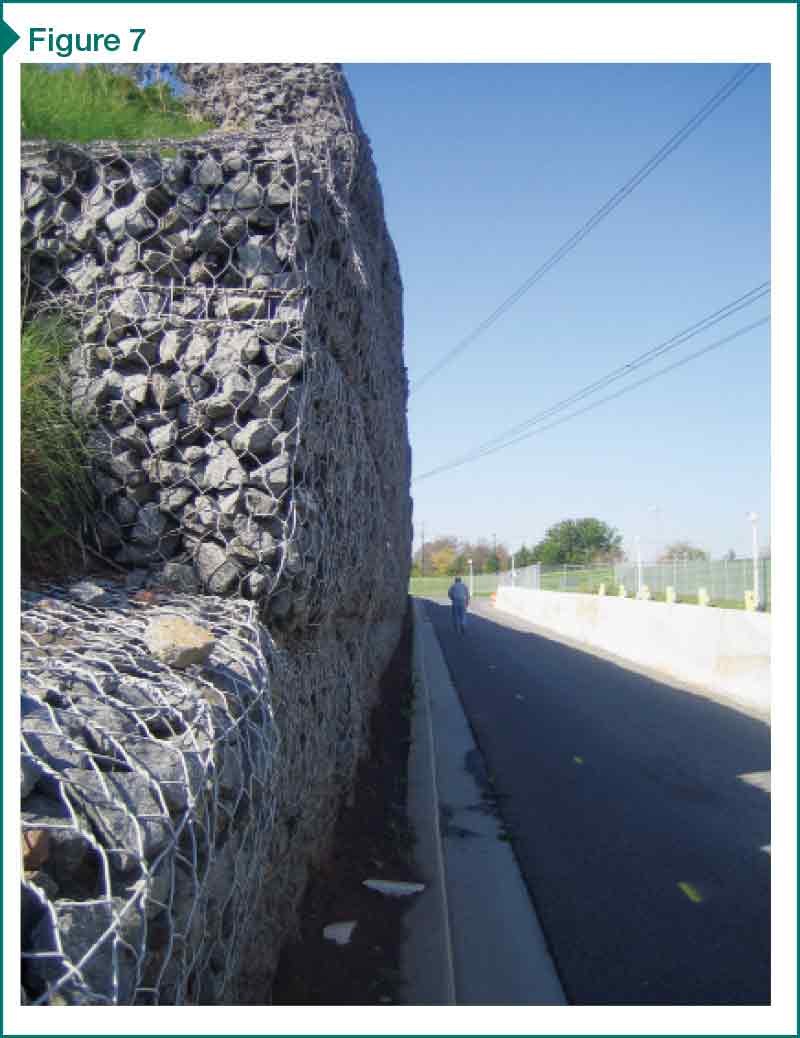
Wall movement
MSE walls are flexible structures that move laterally, primarily during construction. In some cases, walls are designed with a vertical face, without a batter, to maximize the useful property at the top of the wall. However, once the wall undergoes movement, even if the wall is technically stable, the wall appears unstable because the top of the wall overhangs the bottom (Figure 7). Walls should be designed with inward batter to avoid such a perceived failure.
Construction observation
Due to the various parties involved with the wall design, it is important appropriate parties perform construction observation. A qualified geotechnical engineer, familiar with the design and site conditions, should observe wall construction to verify compliance with the plans and specifications. The wall designer, and any other party assuming responsibility for stability checks, should be made aware of soil conditions (naturally occurring at the site and backfill) to verify compliance with the design intent.
Why are these issues important to contractors?
Growth in the use of MSE walls has resulted in a significant number of performance and stability failures. (For examples see R.M. Koerner and G.R. Koerner’s 2011 article, “The Importance of Drainage Control for Geosynthetic Reinforced Mechanically Stabilized Earth Walls,” in Journal of GeoEngineering [vol. 6, no. 1].) Costly repairs and/or disputes often follow. These disputes, whether legitimate or not, commonly involve all project team members, regardless of whether the issues are design- or construction-related. It is beneficial for all project team members, including both the civil and wall contractors, to be proactive and to discuss the issues previously listed during the preconstruction and construction stages. Increased project communication will assist in avoiding potential costly repairs and disputes.
The contractor’s contractual responsibility depends, of course, on the contract language. While contractual arrangements vary between projects, based on two common project delivery methods, a contractor can implement the following approaches in order to improve the chances of a successful project:
- For projects where the owner’s engineer designs the wall, the contractor can submit requests for information (RFIs), and initiate discussions during the bid, preconstruction, and construction stages of the project.
- For projects where the contractor designs the wall, he or she can self-perform the design or hire a subcontractor to perform the work. For these projects, the contractor can proactively discuss important issues with the designer, including civil site improvements, drainage requirements, and responsibility for stability checks.
Even in a scenario where all parties are aware of their roles and responsibilities, the contractor can work closely with the project team during all stages of the construction.
Recommendations
Based on the authors’ experience, regardless of the project delivery method, contractors have the ability and opportunity to take a proactive role before and during the construction of a mechanically stabilized earth wall to mitigate potential problems. The steps outlined below could be beyond the contractor’s responsibility as interpreted from contract requirements. Nevertheless, they are often a good investment given the potential consequences.
Prior to construction:
- review contract documents and verify the wall design includes all the necessary drainage elements defined in the aforementioned NCMA manual and FHWA publication;
- verify that the MSE wall stability and performance checks have been performed and documented by a competent, responsible party;
- submit RFIs during the bid process and preconstruction for clarification on coordination or the interrelationship between the wall and civil site improvements; and
- request a preconstruction meeting with the geotechnical engineer, wall designer, owner’s quality assurance engineer, civil site engineer, landscape designer, and owner to review the drawings and specifications, discuss the construction requirements, and understand the interrelationship between the wall, soils, utilities, reinforcement, penetrations, site grading, and other elements adjacent to the wall.
During construction:
- make field observations to verify design assumptions are consistent with in-situ conditions and to identify any unanticipated conditions;
- be aware of other site construction activities (e.g. utility installation or surcharges on top of wall, etc.) that may impact wall performance;
- verify the owner’s quality assurance (QA) engineer is regularly submitting field reports and performing testing in accordance with project specifications;
- coordinate and attend periodic project meetings to encourage communication among the project team, clarify project requirements, and address unanticipated conditions or issues; and
- document the construction process by preparing complete submittals, filing RFIs, taking site photos, preparing field reports, and recording meeting minutes.
With a proactive approach to construction involving all parties, contractors can put themselves in a position to effectively mitigate risk the project team may not have considered, reducing the potential for costly failures.
Bryan P. Strohman, PE, is a Senior Staff II–Structures at Simpson Gumpertz & Heger (SGH). He is a geotechnical engineer with seven years of experience working on projects involving investigation and rehabilitation of buried structures. Strohman can be contacted via e-mail at bpstrohman@sgh.com.
Scott J. DiFiore, PE, is an associate principal at SGH. He is a structural and geotechnical engineer who has almost 20 years of experience designing, investigating, and rehabilitating a variety of structures. DiFiore has specialized expertise in underground construction, including retaining walls, earth support systems, foundations, and underpinning. He can be reached at sjdifiore@sgh.com.