Significance of results
The results of this study demonstrate there are numerous opportunities for improving the mechanical insulation application in steam- and hydronic-heated buildings. One question prompted by the appraisal is, ‘Why are there so many pieces of missing insulation?’
In many locations, it was obvious a maintenance task had required removal of the insulation, which was simply not replaced after the maintenance was completed. This was observed in several locations where a domestic hot-water (DHW) storage tank had been removed and replaced with a newer tank, and piping connections to the tank were left uninsulated. It is possible the personnel performing the work did not have the materials or proper training to complete the job.
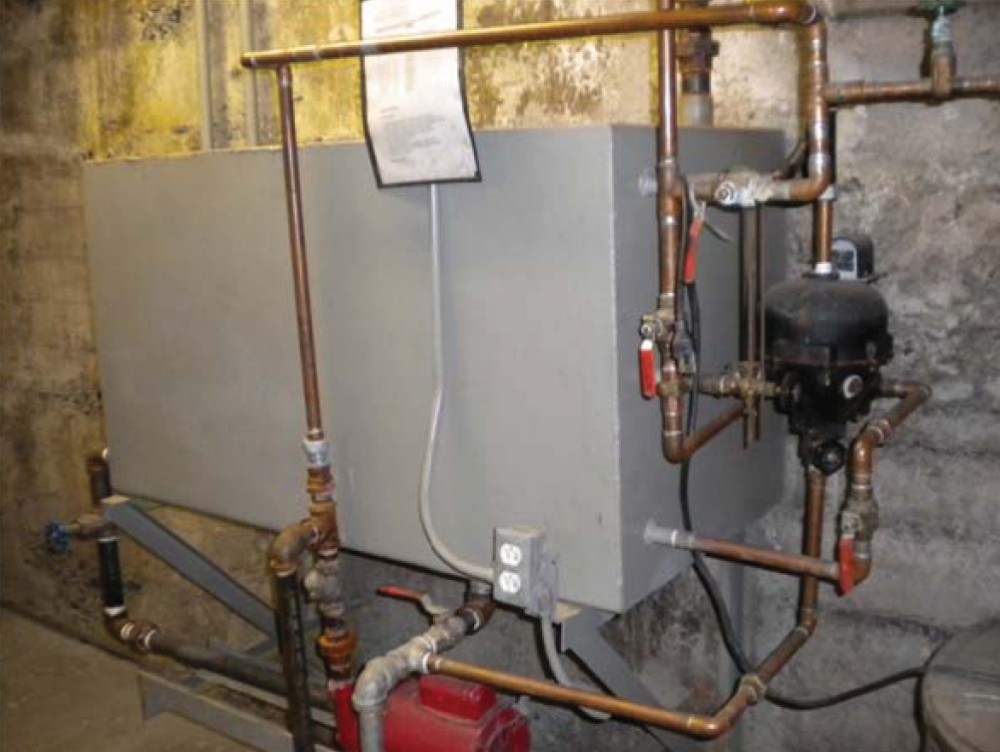
In some areas, either mechanical damage or leaks had occurred and the damaged insulation had not been replaced. More common, however, were items that had never been insulated. For buildings and systems designed and built when energy was less expensive, the ‘extent of insulation’ was not nearly as complete as it is today. Items routinely left uninsulated include:
- pipe unions;
- strainers;
- steam traps;
- condensate tanks;
- expansion joints;
- valves;
- flanged joints;
- pumps; and
- tanks.
The DHW systems in the buildings illustrated the interactions often present in energy conservation projects. Numerous buildings contained newer high-efficiency DHW storage tanks. Some buildings, however, used older conventional-style gas-fired water heaters. For older DHW tanks, the addition of a 1.5-in. (38-mm) thick tank blanket to minimize heat loss was analyzed. These DHW tanks typically operate year-round (i.e. 8760 hours). For a typical 24 by 60-in. (610 by 1524-mm) tank, energy savings can be approximately $30 annually. These savings were included in the analysis where applicable. Depending on the age of the DHW tank, it may be more reasonable to consider replacing these tanks with high-efficiency units. This alternative (and mutually exclusive) option was not investigated in this study.
A related interaction issue concerns the DHW circulating systems. Most of the buildings studied use circulating pumps in the DHW loops. These pumps minimize city water consumption since occupants have hot water at fixtures on demand, rather than waiting for hot water. Some facilities have been fitted with timers to limit the circulating pumps operating hours—and the associated heat loss from DHW piping—to occupied hours.
