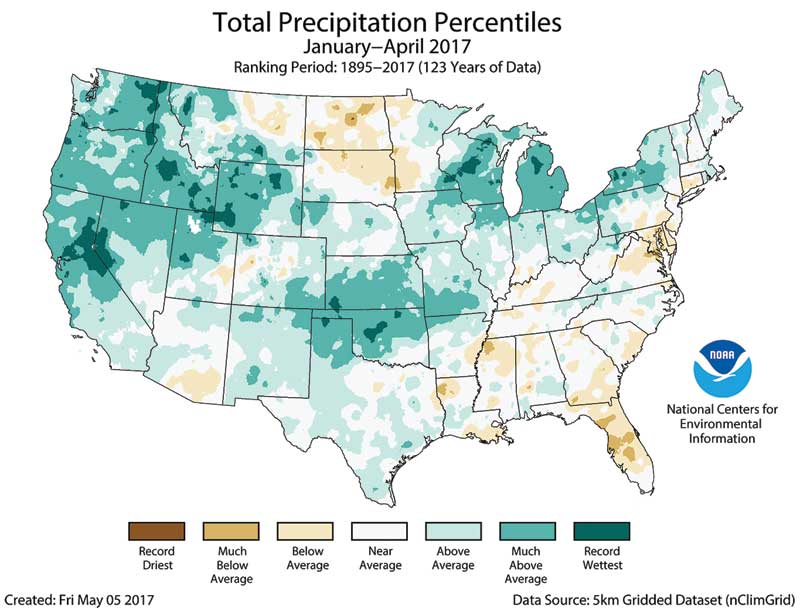
Evaluating WRBs
Plastic building wraps made of polyethylene or polypropylene fabric have been a popular method of protecting against moisture intrusion since the 1970s because of their durability and ease of installation. Since building assemblies have gotten tighter, building wraps have taken on a new function—helping to remove trapped water from the building enclosure. Their unique functionality enables them to both block moisture from the outside while also allowing walls to “breathe” to prevent vapor buildup. The latest innovations in building wrap technology are taking this moisture removal function one step further to incorporate drainage capabilities as well.
The 2018 International Building Code (IBC), Section 1402.2, “Weather Protection,” requires exterior walls “provide the building with a weather-resistant exterior wall envelope…designed and constructed in such a manner as to prevent the accumulation of water within the wall assembly by providing a water-resistive barrier behind the exterior veneer…and a means for draining water that enters the assembly to the exterior.”
This water-resistive barrier, as defined by Section 1403.2, “Weather Protection,” comprises at least “one layer of No. 15 asphalt felt, complying with ASTM D226, Standard Specification for Asphalt-Saturated Organic Felt Used in Roofing and Waterproofing, for Type 1 felt or other approved materials…attached to the studs or sheathing.”
It is important to note the difference between a weather-resistant barrier and a water-resistant barrier, as they have distinct purposes but are often confused with one another. The American Architectural Manufacturers Association (AAMA) defines WRBs as a surface or a wall responsible for preventing air and water infiltration to the building interior. The differentiating factor is a WRB must also prevent air infiltration, while water-resistant barriers are only responsible for stopping water intrusion.
WRBs are commonly specified for commercial buildings or projects where a higher level of performance is desired of the vertical building enclosure and when it is critical to have greater control of interior environmental conditions. Water-resistant barriers, on the other hand, are usually limited to residential and low-rise structures.
The International Code Council-Evaluation Service (ICC-ES) evaluates the following key performance characteristics for building wrap. These characteristics provide a valuable starting point for deciding which product best suits a specific project.
Water resistance
As its most basic function, a building wrap must hold out liquid water. A building wrap should be able to pass both “water ponding” tests, which measure a house wrap’s resistance to a pond of 25 mm (1 in.) water over two hours, and a more stringent hydrostatic pressure test where the wrap is subjected to a pressurized column of water for five hours.
Air resistance
According to the Air Barrier Association of America (ABAA), an air barrier is a system of assemblies within the building enclosure—designed, installed, and integrated in such a manner as to stop the uncontrolled flow of air into and out of the enclosure. Since an air barrier isolates the indoor environment, it plays a major role in the overall energy efficiency, comfort, and IAQ of a building. According to the U.S. Department of Energy (DOE), up to 40 percent of the energy used to heat and cool a building is due to uncontrolled air leakage. As such, the American National Standards Institute/American Society of Heating, Refrigerating and Air-Conditioning Engineers/Illuminating Engineering Society (ANSI/ASHRAE/IES) 90.1-2016, Energy Standard for Buildings Except Low-Rise Residential Buildings, and the International Energy Conservation Code (IECC) include air barrier requirements.
