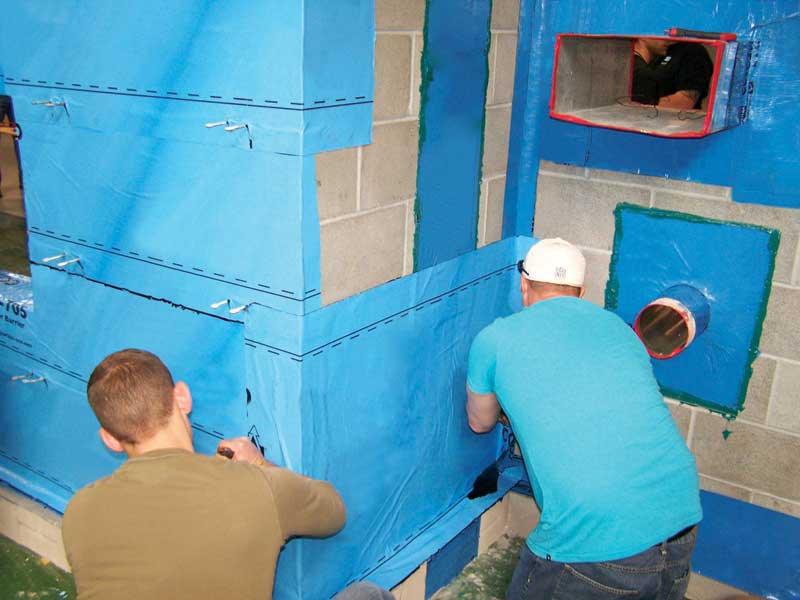
Air barriers
Air barriers restrict air flow in and out of the wall and minimize energy loss and condensation from moist leaking air. By controlling moisture, they reduce or prevent mold growth and corrosion while improving the building’s overall occupant comfort, building life, and energy-efficiency. The Air Barrier Association of America (ABAA) estimates the use of an air barrier reduces cooling costs by 10 to 15 percent, and heating costs by 30 to 40 percent.
Some air barriers also act as WRBs, providing a water-resistant envelope, preventing accumulation of water in the building, and establishing a drainage plane inside the wall. The specifying architect must decide whether the WRB is sheet-applied, fluid-applied, rolled-on, or sprayed, and whether it is permeable or impermeable. Among the popular choices are acrylic air and water-resistive barriers, which are very flexible and able to tolerate building movement. They are fluid-applied and permeable, so they permit limited vapor to pass through, which allows drying and provides ‘forgiveness’ against moisture accumulation in the wall—all while keeping liquid water out (Figure 1).
Insulation
In masonry veneer walls with wood or steel stud structural backup, batt insulation is normally specified in the stud cavity. However, since the stud framing creates a ‘thermal short’ through the cavity insulation layer (as much as 50 percent through steel studs), the batt insulation value is often effectively cut in half. Therefore, continuous insulation is routinely added to the cavity in cavity walls and behind the lath in adhered masonry walls to conform to energy codes. When properly installed using thermal break fasteners, ci minimizes thermal bridging so heat transfer is dramatically reduced.
Water inevitably gets into the air space in cavity walls and behind the lath in adhered masonry walls. Therefore, ci in the cavity or behind the lath should be highly water-resistant. The Brick Industry Association (BIA) in Tech Note 28-B, Brick Veneer/Steel Stud Walls recommends the use of water-resistant, closed-cell, rigid foam insulation sheathing to prevent water from penetrating into the sheathing. Its chemistry and manufacturing process causes extruded polystyrene (XPS) to be inherently water-resistant, and it does not rely on facers for water resistance. Facers are easily damaged on site so they cannot be relied on to keep water out.
Sprayed polyurethane foam (SPF) is sometimes used in stud cavities or as ci. Sprayfoam has the advantage of being able to seal small cracks to limit air movement, but it requires careful control of in-field installation conditions to achieve the necessary insulating properties. Additionally, the application temperature, nozzle pressure, and rate of the applicator wand speed must be precise, and the installer must be very careful to use proper personal protection and overspray control.
