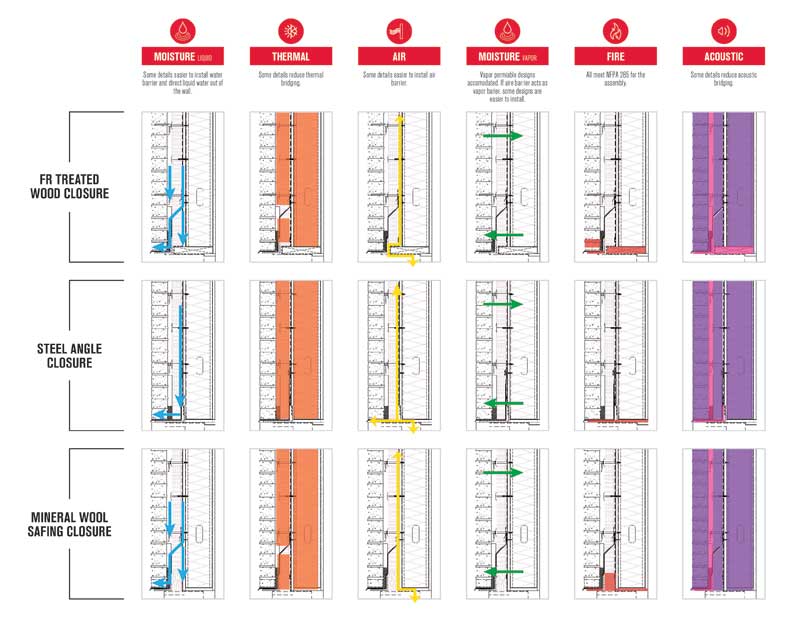
Image courtesy Owens Corning
Making compromises at penetrations
These are three common transitional areas to examine when detailing building enclosures. Yet, there are still other critical areas to identify in transitions when considering changes in material and plane (e.g. outside corners, inside corners, verticals to horizontal, diagonals, etc.). Penetrations are another important area to consider when detailing—particularly pipe penetrations and window openings. While not all could be covered in this article, applying the building science fundamentals when analyzing details will ensure all components have been addressed to create continuity and performance.
In addition to transitions, each penetration should also be evaluated during detail design, and will likely require a compromise between fundamentals based on the primary goals of each project. In Figure 7, three window details are approved for an NFPA 285 assembly. How can the appropriate one for the project be selected? This is where applying building science fundamentals will demonstrate the best choice or compromise.
With regard to a continuous water barrier, the steel angle detail is likely the easiest to construct and provides a direct path for water out of the wall while separating water entering into the window system. However, when analyzing the same three details for thermal performance, the detail featuring mineral wool safing would eliminate the most thermal bridging at the opening. Incidentally, the same mineral wool detail is likely easier to install with air barrier membrane flashing, whether that flashing is a liquid or tape material. If the assembly is to be vapor-permeable, all of the details would likely perform equally. However, if the air and water barrier is to act as a vapor control layer, the mineral wool detail will be particularly appealing to installers. (If the vapor control is provided by a membrane on the interior, behind the gypsum board, in a different climate, these details would probably be equally easy to construct.)
Analyzing all three detail options for acoustical performance, the mineral wool safing detail provides the least conductive materials in contact with each other. As demonstrated by this exercise, given a series of design options, analyzing for the continuity of materials and design fundamentals may make one detail stand out.
Quality control and assurance
Having reviewed building science fundamentals, strategies to maintain continuity at transitions, and selection of the best penetration options, it is also important to address issues that can occur with sequencing, compatibility, adhesion, and testing in the field.
Sequencing
When considering sequencing, it is best to begin with weather-lapping materials. A high-performing product may still fail when installed incorrectly—usually, in the wrong sequence. Professionals should ensure materials lap correctly so water drains and does not sit on seams. When openings are not correctly weather-lapped, the air and water barrier is not tied in with the rest of the wall, and water drains into the building instead of away while air is allowed to leak. Other issues to consider are trades arriving and engaging at the jobsite at different times. For example, one should ensure the air barrier goes in before the windows, and that the roof protects the walls from filling up with water before the air and water barrier can be installed.
