The next method, performance, may be increasing in popularity as additional strategies are employed to reduce thermal leakage throughout the assembly. In the performance method, a wall is modeled, and a U-factor is calculated referencing the overall conductivity of a wall assembly. This may take further measures such as thermally broken fasteners into account. Finally, compliance can be proven through a checklist software which considers performance assigned to specific assembly design types.
It should also be noted, while code compliance is the first step in addressing thermal performance, many voluntary or even compulsory codes and standards may be used to supersede or complement these requirements. These comprise standards such as ASHRAE 189.1, which includes commissioning among other criteria like higher air leakage requirements, or approaches such as Passive House as a strategy to reach net-zero or net-zero-ready building performance. As these approaches are implemented, the most significant performance strategies, such as specifying continuous insulation, become a baseline for more fine-tuned approaches to managing thermal performance. Addressing details like thermal bridging and heat recovery valves becomes critical to reaching the last bit of reduction in energy usage.
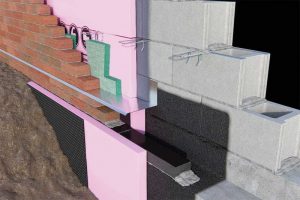
Insulating masonry cavity walls
The fact many insulation types may be used in masonry veneer assemblies may be one reason for the robust design’s continued popularity. The most common insulating material is perhaps a rigid board insulation such as extruded polystyrene, expanded polystyrene, or polyisocyanurate. These materials come in regular dimensions and are cut to fit in the application. Joints are not necessarily required to be sealed, but simply tightly butted. However, specifiers should verify with the manufacturer of choice, as sealing may be required if the material is also to act as the air and weather barrier. If a material is strong enough, it may be simply compression fit between masonry ties attached from the masonry veneer into the structure behind, or it may be attached using mechanical fasteners through the insulation into the structure beneath. Adhesives may also be used with this insulation type. Among other requirements, specifiers should be cautious to verify the adhesive is compatible with both insulation and surrounding materials, such as air barriers; the insulation is resistant to moisture, as the cavity will be a location of moisture presence; any fire performance requirements are tested or listed; and the R-value is reliable in anticipated climate situations.
Semi-rigid mineral wool insulations have also become more common in masonry veneer wall applications. They are most likely to be secured through compression fit between masonry ties or mechanical fasteners. Specifiers should verify moisture resistance of this special group of mineral wool, but the flexibility of the material may be advantageous for specific shapes such as curves.
Another option is spray polyurethane foam (SPF) insulation. This product is applied by combining a polyol and an isocyanate at a specific temperature directly to the substrate. Specifiers should verify moisture resistance (closed-cell versus open-cell) and climate for appropriate conditions at the jobsite and maintain the minimum cavity thickness for drainage and air circulation.
What are thermal bridges and where do they occur in the wall?
With all the effort to design and install more energy-efficient masonry walls, more focus is being placed on transitions to address thermal bridges which could impact or even negate increased insulating efforts. Many buildings designed to be more efficient see a disconnect or performance gap between how they were intended to perform and their actual energy performance.