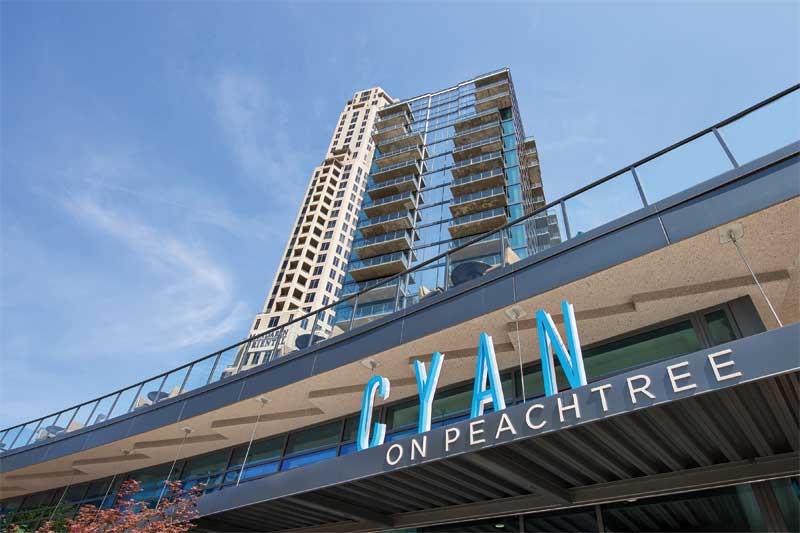
Code and standard requirements
In practically every situation, CI is essential to meeting key energy codes, including ASHRAE 90.1, the International Energy Conservation Code (IECC), and numerous state energy codes. To meet such lofty goals as net-zero-energy operation, Leadership in Energy and Environmental Design (LEED) certifications, meeting Passive House, or performing to other standards seeking reduced carbon footprints or greenhouse gas (GHG) emissions, CI is a necessity.
Some of these benchmarks offer prescriptive solutions. Using the project’s climate zone, the space’s conditioning category, and maximum allowable U-factor (i.e. rate of heat loss), ASHRAE 90.1 offers guidance on applying CI to achieve required performance levels. Using an example from North American Insulation Manufacturers Association (NAIMA), a metal-framed worship facility in Raleigh, North Carolina, could meet the required U-factor in 90.1 with an R-16 fiberglass batt layer and R-5.6 of CI for the roof, along with walls constructed with an R-10 fiberglass insulation layer and R-5.6 of CI.
Cost requirements
Many project teams practice lean construction methods, seeking to optimize building systems for life-cycle economics. According to architect Herbert Slone, RA, insulation life-cycle cost (LCC) can be expressed as:
FC+M+R+E–RV
Where:
- FC is first cost;
- M is maintenance and repair expense;
- R is the replacement cost;
- E is energy expenditure; and
- RV is resale value.
While first cost increases as R-value does, at the same time energy costs drop, reducing operations expense. In this way, optimal insulation can be defined for any given climate, building type, and facility usage patterns.
Life-safety requirements
There are life-safety requirements that affect the
use of CI. Most relevant for U.S. building teams
is National Fire Protection Association (NFPA)
285, Standard Fire Test Method for Evaluation of
Fire Propagation Characteristics of Exterior Non-loadbearing Wall Assemblies Containing Combustible Components. If the CI layer for exterior walls is made of foam plastic, or if the air and water barriers are combustible, the NFPA 285 fire test is mandated for walls of construction types I, II, III, or IV—even though these wall types are, by definition in the International Building Code (IBC), to be made with noncombustible materials. (There are some exceptions. The design professional should refer to 2015 International Building Code [IBC] Chapters 14 and 26.)
With the rise in use of CI and air barriers, NFPA 285 has become a ubiquitous requirement for building projects. Specifiers often check to ensure their proposed assemblies have already been subjected to the costly test—an impressive full-scale multi-story mockup subjected to a fire intended to simulate a blaze originating from an interior room. In the 2015 IBC, six sections (including 1403.5 for weather-resistive barriers [WRBs] and 2603.5.5 for foam plastic insulation) reference NFPA 285.
In general, project teams must focus on NFPA 285 early in the design phases as the market may not offer enough compliant assemblies for walls of greater than 12 m (40 ft) above-grade. Additionally, some rainscreens and other cladding types have yet to be tested with foam plastic insulations. In these cases, the design team can choose to employ a tested combination of products or, in some cases, have the proposed assembly tested.