Compatibility
Adhesion and compatibility between different components is critical in making air and water barriers continuous. The test method to ensure materials adhere to their substrates and each other is often specified as ASTM C794, Standard Test Method for Adhesion-in-peel of Elastomeric Joint Sealants, where one product is applied to another and the two are pulled apart with the ultimate goal of cohesive versus adhesive failure. Chemical compatibility can be tested for using American Architectural Manufacturers Association (AAMA) 713, Voluntary Test Method to Determine Chemical Compatibility of Sealants and Self-adhered Flexible Flashings, where two materials are applied in contact with each other and then conditioned with temperature and time exposure.
One particular area of consideration is transitioning from roof membrane to wall membrane. The products used in these locations may not be compatible, and it is important to verify this prior to installation. It is also critical to review the sealant at the window opening—another common area of weakness. Incompatibility can also occur between the window manufacturer’s sealant and the air barrier manufacturer’s flashing. If incompatible, the building owner may be left with softened black goo dripping down the wall. Specifying test methods for compatibility and adhesion is one way to ensure a continuous system prior to installation.
Verification
One final consideration to remember throughout the process is verification. This begins with a peer review—whether in office with colleagues or delegated to expert consultants, building envelope details should be reviewed with multiple sets of eyes, as even experts will miss areas for improvement on complex details. An additional resource available is manufacturer review, since few know a product better than those who produce it. The manufacturer knows which products are compatible, what sequencing issues may arise on a jobsite, concerns with adhesion, and typical ways of detailing. Professionals can look to them as a resource for everything from ASTM E2357 air barrier testing to E2307 perimeter fire containment engineering judgements and project-specific hygrothermic analysis.
The review process does not stop once a project is awarded; it is important to have preconstruction meetings with everyone on the jobsite that will be interacting with the materials, reviewing the sequence, compatibility, any warranty concerns, and how the details will go together. By sharing the vision prior to the start, previously discussed pitfalls such as weather-lapping, contractor sequencing, and compatibility can be eliminated. For example, the mason may discover striking joints flush creates a better surface on which the air barrier installer can apply the system consistently at the correct thickness.
Mockups
It is also critical to erect mockups. Many times, mockups are specified, but later disregarded due to shortage in time and budget. Being able to observe construction of mockups as part of preconstruction meetings, and to review and agree on detailing with all trades involved, allows for concerns to be addressed before they become costly changes during construction.
Testing
In-situ testing verifies the correct installation and performance of project systems. This can take the form of a test under ASTM E779, Standard Test Method for Determining Air Leakage Rate by Fan Pressurization, as required in newer building codes such as the International Green Construction Code (IgCC) or International Energy Conservation Code (IECC), or thermal imaging to detect any thermal bridging that may be corrected before more damage occurs. More projects are requiring the verification of workmanship to ensure anticipated performance.
Conclusion
When looking at a detail, it is important to verify the products are properly sequenced, can be adhered, are compatible, and will together achieve any specific warranty through use of all of the components in the correct way. Professionals should remember to involve the entire team and ensure all aspects have been reviewed together throughout the entire process, not just during construction. These quality assurance measures, combined with quality control testing and verification, serve to help ensure continuous, high-performing systems.
Tiffany Coppock, AIA, NCARB, CDT, ASTM, RCI, EDAC, LEED AP, is Owens Corning’s commercial building systems specialist. She provides leadership and technical guidance in building science, testing, and documentation to design professionals and the Owens Corning team. Formerly, Coppock was a building science manager answering technical questions, reviewing drawings and specifications, and giving educational sessions on topics such as air barriers, waterproofing, vegetated roof assemblies, and insulation. She holds degrees from Texas A&M University and the University of Colorado, and is a registered architect with specialization in healthcare and historic preservation. Coppock can be reached via e-mail at tiffany.coppock@owenscorning.com.