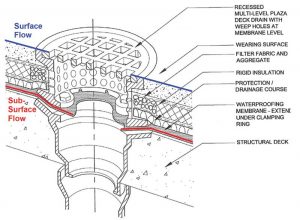
Keeping water drained away from the deck will increase its service life. Standing water rapidly deteriorates the deck components, such as the waterproofing membrane, the concrete slab, and the rebars. Water within the assembly can also cause extra damage via freezing and thawing cycles in cold climates. Maintaining a minimum slope of two percent (6.35 mm per m [0.25 in. per ft]) at the topping (for surface flow) and at the deck slab (for subsurface flow) is essential to direct water toward the highly recommended double-tiered drains (see Figure 2, page 50). Considerations should be given to the effects of structural deflections and building settlements on the magnitudes of slope.
Installation inspection and flood testing
The installation quality of the waterproofing membrane is as important as the selection and design of the waterproofing system, as the integrity and continuity of the membrane are paramount to the performance and durability of the parking deck system. Hiring a third-party reviewer to inspect installation and test the system is beneficial—especially before adding any additional layers and the wearing course. Visual reviews should be conducted frequently as part of the quality control program. Testing can be employed as a quality assurance measure.
Flood testing using ASTM D5957-98, Standard Guide for Flood Testing Horizontal Waterproofing Installations, is a good method to verify the continuity of the waterproofing membrane. This test suits parking decks since they mostly have a slope of no greater than two percent with liquid-applied, adhered, or loose-laid waterproofing membrane. Testing is best performed for a minimum of 24 hours and maximum of 72 hours, when rainfall is not expected. If a failure happens, the tested floor will be drained, and the breach will be mended. A retest will then be performed using the same conditions. Required preparation work includes installing containment assemblies and plugging the drains with inflatable devices consisting of rubber balls, draw chains, and rings, as well as other standard plumbing fixtures.
As an alternative to flood testing, utilizing electric leak detection (ELD) to test the integrity of the waterproofing membrane is safe, fast, accurate, and economical. ASTM D7877-14, Standard Guide for Electronic Methods for Detecting and Locating Leaks in Waterproof Membranes, describes standard procedures for using electrical conductance measurement methods to locate leaks in waterproof membranes. This method is suited for a typical parking deck, where the concrete acts as a conductor and the adhered membrane is the insulator. When there is a hole in the membrane, a breach will be detected to determine the hole’s location.
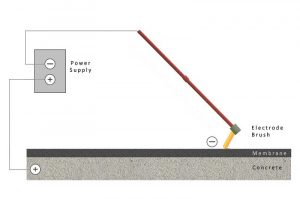
High-voltage ELD is becoming more popular compared to low-voltage ELD, because the latter needs wet membrane and cannot test vertical surfaces. The presence of drains and an insulation layer under the membrane can cause a misreading of results. Those limitations can be overcome by applying methods some would consider impractical, such as installing electrically conductive primer or lightweight wire grid under the membrane. Some waterproofing membranes such as butyl and ethylene propylene diene monomer (EPDM) also behave as conductors, so ELD cannot be executed on those membranes.
Looking forward to including the specifier as a resource to our office library.