In other buildings, the circulating pumps continuously run. For these facilities, the insulation replacement items are appealing because savings are directly proportional to operating hours. The alternative option of installing a timer to limit hours of operation would reduce the savings from insulation. The two options, however, are not mutually exclusive, and installation of timers should be considered in addition to replacing any missing insulation in the DHW loop.
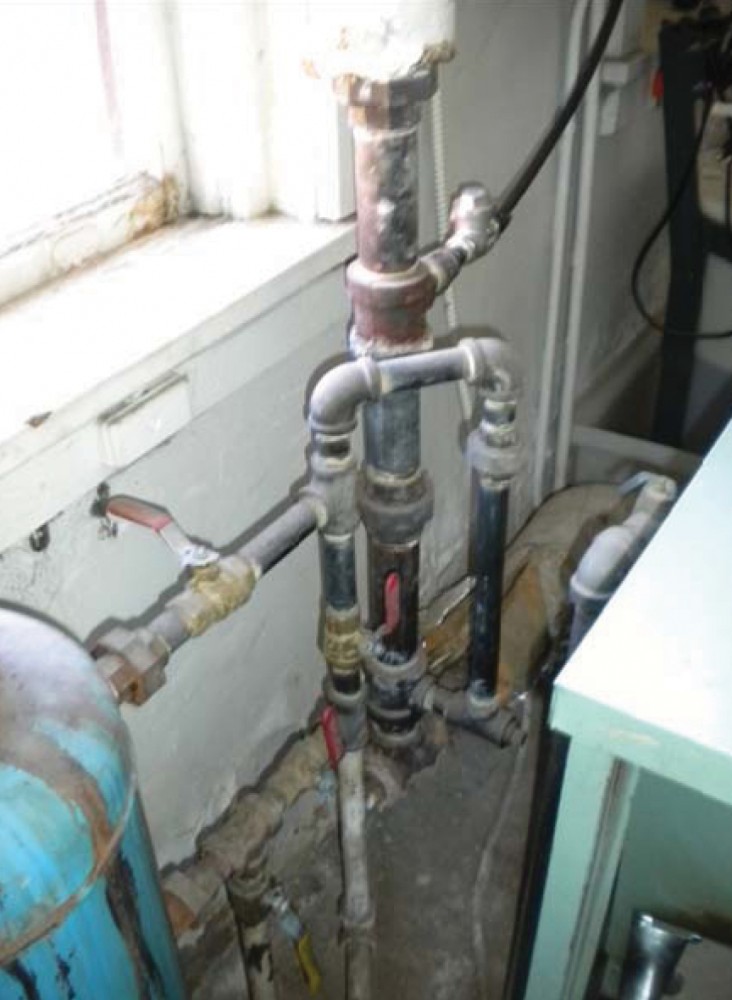
Extrapolating the findings statewide
One of the program’s objectives was to use the results to estimate possible savings if the study were expanded to cover similar state-owned buildings. The State of Montana has an inventory of approximately 2000 different types of buildings, from roadside rest facilities and historical village gift shops to prisons and university football stadiums. Many of these facilities are small, seasonal, and with specialized use and/or limited occupancy. As the study’s results do not apply to all facilities, extrapolation to every state building is not accurate. However, projections to similar state-owned facilities are possible and may be useful.
The initial step toward that objective was to review a list of state buildings considered potential candidates for inclusion in mechanical insulation upgrade projects. The information provided included:
- building designation and location;
- year built;
- occupancy code;
- gross area (in square feet);
- number of stories; and
- number of full-time employees.
The list contained a total of 142 buildings with a total gross area of 2.35 million sf (218,322 m2).
The pilot study of Helena buildings covered several of the larger state buildings, representing a significant percentage of the total. Overall, approximately 55 percent of the square footage identified on the candidate list was included in the study discussed. As a first-order estimate, the energy savings from the Helena study can be prorated based on building area. Annual energy savings from the 25 facilities analyzed averaged 4.6 kBtu/sf/yr, which is about $0.043/sf/yr. If these savings were prorated to the statewide candidate list (i.e. 2.35 million sf [21,8322 m2]), they would total 10,800 DKT, or $101,000, annually.
However, additional analysis could refine this estimate. For example, it was determined steam- and hydronic-heated systems will have more opportunities for mechanical insulation than their forced-air counterparts. Additionally, some candidate buildings have already been addressed. More information about the building inventory statewide would allow a more precise estimate, but an order-of-magnitude statewide savings of 10 billion Btus—eight percent savings annually—is not unreasonable. Installation costs would be similar, so annualized returns of 24 percent could be achieved.
Hi, I work with Indiana Legislative Services and would like to know the average cost of installing mechanical insulation. I understand this is difficult to estimate, but if you could provide some sort of range I’d appreciate it.