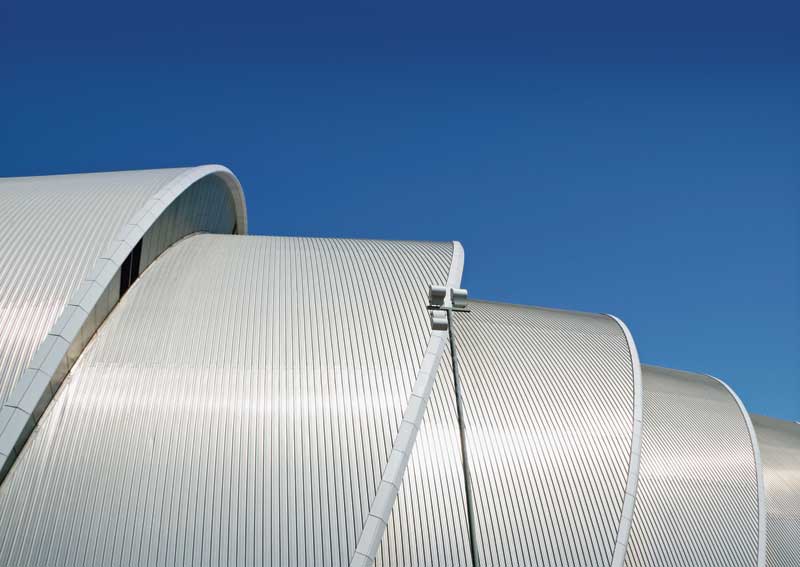
by Robert M. Haddock, CSI
Economic reasons make carbon sheet steel popular for metal roofing, but the material can corrode when exposed to both oxygen and moisture. For this reason, steel typically has a coating, but the protective role differs among products.
Some provide a ‘barrier,’ creating a thin, impermeable film that prevents air and water from reaching the steel substrate. Others are ‘zinc-rich’ and provide ‘sacrificial’ protection—an electrochemical phenomenon protecting the base metal at the expense of the coating metal.
The continuous hot-dip process
Metal coatings are normally applied to the steel coil at the producing mill using a process called ‘continuous hot dipping’. In the first stages of the process, the steel is cleaned, degreased, rinsed, and forced-air dried. It is also ‘pickled’ in an acid bath, and preheated. At this point, the material’s mechanical properties can be affected—if desired—by exacting control of high temperatures, pressure, and cooling.
The coil then passes through a bath of molten metal at temperatures that provide for a metallurgical bond between base steel and coating metal. Ranging between 426 and 593 C (800 and 1100 F), the exact temperature varies with the coating type, since different coatings have different melting temperatures. The metallurgical bond between coating and base steel substrate causes monolithic behavior of the material during fabrication and service.
The coating thickness is controlled in most mills with ‘air knives’—sophisticated pneumatic squeegees that interface with the surface of the coil as it emerges from the bath of molten metal. The material is cooled and the coating solidifies on exit from the bath and entrance to the cooling tower. This process is closely controlled to affect varying surface appearance characteristics. It is during this process that the ‘spangle’—the metal flake appearance in the finish—of zinc-rich coatings is sometimes altered (i.e. minimized). Finally, the material is water-quenched, dried, and recoiled at the end of the line.
Most often just prior to recoiling, a chemical, passivation, or oil treatment (or combination thereof) is applied to extend the material’s shelf life, prevent storage staining, and/or prepare it for the next step of production—whether this means painting or fabrication. The oils help lubricate during the roll-forming process and provide some shelf life. These materials evaporate soon after installation.
The continuous hot-dip process takes place at line speeds of about 244 linear meters (800 linear feet) per minute, translating to as much as 446 m2 (4800 sf) per minute, making it a cost-effective method to apply metallic coatings.
Zinc coatings
Perhaps the best-known coating for carbon steel sheet is commercially pure zinc, commonly known as ‘galvanized.’ (It bears mentioning here that galvanized iron [GI], despite being commonly designated on architectural plans, is a product that has been obsolete for decades.)
Common coating application rates for galvanized steel are 0.30, 0.60, and 0.90 oz per sf, designated as G-30, G-60, and G-90, respectively. Long ago, the target application rate for G-90 was 35.4 g (1.25 oz), with 0.90 serving as the minimum requirement. Sophisticated modern application equipment has enabled producers to maintain much more consistent and uniform application thickness, so the target rate of 35.4 g has gone by the wayside. Target application weight now is much closer to the minimum and verified by testing using either a single- or triple-spot sample according to ASTM International procedures.
It is important users understand zinc application coating rates because they have a linear relationship with the roof’s performance and longevity. For example, with other factors being equal, G-30 has a third the life of G-90; consequently, it should not be used for exterior claddings. G-60 is used only in cost-cutting applications and G-90 is the common choice for commercial steel roofing in pre-painted applications.
The total coating thickness of both sides of G-90 is 38.4 µm (1.51 mils). At the target application rate, this means coating thickness on a single side is about 19 µm (0.75 mils). However, due to coating process tolerances, industry standards allow the minimum on one side to be as low as 40 percent of the total, so the thickness on one side could be 15 µm (0.6 mils).
Excellent article Rob.