the nature of the installation area should be assessed to determine the susceptibility of its elements to such issues. Ground-level elements should be given particular attention, especially if they are within reach of pedestrians. In parking structures and other applications where façade elements are easily accessible, it may be worthwhile to install protective mesh on the rear of unitized sections to prevent malicious vandalism, or to apply anti-graffiti coatings on the flapper elements. In any case, the ease of flapper replacement should be considered.
Proper kinetic façade design should discourage bird or insect nesting. Minimized fixed horizontal surfaces, no open hollow voids, clear openings between the moving elements, appropriate suspension systems, and reflective materials, are just some of the measures that can be employed to deter bird nesting.
While every challenge of site location, orientation, and environmental surroundings cannot be predicted, addressing the above considerations will set a kinetic façade project on the path to success.
Performance considerations
Performance requirements are important on every building, and deserve extra attention with kinetic façade systems. Careful analysis is needed regarding the interaction between the kinetic façade elements and the building structure to which it is attached, as well as the impact of the structural behavior on the design and cost of the system.
Structural loads, especially those due to positive and negative wind pressures, need to be assessed to ensure the façade system meets the required strength specifications and the aesthetic requirements. Ice, snow, and seismic loads are also influential in the specification, design, and installation of the kinetic façade.
The method of attaching the façade elements to the building needs to be examined and coordinated as early as possible during the design and specification phase. For example, will the kinetic panels be self-supporting, or will secondary supports need to be installed? In concrete structures, this means evaluating their embeds and anchors, their interaction with the existing reinforcement configurations, and the required supporting system.
The kinetic façade system also needs to be compatible with anticipated building movements. The attachment design should account for the dynamic deflections of various types of buildings and structural systems. In parking structures, for example, the dynamic deflections from vehicle traffic must adequately be taken into account. Kinetic façade systems that cannot accommodate the required deflections run the risk of failure. It is, therefore, crucial mounting systems are designed for these deflections to ensure long-term integrity of the system is maintained. Close coordination between the façade designer, manufacturer, and the engineer of record (EOR) for the supporting building structure is critical even in the early phases of the design process.
A building’s structural demands may also govern the testing requirements of the kinetic façade. These testing requirements are often driven by local codes. However, they may also be determined by the desired façade performance. Some are ASTM standards, such as ASTM E330, Standard Test Method for Structural Performance of Exterior Windows, Doors, Skylights and Curtain Walls by Uniform Static Air Pressure Difference. Others may be custom to the project as required by the client or local jurisdiction.
Design and specification considerations
With a kinetic façade system, the focus is on material selection, the flapper elements’ size, shape, and spacing, and the suspension systems supporting them. Integration of lighting elements also can play a critical role in the system’s design and the project’s final appearance.
Material selection
As with any façade, material selection and arrangement is critical to long-term performance of the system. Due to the dynamic nature of a kinetic façade, it is critical to incorporate movement and, therefore, to wear the proper selection of ultraviolet (UV) and abrasion-resistant material. This often involves customized, accelerated testing of components and assemblies. Some materials are provided to the faced system manufacturer with testing, such as UV-resistance. Other tests, such as abrasion and wear, may need to be conducted by the manufacturer.
A nicely presented and very useful piece of information. Thanks for the post.
Thanks for this informative post.
Thanks for the informative post.
Thanks for the nice sharing.