Material considerations
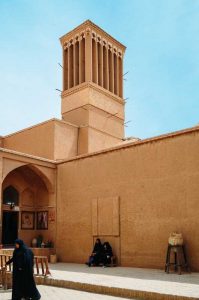
Photo © BigStockPhoto.com
Architectural millwork uses a wide variety of materials for both cores and finishes. One thing these materials share is they expand and contract in response to temperature and/or RH. Wood-based materials, including solid lumber, wood veneers, and engineered wood cores, all move primarily in response to changes in moisture content. Alternatively, solid surface materials, metal laminates, and synthetic stone materials move in response to temperature, but are not affected by RH. Contrary to expectation, high-pressure laminates respond primarily to RH, like wood products.
Core materials are typically engineered wood products. Particleboard, medium-density fiberboard (MDF), and veneer core plywood are all typical cores for casework and paneling. Each has its own strengths and weaknesses. Veneer core plywood is the most dimensionally stable; the longitudinal fibers of the veneer layers move the least with changes in moisture content. However, plywood is more likely to warp than other engineered cores. For this reason, the North American Architectural Woodwork Standards (NAAWS) recommends against its use in doors. It is suitable for other applications (The North American Architectural Woodwork Standards [NAAWS] is a joint publication of the Woodwork Institute [WI] and the Architectural Woodwork Manufacturers Association of Canada [AWMAC]).
MDF and particleboard show more change in dimension than plywood. The NAAWS calls out an allowance for movement of 0.0039 x linear dimension for movement. This may sound like a small number, but consider a standard 1 x 2-m (4 x 8-ft) panel. The potential movement on the long axis calculates to 9.5 mm (3/8 in.). It is not a big factor in smaller pieces, but in a larger fabrication like an expanse of paneling, it becomes important.
Face materials have their own characteristics. High-pressure laminates expand and contract about half as much as MDF or particleboard. Low-pressure laminates do not have significant tensile strength, and typically move with the core material. Therefore, it is important to have balanced panel construction in cabinets and millwork. If a panel has high-pressure laminate on one side, and low-pressure laminate or nothing at all on the other side, it is almost certain to warp when RH changes. Wood veneers behave like high-pressure laminates, but they are more rigid parallel to the grain than across the grain. Their strength is in tension, not compression. There is potential for buckling or cracking to occur if there are large changes in conditions.
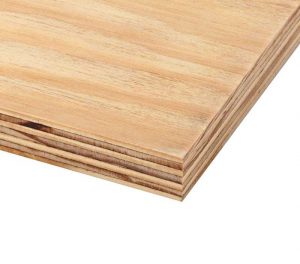
Photo courtesy Woodwork Institute
Solid metal laminates are different. They are one layer of metal, typically aluminum, copper, or brass. This metal layer may have thin, low-pressure laminate backer or no backer at all and differ from metal laminates using a thin metal face bonded to a traditional high-pressure laminate backer. Solid metal laminates respond to changes in temperature, but not to differences in RH. If there is a long run in one direction, coupled with a change in RH, there can be serious problems. The use of these materials should be carefully considered, as they are best in situations with minimal swings in temperature and humidity.
Solid surface materials (filled cast polymeric resin panels) respond to temperature and are unaffected by humidity. They are most often used for countertops, but larger and more complex fabrications are becoming common. Manufacturers recommend 3-mm (1/8-in.) gaps at joints to walls to allow for movement, with flexible caulking to fill gaps.
Hardwood or softwood lumber is typically used in trim, including running trim (base, crown, casings) and built-up items like grill work, sash, and stile and rail doors. Solid stock movement is more complex; movement is anisotropic, with different percentages of movement with the grain (longitudinal), parallel to the growth rings (tangential) and perpendicular to the growth rings (radial). Longitudinal movement is small and can usually be disregarded, but parallel to the growth rings, it can be significant. For example, an ash board 304 mm (12 in.) wide would expand by 4.2 mm (5/32 in.) when going from 5 to 10 percent moisture content. Designs must allow for this movement to avoid problems.