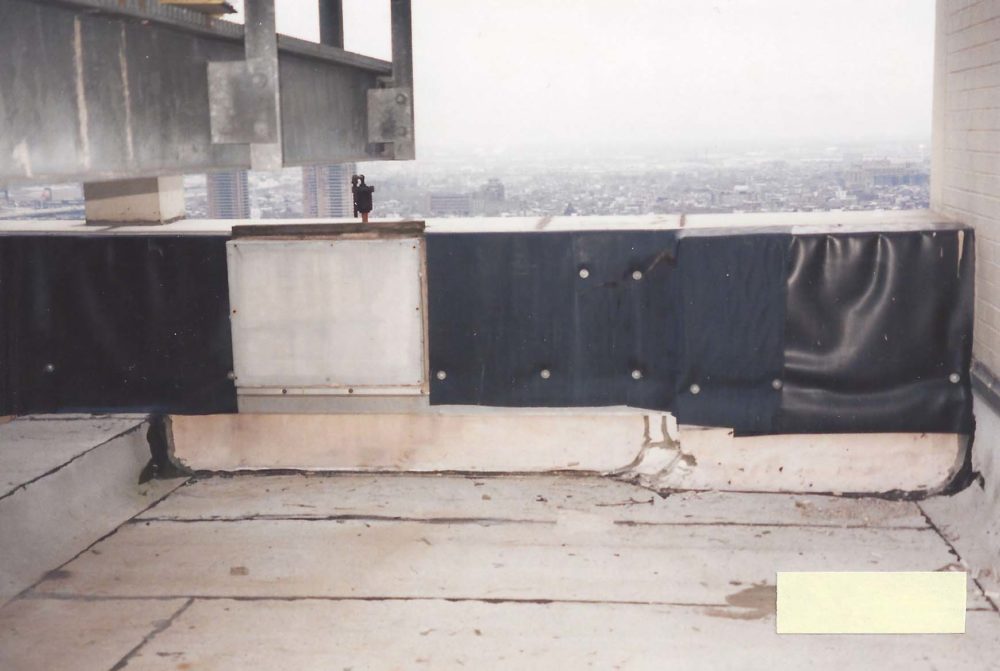
Installation requirements
Installation is just as important to the flashing systems as it is to follow all applicable building codes, safety programs, and the contract for construction. Careful supervision and diligent coordination between the contractor and the subcontractor is essential for proper installation of these flashings. Knowing and executing the appropriate sequencing of the moisture management system products is mandatory.
Installation of the specified products must follow the manufacturers’ installation guidelines for the materials being applied. The sheet metal flashing details are to be measured in the field so they are congruent with the as-built profile of the existing concrete masonry unit (CMU).
The performance of the water-resistive barrier (WRB) aids in keep the building dry. The through-wall flashing assemblies provide the means of egress and allow for any accumulated water to evacuate the weep cavity. End dams must also be installed at each end of the sheet metal flashing to prevent water from migrating outside of the confines of the newly installed flashings.
Benchmark milestones are put in place in order to document the integrity of the flashing assemblies. This documentation is required at each one of the six items listed below, which consist of the following individual elements installed in the order in which they are recorded:
- fully adhered EPDM field ply;
- sheet metal through-wall flashing receiver for the base flashing counterflashing;
- fully adhered EPDM flashing ply;
- high-quality permeable WRB;
- weep tubes installed underneath the setting bed of mortar for the first course of brickwork; and
- drainage plane with a shiplapped fabric that is extended over the back edge of the weep tubes.
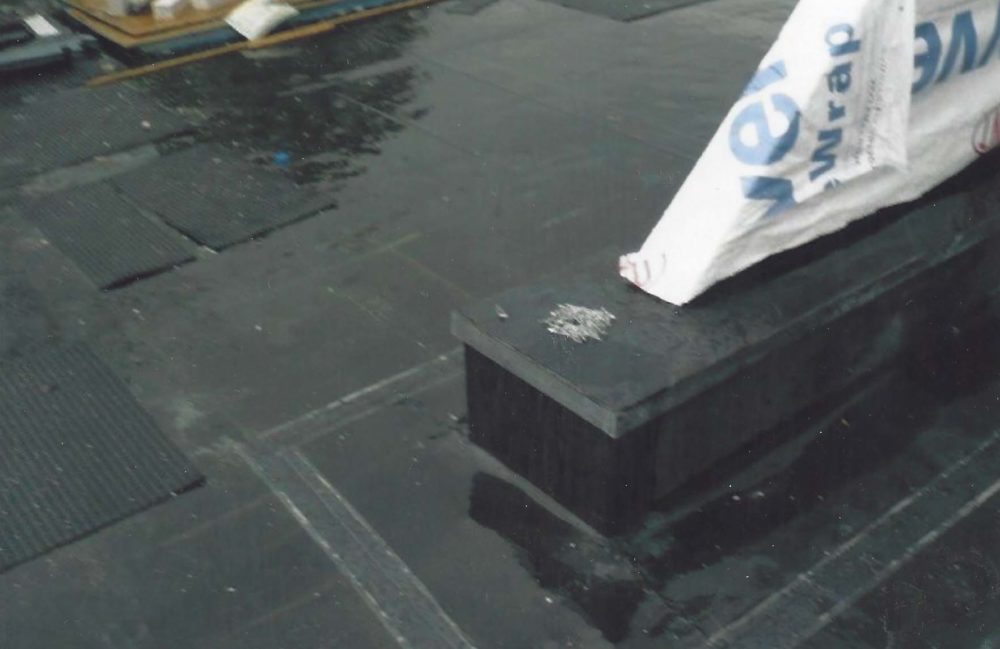
The flashings must be fully adhered and secured to the backup wall with appropriate fasteners. In this example, the flashings are what allows for the accumulated moisture to drain out of the weep cavity. These flashings must be inspected prior to any masonry material being extended over them. This is done to document the integrity of the of the installed through-wall flashing system assemblies, step by step.
Each element must be adhered and fastened to the backup wall with approved fasteners. Those assemblies must then be covered over with a high-quality, permeable WRB, which is shingled into place starting from the top of the CMU base platform, and working from the low point to the high point of the parapet and/or the rising wall.
The installation calls for all lapped seams to be horizontal, and taped using the tape manufactured specifically by the WRB producer. The water-resistive barrier gets fitted to the contour of all exposed areas of the rising/parapet wall sheathing. This material is then fastened with the approved fasteners following fastener density protocol. The drainage plane system then gets installed, covering all exposed areas of the WRB.
Each of the previously mentioned benchmark milestones in the process of construction requires photographic and written accounts that must be documented by the consultant or an independent quality assurance (QA) observer. This document must be distributed to all parties on the same day the report is prepared.
Another choice is to use Fluid Applied Reinforced Flashing like Kemper System 2K-PUR. It is self terminating, and odor free, and provides long term performance.
Steve-You are correct thart there are several choices to make in order to achieve the objective of providing a means to empty the cavity. However, in my experience there are too may holidays and openings in the wall sheathing material that a fluid applied product could not span. therefore in this example it is not the preferred method. Thank you for your inquiry.
Excellent, I am concerned about the concrete bleeding interface with Aluminum window framing and salt spray ocean environment. Even protected and painted metal roofs lose their finish in less than 15 years. Have you seen any association recommendations?