When considering other insulation materials water penetration, impact on thermal properties, fire resistance, and impact of site conditions on the performance of the product should be examined. XPS is a factory-made board product—meaning its insulating properties are quality controlled in the factory, and proper installation is not as dependent onsite conditions as sprayfoam. It is important to note air barriers, extruded polystyrene ci, and other components, must be specified as parts of the National Fire Protection Agency (NFPA) 285, Standard Fire Test Method for Evaluation of Fire Propagation Characteristics of Exterior Non-load-bearing Wall Assemblies Containing Combustible Components. NFPA 285, which verifies limited fire propagation potential in exterior, multi-story wall systems, is often required by the International Building Code (IBC) for Types I, II, III, and IV construction.
The architect must also consider the installation method for ci. With board products, corrosion-resistant, ceramic-coated screws with air-and-water sealing washers offer long life and limit air movement and energy loss. Sealing washers are available with prongs that insert into the foam to enable the contractor to be more efficient by pre-spotting washer locations. The washers must be large enough to distribute the stress of pulling the water-resistant XPS insulation tight against the air barrier/sheathing to effectively seal the screw penetrations. Small details like this can make a big difference in how the wall assembly performs and should be part of the specification.
Moisture vapor retarders
Placement of a vapor retarder depends on several factors. Vapor generally flows from high pressure to low vapor pressure—high pressure being warm air that holds more moisture, compared to cool air that holds less moisture. In northern climates, the vapor retarder typically goes on the ‘warm-in-winter’ side or inside, while in the South, it goes on the outside.
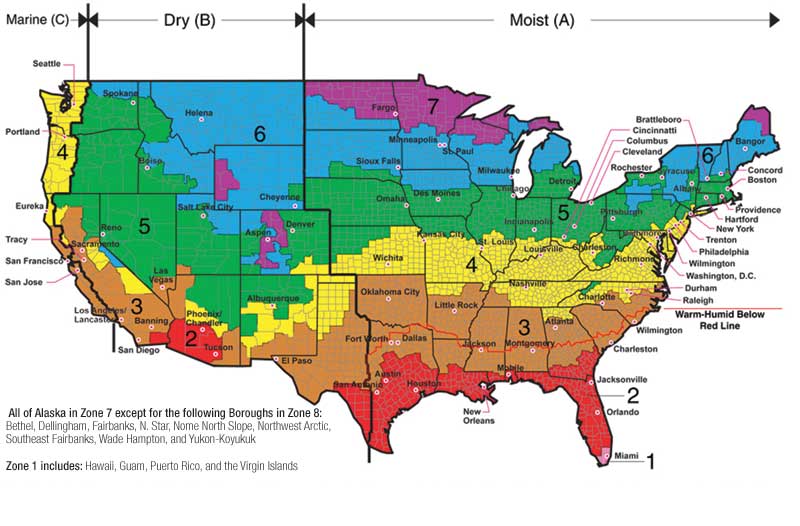
In the middle section of North America, there is more flexibility on the necessity, location, and level of permeance of a vapor retarder. However, in all climate zones, placement depends on the environment, the wall construction, and the permeance (‘perm’) of the vapor retarder. Whether a vapor retarding layer should be high-or-low perm depends on variables such as:
- typical vapor pressure difference;
- how long that vapor pressure difference persists;
- boundary conditions such as typical wetting/drying and solar heating of surfaces cycles; and
- the hygrothermal characteristics of the various material layers in the wall.
Current practice utilizes modeling software such as WUFI to make detailed hourly simulations of moisture migration and accumulation over multiple annual cycles to assess designs and predict performance. All building materials like gypsum board or brick absorb water, hold it, and then release it as conditions change. WUFI analysis takes those dynamic characteristics into consideration. Section 1405.3 of the IBC provides guidance on the use of vapor retarders in different climate zones (Figure 2).
When vapor-retarding facers are a part of the stud cavity insulation, its flame spread rating must also be considered. In Types 1 and 2 construction, facer flame spread must be less than 25. In Types 3, 4, or 5 construction, facer flame spread may be above 25.
It’s good to see masonry making a comeback in the residential construction scene. Although the use of lumber will never really disappear, I think that the demand will change. I will have to do some more research on insulations for concrete and masonry buildings.
Great explanation here of masonry wall systems and their benefits. It’s nice to know how one should be handling a job like that.