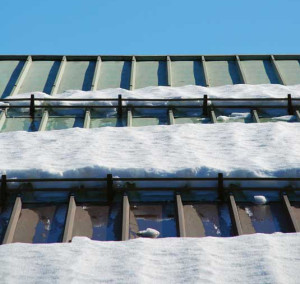
Photos © Dreamstime.com
Aluminum/zinc coatings
Although several aluminum-zinc (AlZn) formulations are used worldwide, the most popular alloy coating domestically is known by its trademarked name, ‘Galvalume.’ This alloy is 55 percent aluminum, 43.4 percent zinc, and about 1.6 percent silicon (by weight). Measured by volume, the coating is approximately 80 percent aluminum.
Developed by Bethlehem Steel, it was made commercially available in the late 1960s. It has since been licensed by BIEC International Inc. (formerly Bethlehem International Engineering Corporation) to 40 or more producers worldwide, several of which are North American companies. It is much more popular here in the United States and in Asia-Pacific (due to strong marketing by the Australian producer) than elsewhere. The product is known by various trade names including Zincalume, Aluzinc, and ZintroAlum.
This AlZn coating blends the barrier protection of aluminum and its oxide durability with the sacrificial properties of zinc, resulting in a synergistic alloy that has superior weathering properties when compared to galvanized, yet maintains the galvanic corrosion protection of zinc at scratches, cut edges, and severe-radius bends. Its cost premium over pure zinc coating is negligible, but performance characteristics are far superior in unpainted applications—hence it has forced bare galvanized into near-obsolescence in commercial applications.
Galvalume is used in various application weights, including 0.50, 0.55, and 0.60 oz. per sf (total both sides). These weights are designated AZ50, AZ55, and AZ60, respectively. The AZ55 coating is the most widely used and is warranted by most domestic producers for 20 years. Its thickness (both sides) is 45 µm (1.76 mils). The warranty is generally an assurance the panel will not perforate (in a ‘normal’ environment) due to corrosion.
Field studies after 25 years of exposure find actual performance of this material far exceeds its warranted performance. In a ‘friendly’ environment, it can be expected to render service life double or even triple that of its conservative warranty. For this reason, some domestic producers are now extending the warranty on AZ55 and painted AZ50 to longer terms.
Galvalume is the leader of coated steel options in unpainted applications. The market trend is also in preference of the AlZn coating as a painted substrate, but galvanized still enjoys significant market share. Due to the fact paint slows down the galvanic process, corrosion performance of Galvalume at scratches and cut edges may not be as good on painted applications as on unpainted ones in the initial years of service Many prefer the galvanized substrate for this reason. However, it has been demonstrated over subsequent years of service, ‘edge-creep’ performance—corrosion that works its way in from a cut edge—is often better with Galvalume than with G-90.
While Galvalume inherits the strengths of both its alloy coating metals, it also takes on their respective weaknesses. Contact with both acids and alkalis should be avoided. Since the coating also tends to retain cosmetic stains such as footprints and handprints, some producers now provide a thin application (about 7.6 µm [0.3 mils]) of acrylic coating to afford temporary stain protection during handling and installation. The coating weathers away after a few years. This option, dubbed ‘Acrylume’ or ‘GalvalumePlus,’ depending on the producer, is used only for unpainted applications and is becoming more popular, as it also has other production and storage-related advantages.
Galvalume-coated steel must be installed to promote free drainage, and is often employed at slopes as low as ¼:12, which is the warranty limitation. Despite its 40-year history and tens of billions of square feet of trouble-free installations at the requisite minimum slope, some specifications and standards mandate ½:12, most notably the National Roofing Contractors Association (NRCA).
Such a requirement is without substantive foundation from a material performance standpoint. The material likes to be able to breathe and air-dry and ¼:12 is deemed (and warranted) by its producers to be adequate for that purpose. Adjacent materials or details that could allow moisture to become trapped against the panel surface should be avoided. Any rooftop appurtenance should be mounted above the drainage plane of the profile. In simple terms: assure drainage of this material and job done.
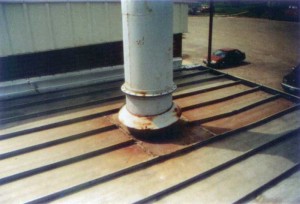
Photo courtesy Metal Roof Advisory Group
Spec references include:
- Federal Spec Army Corps of Engineers Guide Specification (CEGS)-07413;
- Army CEGS-07415;
- Army CEGS-13120;
- Naval Facilities Guide Specification (NFGS)-13121;
- ASTM A 924, General Requirements for Steel Sheet Metallic Coated by the Hot-dip Process; and
- ASTM A 792, Standard Specification for Steel Sheet, 55% Aluminum-Zinc Alloy-coated by the Hot-dip Process.
Other coatings for steel
Other coatings for steel include ‘Galfan,’ which is about 95 percent zinc by volume (almost reciprocal of Galvalume) and terne, which is a solderable tin-lead alloy used over special copper-bearing steel in thin gauges. The latter has been around for more than a century. Its advantages include solderability and a combination of steel’s cost efficiency with the ductility of softer metals.
Both Galfan and terne are only used in painted applications. The former is always pre-painted and the latter is most often post-painted using special paint, although it can also be pre-painted by coil coating. Post-painted terne requires repainting at about six- to eight-year intervals. Newer terne coatings (‘Terne II’ by trade name) are tin-zinc, rather than tin-lead alloys.
Excellent article Rob.