
by Christopher P. Crall, PE, and Ronald L. King
In 2010, a mechanical insulation energy appraisal was conducted on various facilities around Helena, Montana. The objective was to determine the energy, cost, and emission reduction opportunities available through repair, replacement, and/or maintenance of mechanical insulation systems in 25 pre-selected facilities.1
The Mechanical Insulation Assessment Pilot Program was part of the data-gathering goal of the Mechanical Insulation Education and Awareness Campaign (MIC). Executed under the U.S. Department of Energy’s (DOE’s) Advanced Manufacturing Office in conjunction with the National Insulation Association (NIA) and its alliance partners, MIC seeks to raise awareness of the energy efficiency, emission reduction, economic stimulus, and other benefits of the material in the industrial and commercial markets.
The potential of mechanical insulation—thermal protection for piping, equipment, and other devices—to play a significant role in reducing energy intensity is immense. Unfortunately, the lack of sufficient data to support its energy efficiency potential, combined with a deficient understanding of what mechanical insulation is and how it can be used, impedes policy- and decision-makers in developing supportable cases for increased use and maintenance of the mechanical insulation.
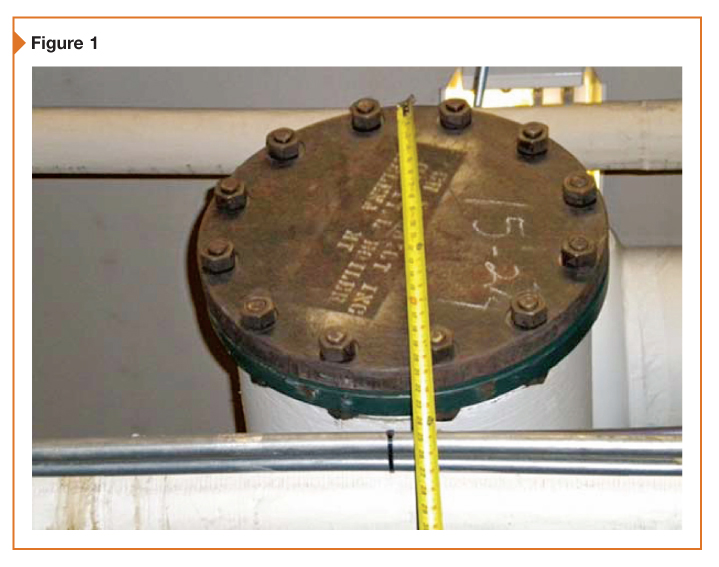
The study
The overall approach of the program was to assemble a team of insulation professionals to conduct an appraisal of State of Montana facilities in the Helena area. The assessment team, with assistance from state personnel, performed tasks including:
- identifying opportunities to improve insulation in the mechanical rooms visited;
- estimate costs to improve or upgrade the insulation systems;
- estimate savings (in dekatherms, dollars, and carbon dioxide [CO2] emissions) associated with the insulation upgrades, and calculate resulting payback period and return on investment (ROI).
The list of candidate buildings in the area was developed and prioritized based on the energy-saving potential from mechanical insulation. Based on the program, buildings with steam and/or hydronic heating systems were included, while those with forced air furnaces were not. The 25 facilities visited ranged from office buildings, assembly facilities, and dormitories to maintenance facilities and museums—representing roughly 1.3 million sf (120,774 m2).(As the original research focused solely on imperial measurements, conversions to metric throughout this article are approximate.)
The study’s scope was limited to the assessment of mechanical insulation on piping and equipment in mechanical rooms. Opportunities for repair and replacement of insulation on piping and ductwork within the building itself were not considered. This study should not be considered an energy audit of the buildings visited. Energy conservation opportunities related to building envelope insulation or sealing, lighting, controls, ventilation, and equipment maintenance were also outside the study’s scope.
For each mechanical room, an insulation summary identifying items where the material was missing or had sustained significant damage was developed. The team also identified the thicknesses required to bring the insulation level up to the existing level. No attempt was made to ‘optimize’ the level of insulation or to identify whether the standing level would meet or exceed those required by local building codes. Also, no assessment was made of the existing insulation’s efficiency. Additional savings may be possible by upgrading the level, but these savings would be minimal compared with insulating the uninsulated or damaged items identified.
During the field visits, additional information was collected about the energy systems in each mechanical room to enable the estimation of energy savings, including:
- the mechanical room’s location within the building;
- operating temperatures;
- estimated hours of operation;
- estimated efficiency of the equipment; and
- general control strategies.
Budget-type cost estimates were also developed based on the summary information on a facility-by-facility basis.
Hi, I work with Indiana Legislative Services and would like to know the average cost of installing mechanical insulation. I understand this is difficult to estimate, but if you could provide some sort of range I’d appreciate it.