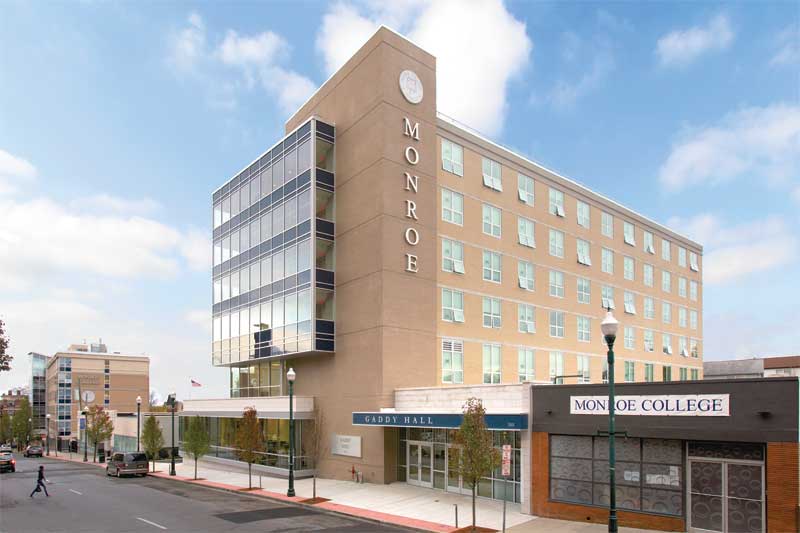
Choice of cladding and CI implications
Before choosing the CI solution, building teams generally select or recommend their cladding system. Aesthetics, performance needs, and suitability to
the application are among the drivers for choosing cladding. All things equal, are there types of cladding that make the most of CI? Possibly.
The reason for this is construction type, climate zone, and the building’s intended use would determine where the CI layer is placed in the enclosure assembly. Its location also affects construction sequencing and cost—that is to say, construction preferences may drive the choice of cladding so the CI layer is easy to apply, inspect, and, in some cases, to repair. When the CI insulation layer is outboard of the structural framing, for example, the detailing and construction tends to be much less complex than when it is interior to the structure, obviating such interruptions as floor slabs.
This leaves two typical options for CI location: behind the cladding or integral to it. Cladding options typically falling outboard of the CI layer include masonry and brick exteriors, as well as panelized metal systems such as aluminum composites, often used with mineral wool for the CI layer. As the CI materials must be supported, the façade attachment hardware can serve in some cases to secure both the cladding and the insulation; examples include clips, horizontal girts, and screws with sealing washers. Other types, such as impaling fasteners, are designed to support insulation alone.
Also located exterior to the CI layer are built-up façade cladding systems that require no penetrating fasteners to attach the insulation, further minimizing thermal bridging. Examples include traditional stucco and exterior insulation and finish system (EIFS) assemblies, which can use fully adhered insulation boards to offer good wind load resistance and protect against cracking caused by thermal expansion and contraction.
For many other cladding systems, the CI layer is integral. These can include precast concrete panels, tilt-up concrete walls, and masonry cavity walls such as brick veneer. XPS can be employed under various masonry veneer exterior finishes or over steel-stud framing, concrete, or masonry wall structures.
Similarly, CI is a feature of rainscreens and rain barrier claddings made with metal or aluminum composite panels, fiber-cement board, glass-fiber-reinforced concrete, or other materials. The chosen insulation must meet minimums for compressive strength and code requirements.
With many metal cladding systems and rainscreens, joint detailing can influence the selection of the CI material. Rainscreens with masonry veneer or open-joint panels are designed to admit moisture, which is then weeped or drained (or both), and dried through ventilation in the assembly’s cavity or air gap. If exposed to moisture, the CI material should be water-repellent. According to NFPA 285 testing, open joinery can expose the insulation to fire, so the CI material is chosen with adequate fire resistance in mind. In some cases, the open joints may also allow ultraviolet (UV) light from the sun past the cladding; therefore, exposed insulation and barrier materials should be rated for UV degradation.