by Brad Davison-Rippey, AIA
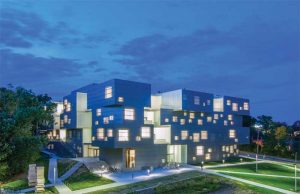
During the last decade, the construction industry has seen an evolution of finishes and applications. This has changed the way metal panels are being designed—they are no longer viewed just as a durable means to enclose a building. This change in perception can be seen in the adoption of a complex metal rainscreen system comprising interlacing patterns to form beautiful, complex façades.
In June 2008, the University of Iowa experienced massive flooding throughout the campus, which destroyed or heavily damaged many buildings. The original arts building from 1936 was one of the affected structures, along with a handful of others along the banks of the Iowa River. The building experienced severe water damage. Therefore, the university decided to invest in a new facility for visual arts. The school partnered with Steven Holl Architects (SHA) to design the new structure at a new, higher location directly adjacent to the Art Building West SHA had worked on a few years prior.
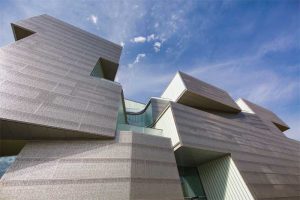
Photo © Angela Sleep Photography
Though this new building would complete the second half of the so-called art quad on campus, Steven Holl and his team set out to incorporate maximum interaction between all departments of the school—not just art—by creating open, social spaces to spark conversation and creativity.
With this intent in mind, light became a focus early in the design process. The use of light would create a dynamic space able to stimulate those who pass through or walk by. After entertaining more than 30 design schemes for the new structure, the project team finally landed on a square-shaped building carved out for brightness with light courts (terraces) and skylights. All five stories of the facility reside on different planes, shifting in harmony with one another and creating movement within the square footprint. Each of the building’s seven
cuts of light can be seen throughout the space, from the furniture and door handles to perforated stainless steel panels on the southwest and southeast elevations of the building.
The façade was designed to ensure the proper amount of light flows into and out of the structure. This proved to be a critical factor in the building’s construction and successful project execution, as it was designed around the multiple centers of light, both inside and out.
Customized panels
Instead of using traditional, full cutouts for window openings, the design called for two of the elevations to be completely wrapped in perforated metal panels passing over the building’s windows to create a dancing light effect as the sun moves throughout the day. The metal panels not only allow light in, but also give the façade texture and depth.
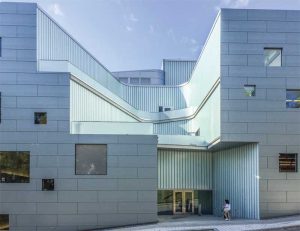
Photo © Eric Dean
The double-skinned wall system also included a zinc cladding located 178 mm (7 in.) behind the perforated stainless steel panels on the south and west elevations. The 1.5-mm (59-mil) zinc cladding was custom designed. The stainless steel wall panels were 5 mm (3/16 in.) thick to accommodate the nearly 13,000 holes in each one. The 16 different shapes for these perforations were derived from the seven cuts of light and skylight.
Installation
Behind the prefabricated rainscreen system, 152 mm (6 in.) of mineral wool insulation and fluid-applied air barrier were installed over the poured-in-place concrete structure. The metal panel system was attached using vertical tracks, strategically placed to accommodate the window placement. Also building information modeling (BIM) was used to finalize the coordination of the panels and their layout across windows. As the metal panels were 5 m (16 ft) wide and 1 m (3.4 ft) tall, the field crew had to set them by crane. Craftspeople onsite were attentive to the vertical track layout during installation, as the layout was critically important for the panels to interface with the windows and terraces.
Another important component was aligning the perforations from one metal panel to the next. The pattern repeats across the face of the wall and aligns on the returns at the top and bottom of each panel. To achieve the precision necessary for this alignment, individual computer-aided design (CAD) files were created for each panel and studied in depth. Custom solutions, such as the deflection support bracket and the panel key in front of the large windows, were employed during installation to maintain the integrity of the aesthetics envisioned by the design team.