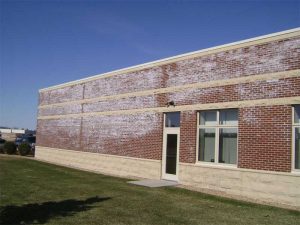
A good cavity should be “clean, but not pristine.” Craftworkers trained by the International Masonry Training and Education Foundation (IMTEF) are taught to minimize droppings through good workmanship, but also to have a full head and bed joint.
Tip 7: Minimize efflorescence and other unsightly deposits
The most common call on this topic to the author’s firm concerns efflorescence, more accurately termed a deposit than a stain (Figure 6). Sometimes called new building bloom, efflorescence often shows up at the time a contractor is trying to collect retainage and the construction team is trying to turn a job over to an owner. For efflorescence to occur, three factors need to happen:
1) Water needs to enter the masonry system;
2) There needs to be a source of soluble salts; and
3) These salts need to migrate to the surface of the brick through capillary action and are left behind when water evaporates.
Finding the source of efflorescence can be as simple as finding the source of water penetration. A less simple answer is to sample the salts to find the actual physical source. New building bloom is usually caused by excessive water in the masonry wall during construction. One should always specify covering the open cavity wall during construction. When new building bloom is the source of efflorescence, it will often disappear with normal weathering. If efflorescence continually shows up on the wall, the source of moisture should be found and repaired. If not, salts may not only deposit on the face of the wall, but also occur as subflorescence beneath the face of the brick, leading to spalling of the masonry face. Cleaning efflorescence follows the common-sense rule of first using a mild detergent with a scrub brush. If this is insufficient, proceed to chemical cleaners under strict conformance with the manufacturer’s directions. Often chemical cleaners can make the problem worse. A common mistake is to hasten the process by either not wetting a wall, if called for, using an improperly diluted cleaning solution, or leaving the solution on the wall for too long a period. All of these can lead to masonry ‘burning,’ often noticeable as a sandy mortar joint.
Lime runs typically occur at a small hole, opening, or hairline crack in the face of the brick masonry (Figure 7). Lime runs are often mistaken for efflorescence. Lime runs are caused by repeated water flow through mortar joints. The deposits are often thicker and harder to remove than efflorescence. Consult with a trusted professional to use proper cleaning techniques.
While well-written specifications and other contract documents are absolutely critical to define roles, responsibilities, and expectations, good communications is another method to ensure success.
Tip 8: Use pre-job meetings and mockups to optimize communication
Pre-job meetings with trades and ongoing site coordination meetings are critical to the success of a project. Allow trades to speak freely while respecting their contractual relationships and they will often point out some of the trade coordination and schedule/ sequencing issues that can result in poor performance. It is easy to skip these meetings while trying to maintain a schedule and productivity, or when a trade is inactive on a job, but regular attendance and participation in the process will help reduce future problems.
Thinking of the mockup as part of the communications plan also manages expectations of workmanship during construction.