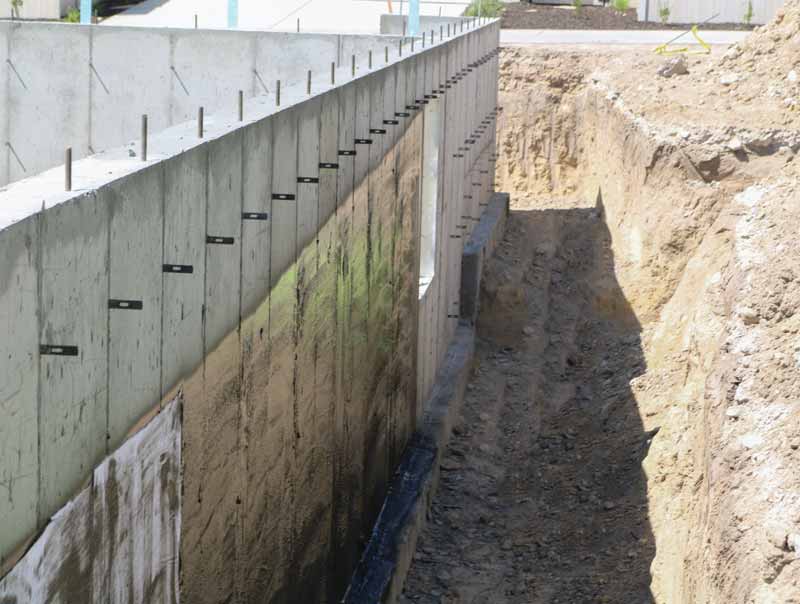
by Curt Liscum
Waterproofing is the art and science of minimizing the potential for water ingress into a structure by treating surfaces to resist the passage of water under hydrostatic pressure. While it sounds similar, waterproofing is different from dampproofing, which is defined as treatment of a surface or structure to resist the passage of water in the absence of hydrostatic pressure.
The pressure exerted by water at equilibrium at a given depth due to the force of gravity is known as hydrostatic pressure. This is important in below-grade applications because it increases in proportion to depth below the surface due to the increasing weight of the water exerting downward force from above. Fresh water exerts a pressure of about 3 kPa (0.43 psi) per foot of water, so a 3-m (10-ft) foundation wall with a 1.2-m (4-ft) groundwater table would exert a pressure of about 14 kPa (2 psi) at the base of the foundation wall. Without a waterproofing treatment on such a foundation wall, the pressure will ultimately force water into the structure, causing damage in the process.
“Positive-side” waterproofing refers to the application of a waterproofing membrane on the side of the wall in direct contact with the water and hydrostatic pressure—generally the exterior side of a wall. Positive-side waterproofing seeks to prevent the water from entering into the wall, protecting the structural element from corrosive chemicals in groundwater as well as freeze-thaw cycle damage. This stands in contrast to “negative-side” waterproofing, which refers to the application of a waterproofing material to the wall side opposite of the water contact or hydrostatic pressure—generally the interior side of the wall. Negative-side waterproofing allows the water to enter into the wall but minimizes its impact to the building occupancy. The main benefit of negative-side waterproofing is it can be installed without having to excavate and expose the exterior of the foundation wall or structure, and it is thus often applied as a repair to failed positive-side waterproofing measures.
Positive-side waterproofing can take several forms, including sheet-applied modified bitumen (mod-bit) and single-ply membranes, liquid-applied materials (both reinforced and non-reinforced), bentonite clay products, and hybrid systems. Each material and system has its advantages and specific application parameters. This article focuses on liquid-applied systems that offer several advantages including:
- monolithic construction;
- self-terminating nature;
- limited fastener corrosion;
- ease of application;
- no open flames or kettle requirements; and
- flexible material delivery.
Benefits of an STPE-based liquid product
A good example of liquid-applied waterproofing is a single-component, moisture-cured silyl-terminated polyether (STPE) elastomeric material. STPE is a hybrid product comprising silicone and polyurethane technologies. Combining these chemistries brings together the most desirable features of each and creates a durable, high-quality product. STPE technology is engineered to not only produce strong performance in end-use applications, but also to be safe for workers and the environment. Other common names for this chemistry include MS polymer, silyl-modified polyurethanes (SPUR), polyether, silyl-terminated polymer (STP), and silicone-modified polyester (SMP).
