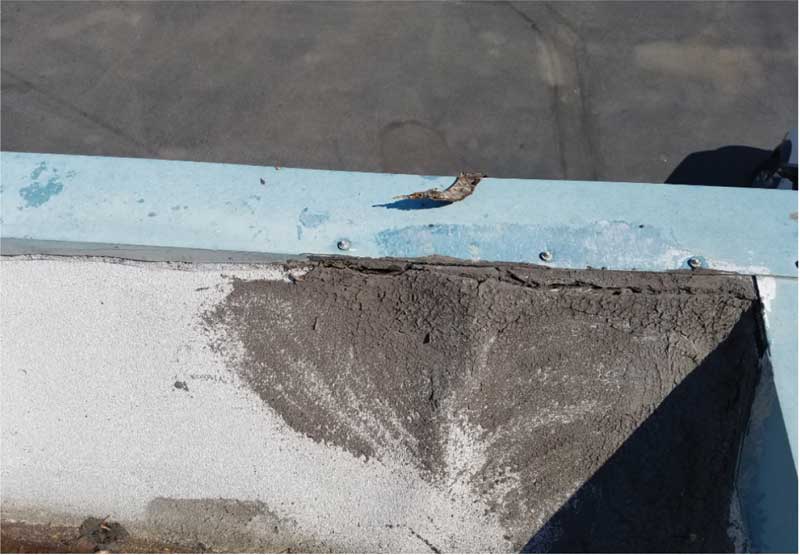
The “when” of coatings
Two especially important cases for coatings are modified bitumen (mod-bit) and architectural metal roofing. Mod-bit comes in two forms—styrene butadiene styrene (SBS) and atactic polyproylene (APP) in either granulated or smooth finish. Often mod-bit is used as the “cap sheet” on a BUR assembly, but even when applied directly over asphalt, a coating application is much the same. Mod-bit is a robust, simple, repairable, and cold-weather-friendly product with needs—protection from weather and heat. Granulated mod-bit, commonly SBS in northern regions, is a material that ages both thermally and by a combination of UV light and moisture attack to the asphalt underneath. Eventually asphalt weakens and the granules release, at which point there is little protection left and soon the reinforcement gets exposed. However, an acrylic coating provides adhesive and encapsulating characteristics, even if applied lightly (1.5 to 2 m2/L [1.6 to 1.2 gal/100 sf]). The result is a cooler surface and less oxidation, postponing the eventual embrittlement of the roof cover. Subsequent reduction in UV and moisture significantly slow the aging process. Some manufactures now provide pre-coated mod-bit to combat these issues. Additional coating, or better yet, reinforcement over the seams and bleed lines, will slow the other main route of failure via ruptured seams.
Coating can be accomplished early or late in the membrane’s service life, but it is best done the second year. If the roof has begun to lose a significant amount of granules, a liquid membrane can still extend it another 15 years or more. The key is to treat the roof before it has significant degradation, making 10 years a good outside target date for coating. Leaks mean wet insulation, resulting in lost energy. In cold climes, the importance of efficient heating is such that investing in coating on a wet roof is throwing good money after bad. Granulated mod-bit and coatings work especially well together. A mod-bit/coating system
is also a good candidate for covering uninsulated concrete decks.
Metal roofs
Metal roofs have the longest potential service life of any major roofing system, but they often leak. The issue is with expansion and contraction, which especially impacts the fasteners. Some metal roofs have hidden fastening, but all generally have horizontal seams that can experience ice damming or wind-driven rain, creating a route for moisture entry. Coatings combined with reinforcement at these points can easily add another 20 years of service to such a roof. Acrylics, urethanes, and silicones, as well as styrene ethylene/butylene styrene (SEBS), asphaltic, and silicone hybrid (SPUR) coatings are acceptable choices. Acrylics can be easily colored and tend to hold up well on metal, while silicones are best in cold weather applications. Urethanes excel at crack bridging and adhesion, and often perform best on a really problematic metal roof. In all cases, these coatings provide color selection, often a key reason why metal was specified in the first place. A typical metal roof coating project involves:
- removing severe corrosion;
- replacing deteriorated panels;
- tightening and sealing all fasteners;
- detailing at seam level;
- reinforcing horizontal laps; and
- applying a protective coating.
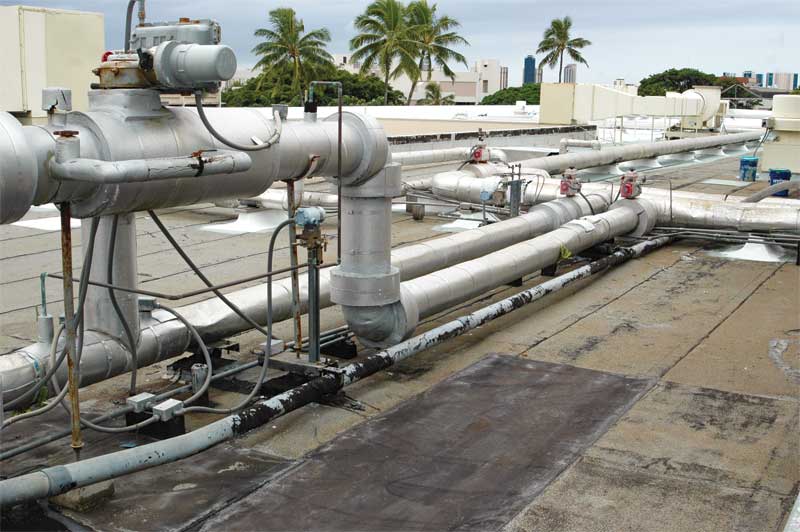
Photos courtesy GAF
A light-color finish helps mitigate the severity of expansion and contraction cycles. Leaks should be repaired with a level of redundancy to ensure a longer service life than may have been initially provided, making proper detailing the key to this application. Proper coating of a moderately rusted galvanized metal roof illustrates a best-case situation. Even a dark-colored finish can reduce heat buildup as a result of improved thermal emissivity because a coating changes the rate at which heat is released from metal. White coating works in two ways—it is reflective, so less solar energy is absorbed in the first place, and it also allows heat to escape about three times faster. A white coating can drop peak temperatures by as much as 50 C (122 F). The reduced mechanical stress translates to a lower risk of leakage in the long run.