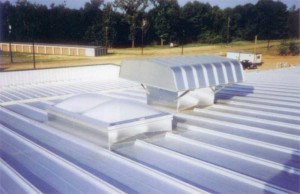
Photo courtesy Metal Roof Advisory Group
Due to the slim coating thickness, zinc and zinc-alloy coatings also rely on the galvanic protection at scratches and cut edges. In the presence of an electrolyte (e.g. water), zinc’s active or anodic behavior retards oxidation of the steel substrate. For the same reason, zinc bars are attached to steel-hull ships and often inserted into domestic hot-water tanks—they slow steel’s corrosion.
Zinc coating is preferred by some manufacturers due to its excellent flexibility (i.e. malleability) in fabrication, especially when sharp radius bends are required in the product. Another advantage of using galvanized steel
is its solderability.
Although technically any coating (including zinc) offers barrier protection, zinc is generally referred to as a sacrificial coating because its electrolytic behavior is somewhat unique. By design, the coating goes away over time, sacrificing itself to retard the steel’s corrosion. Its life, then, is directly proportional to its thickness and the elements to which it is exposed. This galvanic activity is a desirable characteristic with respect to the corrosion behavior of steel, especially at surface scratches and cut edges where the base steel is exposed and unprotected by a barrier.
In unpainted applications, galvanized steel has become outdated as it has been replaced by newer technology coatings that significantly outperform it in such instances. Nevertheless, it is still considered an acceptable coating and is preferred by many when a premium organic finish (paint) is used. Although the paint is not impervious to moisture, it retards the galvanic process, prolonging the life of the galvanized substrate. However, due to the hindered galvanic process, corrosion performance at scratches, cut edges, and severe outside-radius bends is somewhat diminished.
Galvanized steel is produced by many mills and is widely available. It is not typically warranted by the producing mills for corrosion performance. Due to galvanic behavior and the natural oxidation process, the zinc diminishes over time. When a substantial volume is gone, the base steel is exposed and the corrosion protection—barrier or sacrificial—is no longer afforded.
This service life varies in different environments. The galvanic process occurs only when an electrolyte is present (i.e. when the surface is wet), so service life is longer in dry climates and at steeper slopes that keep surface moisture well drained. Hence, duration of wetness on the panels’ surface has more to do with service life than rainfall intensity or frequency.
In dry, desert-like climates where roofs seldom dew at night, bare G-90 may perform well for 50 or 60 years. In more humid climates, this is not the case; the roof will reach dewpoint almost every night, it is wet for a third of its lifetime, notwithstanding rainfall.
The aggression of the moisture also affects the life of the galvanized material—drastically reducing it in salt-spray or acid-rain environments. This is because such contaminants make for a much more effective electrolyte, accelerating the galvanic process. Once the coating is depleted, the steel roof need not be replaced, but it is a candidate for a field-applied coating to extend its useful life. However, no known field-applied coating has the same life or performance expectancy as the original metallic one.
Zinc coatings are typified by a broad spangle appearance caused by trace lead or antimony content. The size of the spangle can be controlled or eliminated altogether by the producing mill. In general, minimized spangle is preferred when the material is to be painted.
Spec references for galvanized include:
- Federal Spec QQS-775d;
- ASTM A 924, General Requirements for Steel Sheet Metallic Coated by the Hot-dip Process; and
- ASTM A 653, Standard Specification for Steel Sheet, Zinc-coated (Galvanized) or Zinc-Iron Alloy-coated (Galvannealed) by the Hot-dip Process.
The ASTM reference number is normally followed by steel grade (e.g. “A653 Structural Quality Grade 50”).
The same ASTM spec references are also used for ‘Galvannealed,’ which is a special zinc-iron alloy coating. Other zinc coating treatments, sometimes tailored to specific field-painting applications, are known by various trade names.
Aluminum coating
The application of commercially pure aluminum to steel sheet is a process developed by Armco Steel Inc., and is known by the trade names ‘Aluminized Type I’ or ‘Aluminized Type II.’ The former is typically only used in the automotive industry, while the latter is commonly employed for exterior claddings in coating weight of 18 g (0.65 oz), resulting in a thickness of
62 µm (2.43 mils), total for both sides. Note that although the coating weight is less than zinc (G-90), the resulting thickness is significantly greater, due to the lighter weight of aluminum. It is also available in other coating weights.
As opposed to zinc’s sacrificial nature, aluminum coating offers barrier-type protection. Aluminum oxides are extremely durable and the 0.65-oz coating application, which is designated T2-65, carries a limited 20-year warranty against panel perforation due to normal atmospheric corrosion. (This is a limited material-only warranty underwritten by the mill and normally ‘flows through’ the panel fabrication process, passing on to the end user when specifically requested.) Twenty-year exposure testing of the product has shown it far outlives (and even doubles) the warranted life in most environments.
Although Aluminized does not have the sacrificial protection of zinc, scratch and cut-edge performance is reasonably good. Corrosion seems to progress slowly from such areas because of the durability of the aluminum oxides. Aluminized steel has been used in both painted and unpainted applications, but as the coating is more brittle than zinc, restrictions on sharp bends in fabrication are more stringent. This type of coating is applied by the same hot-dip process, but at slightly higher temperatures.
Having a matte finish without spangle, Aluminized is a good choice for bare applications, or the material can be pre-painted. It generally outperforms most of the other popular coatings in salt or acid environments, although its warranty may exclude a 20-year performance in those situations. Aluminized material has decreased in relative market share in the last two decades because it has not been as actively and aggressively marketed as other coatings have been. However, it is still quite popular within the automotive industry.
Spec references include:
- Federal Spec S-4174 B; and
- ASTM A 463, Standard Specification for Steel Sheet, Aluminum-coated by the Hot-dip Process.
Excellent article Rob.