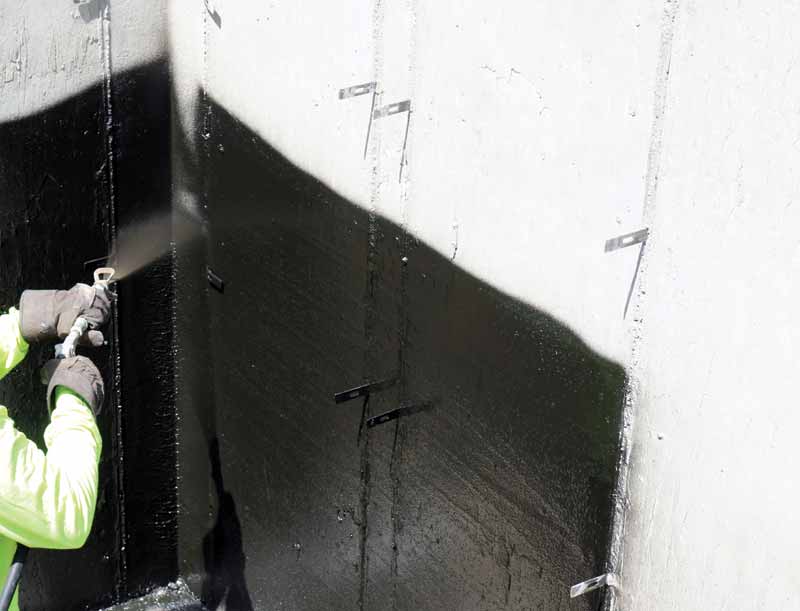
STPE-based products contain extremely low levels of volatile organic compounds (VOCs), offer excellent cure times, and perform well at temperatures as low as 1.6 C (35 F). STPE technology is suitable for projects requiring flexibility in design, as these products typically do not require primers, offer a broad adhesion profile for many types of projects, and are compatible with a wide range of substrates.
Single-component products are also beneficial to the installer as they can be used directly from the pail with minimal initial mixing. Most single-component products must be mixed for uniformity and consistency, but catalysts, accelerators, hardeners, or other components need not be added. A high-solids, single-component, moisture-cured STPE elastomeric, liquid-applied waterproofing material is also advantageous as the amount of material applied to the surface is close to the finished membrane thickness. The higher the percentage of solids within a material, the lower the volatile content, and therefore, there will be little shrinkage in film thickness as solvent evaporates during the curing process. For instance, using a 98 percent solids material (the recommended minimum) and targeting a 2.2-mm (90-mil) wet film thickness (WFT) application rate, the cured finished membrane would be about 2-mm (88-mil) dry film thickness (DFT) of material.
Unlike other solvent-cured, adhesive-adhered, self-adhered, or heat-welded products, a liquid-applied STPE product will not blister, outgas, or lose adhesion when installed over damp or fresh “green” concrete surfaces due to STPE’s moisture-curing nature. Once the wall obtains sufficient strength for form removal, and the initial concrete set is achieved (generally within two to seven days), the waterproofing material can be applied. This can significantly accelerate the construction schedule.
Cure time will vary from minutes to hours depending on applied film thickness, temperature, and relative humidity (RH). Typical cure time is three hours for 0.7-mm (30-mil) applications at 21 C (70 F) and 50 percent RH, but this may be extended in cooler, drier climates. In ultra-dry climates, additional water misting may help accelerate curing. Full, normal curing is anticipated in three to four days, and supplemental coats and repairs should be performed within 72 hours of the initial application.
Single-component, moisture-cured STPE elastomeric, liquid-applied waterproofing material is manufactured in several viscosities (or thicknesses) depending on application method. The lower the viscosity—measured in centipoise (cP)—the easier it is to deform, or in this case, apply. One advantage of a well-formulated, single-component, moisture-cured STPE elastomeric, liquid-applied waterproofing material is it has the necessary viscosity to be spray applied. This can create labor savings for contractors installing below-grade waterproofing.