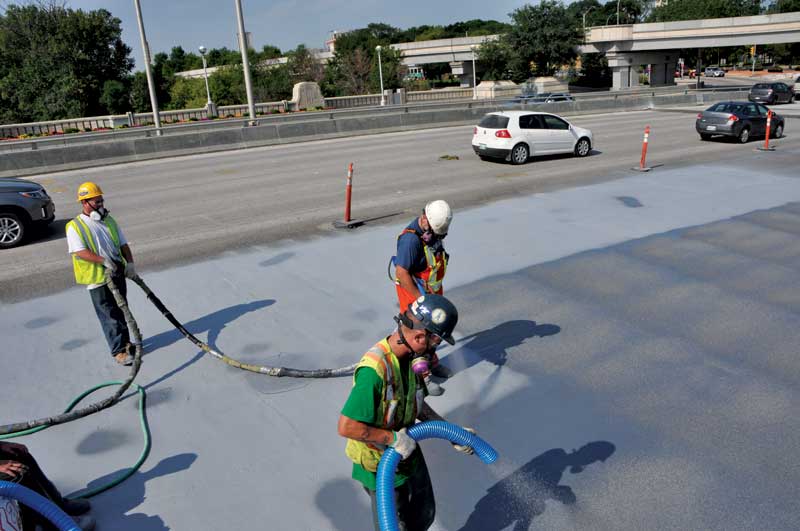
by Del Williams
A recent 60 Minutes episode, “Falling Apart,” noted America’s roads, bridges, airports, and rail lines are outdated, neglected, and need to be fixed. The segment goes on to state, “nearly 70,000 bridges in America—one out of every nine—is considered to be structurally deficient.” Indeed, according to the American Society of Civil Engineers (ASCE), “32 percent of the major roads in America are now in poor condition and in need of major repairs.”
The majority of America’s infrastructure has outlived its intended service life, and a failure of traditional waterproofing coatings has led to significant corrosion of structural elements, including corroded rebar and crumbling concrete. New high-performance waterproofing alternatives are replacing more traditional techniques, such as sheet goods and short-term liquid sealants, to help civil and structural engineers cost-effectively protect and maintain critical infrastructure. Examples of projects that can be protected
by these technologies include:
- rail;
- highway, and pedestrian bridges;
- tunnels;
- parking decks;
- airport terminals; and
- entrance/exit ramps.
Spray-applied waterproofing products—comprising spray-on materials such as polyureas, polyurethanes, and poly methyl methacrylates (MMAs)—are seamless, rugged, quick-curing, impervious to water, able to bridge cracks, and capable of lasting decades without extensive maintenance.
“Spray-applied waterproofing now accounts for over 50 percent of the membranes applied to our bridges,” said Alexander Bardow, Massachusetts’ Department of Transportation (MassDOT) state bridge engineer.
“What drove us to spray-applied waterproofing is its enhanced durability, bonding to concrete, and crack bridging ability,” said Bardow, who oversees and helps to prioritize work on 5000 bridges that receive federal funds for MassDOT. “If cracks form due to deck deterioration or traffic loading, then water gets into those cracks and the concrete matrix. The [underlying] membrane must be pliable enough to accommodate these cracks without failing.”
Drawbacks of traditional techniques
In past decades, MassDOT utilized mopped emulsion reinforced with fiberglass fabric for bridge decks, then later turned to sheet goods. While traditional methods of waterproofing such as these, or non-elastomeric coatings like epoxies and paints, have long been used, they can have drawbacks, and must be continually inspected and maintained over time.
Reinforced emulsion was not a good deck waterproofing system because it debonds and allows water to seep underneath and into the deck. After failure with reinforced emulsion, prefabricated sheet-applied membranes became the focus. These are easy to apply, but more durability was necessary.
Non-elastomeric coatings such as epoxies and paints do not have the elasticity to bridge cracks, and tend to be ‘moisture-resistant’ rather than truly ‘waterproof.’
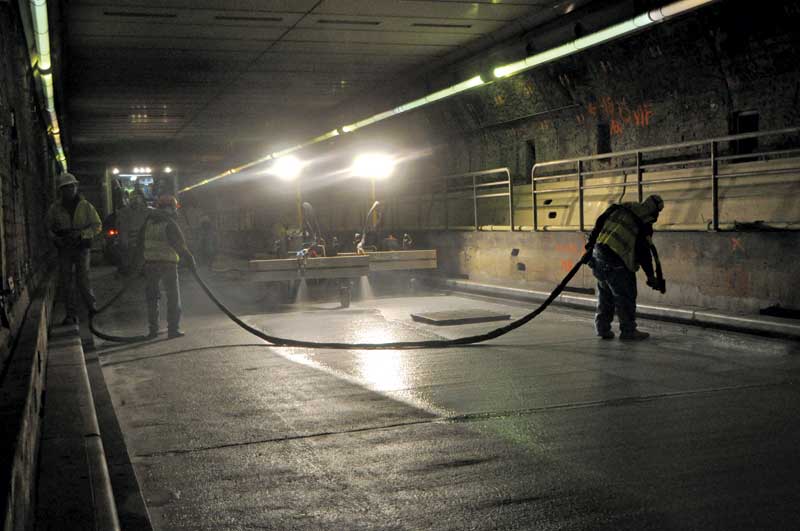
Spray-applied waterproofing membranes, on the other hand, display better performance and have measurable performance characteristics that can be counted on for extended deck life.
“We can expect spray-applied waterproofing membranes to last about 30 to 50 years,” Bardow adds. “We would still repave and resurface the asphalt overlay, but would not need to do anything to maintain the underlying waterproof membrane during that time.”
Spray-applied waterproofing
A newer generation of elastomeric coating, spray-applied waterproofing membranes are resolving the longevity, reliability, and quick application issues of older techniques.
Since crack-bridging is a critical element of these newer technology membrane systems, ASTM has developed its ASTM C1305, Standard Test Method for Crack Bridging Ability of Liquid-applied Waterproofing Membrane. For liquid membranes with an independent wearing course, the test consists of applying the membrane system across two concrete masonry units (CMUs) with matching faces. The test sample is then brought down to –26 C (–15 F) for 24 hours to stabilize it at this temperature. The testing requires the two blocks be pulled apart at a rate of 3 mm (1/8 in.) per hour to a maximum opening of 3 mm, then closed to a zero gap at the same speed. The test fixture must maintain the sample at the –26 C temperature through the 10 cycles of testing required. Some manufacturers have conducted this test for many additional cycles to further assess their product.
The American Railway Engineering and Maintenance-of-way Association (AREMA) also includes spray-applied membranes in its guidelines, and some products exceed these parameters. The spray-applied waterproofing membrane previously cited, for instance, exceeds AREMA Chapter 8, Part 29 requirements for waterproofing membranes, and is designed to last the lifetime of the structure. It is impervious to de-icing chemicals, water, ballast, stray current, and other factors that contribute to accelerated deterioration and wear of elevated rail/road structures and tunnels.
We are an emerging bridge waterproofing comapny based in rhode island and we are offering many products like Dek RR, Dri span.
Our website is http://www.dekshield.com/ and I hope you will add backlink in your website and we will add your website link in our website.