For an individual building material to be classified as an air barrier, its air permeance must be equal to or less than 0.02 L/(s-m2) @ 75 Pa when tested in accordance with ASTM E2178, Standard Test Method for Air Permeance of Building Materials. However, this air permeance test only measures the amount of air migrating through the material itself and not through holes or gaps in the larger assembly. Therefore, it is important to keep in mind a material’s effectiveness as an air barrier is largely dependent on proper installation and the use of compatible tapes, fasteners, and sealants.
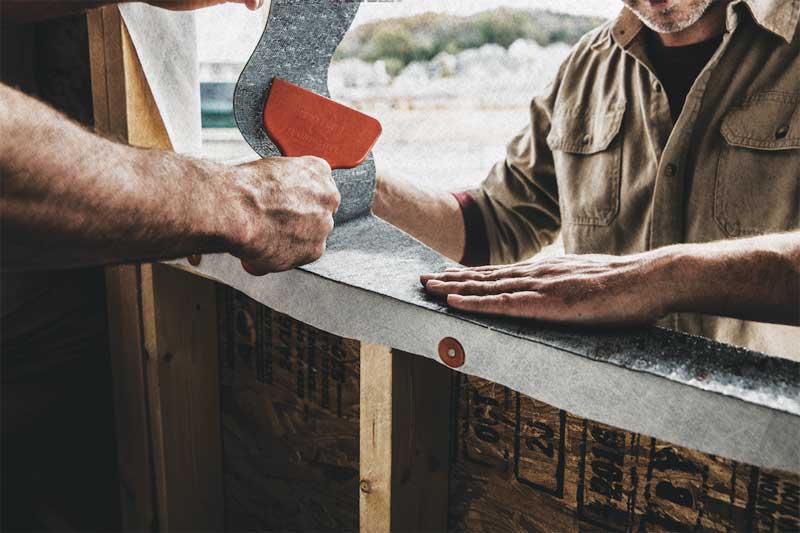
Durability
The ICC-ES looks at the tear resistance and tensile strength as the best measure of a building wrap’s durability, since it must be able to withstand the handling and application process without compromising its water resistance. Ultra violet- (UV) and low-temperature resistance are also important measures of durability because prolonged exposure to the elements can compromise the integrity of the product or cause it to crack.
Vapor permeability
For a product to be considered a building wrap and not a vapor retarder, ICC-ES mandates the permeance rating must be higher than 5 perms. However, permeability is achieved in a variety of ways, and as noted by Lstiburek, a higher perm rating does not always equal a better building wrap.
When selecting a building wrap, look for one that hits the “sweet spot” of 10 to 20 perms to achieve the desired balance of moisture protection and drying capacity. For example, some wraps have mechanical micro-perforations, which may allow the passage of more water vapor, but could also be more vulnerable to bulk water leakage. Generally, it is better to go with a higher quality, non-perforated or micro-porous product allowing for sufficient vapor mitigation while providing excellent resistance to bulk water.
Drainage
Drainage is widely accepted as one of the most effective measures for reducing moisture damage due to rain penetration. Drainage is a critical component in allowing a building wrap to do its job, particularly in keeping walls dry. Usually, this involves the use of furring strips separating the wrap from the structural sheathing and framing, but emerging technologies are helping to simplify this process.
Building wrap manufacturers have developed new products integrating drainage gaps into the material itself through creping, embossing, weaving, or filament spacers. These new technologies eliminate the need for furring strips as a capillary break, helping to reduce material costs and streamline installation.
These drainable building wraps meet all current standards for drainage efficiency (ASTM E2273) and are also vapor permeable, helping to address many of the moisture management issues described earlier.
Flammability
When designing wall assemblies, considerations should also be taken to ensure the wall system meets all applicable fire codes. The National Fire Protection (NFPA) 285, Standard Fire Test Method for Evaluation of Fire Propagation Characteristics of Exterior Non-Load-Bearing Wall Assemblies Containing Combustible Components, is the standardized procedure for fire testing of overall exterior wall assemblies when combustible materials, such as foam plastic continuous insulation (ci), panels, and water-resistive barriers, are components within the wall assembly. NFPA 285 is an assembly test, meaning all components of the wall system must be tested together. IBC, generally, requires NFPA 285 testing for exterior wall assemblies with combustible materials on buildings more than 12 m (40 ft) tall.
In addition to the NFPA 285 wall assembly test, relevant combustible components must also pass a series of material tests, per IBC. ASTM E84, Surface Burning Characteristics, comparatively measures product surface flame spread and smoke density. Products are then classified as A, B, or C based on their flame spread index, with Class A offering the lowest flame spread levels. It is important to note this test does not measure heat transmission, determine an assembly’s flame spread behavior, or classify a material as noncombustible. Specifiers should also request ICC-ES reporting data as part of their evaluation to ensure products meet the necessary standards.