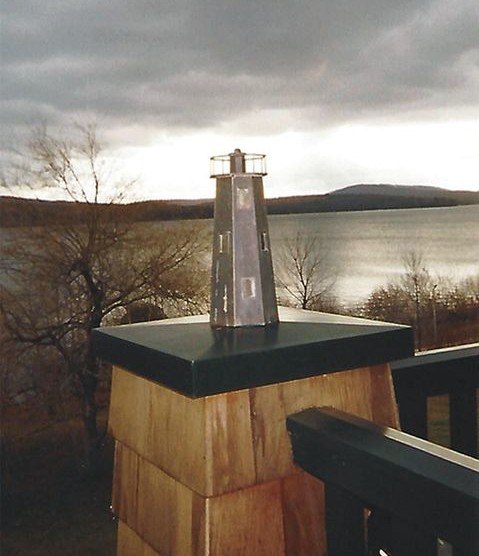
Design
Design should be performed by a qualified lightning protection system designer, such as an individual certified as a Designer Inspector (DI) or Master Installer Designer (MID) by the Lightning Protection Institute (LPI).
Complex projects, and those requiring careful coordination of lightning protection with the architectural design and layout of building services, benefit by obtaining guidance from a qualified lightning protection system designer at the early stages of project design. The system designer can be hired by the building owner or by the A/E as a consultant; in this case, detailed lightning protection drawings and specifications are issued as part of the project’s contract documents.
Alternatively, the A/E can prepare a performance specification that delegates the detailed lightning protection design to the contractor. The lightning protection design is then prepared by a qualified individual working for the contractor or sub-contractor. The design documents should be signed by a system designer, state the design complies with specified quality assurance (QA) requirements, and be submitted to the A/E as required in project specifications.
Fabrication
Components should be fabricated by firms that are UL-listed specifically for lightning protection; typical products listed for electrical systems might not be sized to handle a lightning strike. A full product line—including clamps, couplings, fasteners, and accessories—requires more than 2000 stock keeping units (SKUs) plus customization capabilities to meet the full range of construction conditions.
Installation
The International Association of Electrical Inspectors (IAEI) states, “Installation of a lightning protection system is much different from the installation of electrical service wiring.” The installer should be a firm UL-listed for lightning protection. The firm should also be a dealer/contractor member of the Lightning Protection Institute (LPI) to ensure it has an employee certified as a Master Installer by LPI.
Inspection
Lightning protection systems are not inspected by most building code departments. For assurance the job was done correctly, a building owner should insist on an independent inspection and compliance with LPI’s Master Installation Certificate program.
While stringent, this criteria should be seen as minimum acceptable practices. Additional rules govern structures containing explosive materials, flammable vapors or gases, or other dangerous materials. Owners with mission-critical operations may also stipulate higher standards. At the new South Air Traffic Control Tower at Chicago’s O’Hare International Airport, for example, the Federal Aviation Administration (FAA) boosted safety factors, created redundant systems, and installed more air terminals, including air terminals on the sides of the tower, than are justifiable in most buildings.
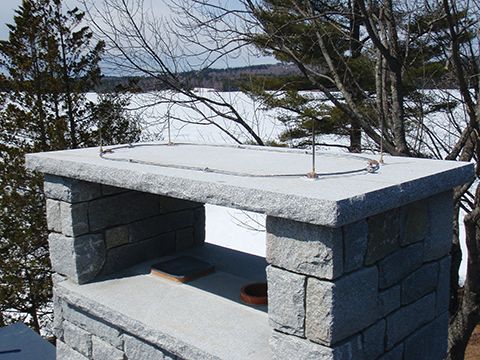
System components
Drawings and specifications prepared by the project’s A/E should not attempt to size or locate lightning protection components or repeat requirements found in the standards. Only optional requirements and information essential for administration and coordination of project should be included.
Metal
Copper and aluminum are the most commonly used metals. Copper weathers to blend into dark-colored surfaces and can be treated to accelerate patina. However, it should not be used where runoff contacts steel or aluminum.
Aluminum may be more economical and blends well with light-colored surfaces. It should be used with aluminum roofing, but should not be embedded in concrete or used within 460 mm (18 in.) of grade.
Tin-plated copper provides a dull metal appearance and is recommended for increased corrosion resistance in coastal areas. Stainless steel can be considered for use in highly corrosive environments.