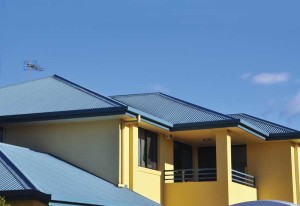
Photo © Dreamstime.com
Limitations of coated steel products
Aside from drainage issues, other precautionary measures when using metallic-coated steel are primarily chemical and metallurgical. Contact of these coatings with strong acids should be avoided. Heavy discharge of sulfurous and nitrous oxides from flues and the like shortens coating life adjacent to those areas. When using aluminum or aluminum alloy, strong alkalis are also detrimental to the aluminum. For this reason, use of these products with wet portland cement mortars such as reglet flashings is precluded, unless the metallic coating is first protected with a good, heavy layer of spray- or brush-applied clear coating (e.g. acrylic) to protect it until the mortar cures.
When work adjacent to Galvalume or Aluminized (or aluminum) involves cement mortar, the trades should be sequenced so the masonry installers finish their work prior to placement of metal panels. Cured mortar poses no threat.
There are also some mechanical precautions to be observed. Warranties on Galvalume usually specify a minimum bend radius of ‘2T’ in fabricated shapes—the radius of a bend must be at least double the metal thickness. This is because the material is stretched into tension on the outside of the radius and may develop micro-fractures if such a minimum were not observed. G-90 is a little more flexible and tolerates a tighter radius.
Aluminized (and aluminum sheet) are less ductile and may require even greater bend radii. In most cases, the tooling of roll-forming equipment anticipates these limitations, so there is no need for concern. However, there are exceptions. Sometimes panels or related flashings are brake-formed. Common leaf-brakes often violate the minimum bend restrictions of some coated steel products. The result may be thinning of the coating, micro-fractures, and premature corrosion at tension (outside radius) bends.
Weldability
Contrary to many industry claims, coated steel cannot be welded. Steel can be welded; coated steel cannot. This is because when attempts are made to weld coated steel in a fabrication or manufacturing process, the first step is to completely remove all coating from the area to be welded. Having done that, it is no longer coated steel, but bare steel, and the integrity of the metallic coating cannot be adequately restored.
The weld must be protected from corrosion, however, so the fabricator often employs a brush-applied, air-dried paint of sorts (sometimes with zinc or aluminum particulate) for the necessary corrosion protection. This secondary applied coating never has the life or maintenance freedom of the original hot-dip metallic coating. Except in rare cases, such specification is obsolete and a customer disservice. Instead, weldable materials should be specified for such conditions metallurgically compatible with the coated steel roof panels.
Compatibility issues
Zinc and aluminum are both anodic metals and should be isolated from electrolytic contact with more noble or cathodic metals, most notably copper. For the contractor, this means copper flashings should not be used anywhere upstream or in electrolytic contact with the coated steel. Additionally, any mounted equipment involving copper lines that drips condensate or rainwater runoff onto the roof should be avoided at all cost.
Runoff from copper contains copper salts, causing rapid galvanic corrosion of any of these coatings. It is not unusual to see a trail of red rust downslope of a roof-mounted air conditioner after a few years of service. Copper lines should be jacketed with insulation to prevent condensate drippage or rainwater runoff. Alternatively, runoff can be collected in a condensate pan and directed to drains by polyvinyl chloride (PVC) piping, isolating it from the roof panels.
Another common mistake is the use of graphite pencil to mark aluminum-, Aluminized-, or Galvalume-coated steel. Graphite has a severe corrosive effect on aluminum and etches the surface. In the case of coated steel and a wet climate, heavy pencil marks may show red rust in as little as one year. Instead, a felt-tip marker should be used for layout lines and other markings.
A galvanic scale can be used for determining dissimilar metals, and is included in many reference materials. However, the user should be aware this tool does not tell the whole truth. It is a mistake to conclude galvanic corrosion is imminent based on the scale alone. For instance, lead is distant (cathodic) from zinc (anodic) on the scale; but zinc may be soldered with lead alloy without adverse effects. Nickel steel is distant from both zinc and aluminum, but stainless fasteners are not only used, but are also preferred for these metals. Aluminum nails can be used in galvanized steel, but the reciprocal presents a problem.
Metals’ compatibility is too complex to be assessed merely by a quick look at the galvanic scale. Contributing to the complexity is formation of oxide layers that have different characteristics than the base metal. Galvalume producers have always recommended avoiding contact with lead flashings. However, in practice, lead reglet flashing (for instance) rarely affects Galvalume roofing adversely.
The best approach is to ask more questions if metals are found to be distant on the scale. Although coated steel panels are a popular choice for coastal applications, users should be aware of the detrimental effects salt spray has on all these coatings—they simply cannot yield the kind of life mentioned earlier in this type of environment.
Adequate drainage
None of the coatings described in this article tolerate moisture trapped against their surface for prolonged periods. Zinc is markedly less tolerant of this than aluminum, but both benefit from being freely drained and readily air-dried. Warranties typically exclude under-side corrosion. This can result from prolonged exposure of the panels’ underside to wet felts and deck (which is usually the result of leakage).
Topside corrosion can also be induced from the same phenomena where water ponds on the panel or where leaves, pine straw, or other debris retain moisture on the coating’s surface for a time. Occasional inspection and routine cleaning if necessary goes a long way toward preventing such induced coating corrosion. Thanks to its excellent strength-to-weight ratio and good formability and paintability characteristics, coated steel is the most widely used of all metals for roof coverings in the United States. Further, the material is durable enough for engineered, structural applications over open framing. Other factors being equal, coated carbon steel can offer superior wind uplift performance due to their mechanical properties. In many environments the metal can have a service life of four decades or more, and is a cost-compelling choice.
Robert M. Haddock, CSI, is a spokesperson for The Metal Initiative and the president of the Metal Roof Advisory Group. A consultant, technical writer, training curriculum author, inventor, and educator, Haddock is faculty at the National Roofing Contractors Association’s (NRCA’s) Roofing Industry Educational Institute (RIEI), and is also a member of ASTM International, the Construction Specifications Institute (CSI), and the Metal Construction Association (MCA). He can be contacted via e-mail at rmhaddock@earthlink.net.
Excellent article Rob.